Reversible covalent cross-linked epoxy resin and preparation method thereof
A technology of epoxy resin and covalent crosslinking, which is applied in the field of reversible covalent crosslinking epoxy resin and its preparation, and can solve the problems of many reaction steps, low Young's modulus or elongation at break of epoxy resin materials, etc. , to achieve the effect of simple conditions, easy implementation, and relatively low cost
- Summary
- Abstract
- Description
- Claims
- Application Information
AI Technical Summary
Problems solved by technology
Method used
Image
Examples
Embodiment 1
[0027] A kind of preparation method of reversible covalent crosslinking epoxy resin, epoxy resin monomer selects bisphenol A diglycidyl ether, and the steps are as follows:
[0028] 1) At room temperature, add 38g of bisphenol A diglycidyl ether and 10g of 2-furylmethylamine into a 100mL single-necked round bottom flask and stir well, then pour it into a polytetrafluoroethylene mold and place it in a vacuum protected by argon In an oven, react at room temperature for 12 hours, then heat to 65°C for 8 hours to obtain a light yellow transparent solid that is a linear epoxy resin;
[0029] 2) Demould the obtained linear epoxy resin at room temperature and dissolve it in 200mL of N,N'-dimethylacetamide, add 18g of N,N'-(4,4'-methylenediphenyl) Bismaleimide, after stirring evenly, pour it into a mold placed in a vacuum oven, remove the N,N'-dimethylacetamide solvent under vacuum conditions, and then react at 60°C for 20 hours to obtain a yellow transparent solid It is a reversible...
Embodiment 2
[0033] A kind of preparation method of reversible covalent cross-linking epoxy resin, epoxy resin monomer selects polyethylene glycol diglycidyl ether, and the steps are as follows:
[0034] 1) Add 10.5g polyethylene glycol diglycidyl ether (number average molecular weight: 526), 1.9g 2-furylmethylamine and 40mL tetrahydrofuran into a 100mL single-necked round bottom flask at room temperature, stir well, and store at 60°C under nitrogen protection After reacting for 24 hours, the tetrahydrofuran solvent was removed by rotary evaporation, and the obtained yellow liquid was linear polyethylene glycol with a furan group in the side chain;
[0035] 2) Dissolve the obtained linear polyethylene glycol with furan group in the side chain into 20mL N,N'-dimethylacetamide at room temperature, add 7.1g N,N'-(4,4'- Methyl diphenyl) bismaleimide, after stirring evenly, pour it into a mold placed in a vacuum oven, remove the N, N'-dimethylacetamide solvent under vacuum conditions, and the...
PUM
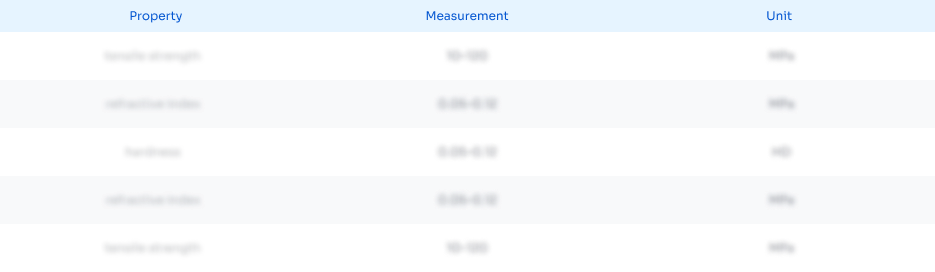
Abstract
Description
Claims
Application Information

- R&D
- Intellectual Property
- Life Sciences
- Materials
- Tech Scout
- Unparalleled Data Quality
- Higher Quality Content
- 60% Fewer Hallucinations
Browse by: Latest US Patents, China's latest patents, Technical Efficacy Thesaurus, Application Domain, Technology Topic, Popular Technical Reports.
© 2025 PatSnap. All rights reserved.Legal|Privacy policy|Modern Slavery Act Transparency Statement|Sitemap|About US| Contact US: help@patsnap.com