Method for extracting metal from coal ash by fused salt electrolysis method
A molten salt electrolysis and metal extraction technology, applied in the field of metallurgy, can solve the problems of low purification rate, unrecyclable alkali reactant, equipment corrosion, etc., and achieve the effects of simple process, green and efficient comprehensive utilization, and short process.
- Summary
- Abstract
- Description
- Claims
- Application Information
AI Technical Summary
Problems solved by technology
Method used
Image
Examples
Embodiment 1
[0034] Na 3 AlF 6 and AlF 3 Mix evenly to make cryolite-based molten salt, the mixing ratio is NaF and AlF in cryolite-based molten salt 3 The molar ratio is 2;
[0035] Put the metal aluminum in the electrolytic cell; then place the cryolite-based molten salt in the electrolytic cell, and then add fly ash, the amount of fly ash added is 5% of the total weight of the cryolite-based molten salt and fly ash; The composition of fly ash contains Al by weight percentage 2 o 352.75%, SiO 2 38.05%, CaO 3.88%, TiO 2 1.97%, Fe 2 o 3 1.86%, MgO 0.51%, K 2 O 0.10%, the balance is impurity;
[0036] Heating cryolite-based molten salt and fly ash to 910°C, metal aluminum is melted into liquid aluminum, the liquid aluminum is used as the cathode, and the carbon anode is used as the anode; electrolysis is carried out by electrification, and the current density between the cathode and the anode is controlled to be 0.4A / cm 2 , the electrolysis time is 8h. After starting the ele...
Embodiment 2
[0039] The method that molten salt electrolysis extracts metal from fly ash is the same as embodiment 1, and difference is:
[0040] (1) NaF and AlF in cryolite-based molten salt 3 The molar ratio is 2.2;
[0041] (2) The amount of fly ash added to the electrolytic cell is 3% of the total weight of cryolite-based molten salt and fly ash; the composition of fly ash contains Al 2 o 3 39.04%, SiO 2 55.24%, CaO 0.25%, TiO 2 0.77%, Fe 2 o 3 3.76%, MgO 0.10%, K 2 O 0.01%, the balance is impurity;
[0042] (3) Heat cryolite-based molten salt and fly ash to 955°C, use an inert anode as the anode, and the inert anode is a metal-based aluminum electrolytic inert anode; electrify for electrolysis, and the current density between the cathode and the anode is 0.6A / cm 2 , the electrolysis time is 7h; the amount of fly ash added each time is 30% of the total weight of fly ash in the electrolytic cell when electrolysis is started;
[0043] (4) The composition of the aluminum-bas...
Embodiment 3
[0045] The method that molten salt electrolysis extracts metal from fly ash is the same as embodiment 1, and difference is:
[0046] (1) NaF and AlF in cryolite-based molten salt 3 The molar ratio is 2.4;
[0047] (2) The amount of fly ash added to the electrolytic cell is 10% of the total weight of cryolite-based molten salt and fly ash; the composition of fly ash contains Al by weight percentage 2 o 3 47.11%, SiO 2 34.30%, CaO 3.90%, TiO 2 1.86%, Fe 2 o 3 6.20%, MgO 3.70%, K 2 O 2.10%, the balance is impurity;
[0048] (3) Heat cryolite-based molten salt and fly ash to 965°C; electrify for electrolysis, and the current density between the cathode and anode is 0.7A / cm 2 , the electrolysis time is 6h; the amount of fly ash added each time is 40% of the total weight of fly ash in the electrolytic cell when the electrolysis is started;
[0049] (4) The composition of the aluminum-based alloy contains Al 67.9%, Si 17.9%, Fe 5.4%, Ti 8.4% by weight percentage, and the...
PUM
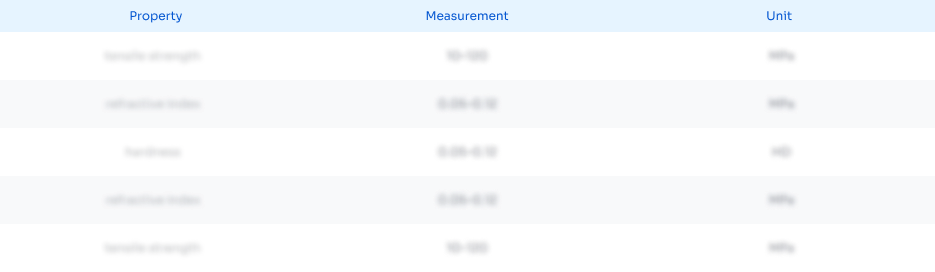
Abstract
Description
Claims
Application Information

- R&D Engineer
- R&D Manager
- IP Professional
- Industry Leading Data Capabilities
- Powerful AI technology
- Patent DNA Extraction
Browse by: Latest US Patents, China's latest patents, Technical Efficacy Thesaurus, Application Domain, Technology Topic, Popular Technical Reports.
© 2024 PatSnap. All rights reserved.Legal|Privacy policy|Modern Slavery Act Transparency Statement|Sitemap|About US| Contact US: help@patsnap.com