Micro-pore polarity induction absorbent for regeneration treatment on electric power oil and preparation method of micro-pore polarity induction absorbent
A technology for power oil and adsorbent, which is applied in the field of power oil regeneration treatment of microporous polarity-inducing adsorbent and its preparation, can solve the problems of limited effect, limited types of deterioration products, large pore size of adsorption medium, etc.
- Summary
- Abstract
- Description
- Claims
- Application Information
AI Technical Summary
Problems solved by technology
Method used
Image
Examples
Embodiment 1
[0044] The cetyltrimethylammonium bromide of 36.4g is dissolved in the aqueous ethanol solution of 300ml (Wt 乙醇 =20%), adjust the pH value of the solution to 11 with ammonia water to obtain an alkaline solution; take 57.6g of SiO 2 2H 2 O and 85.8g of Al(OH) 3 Dissolve in the above alkaline solution in a water bath at 60°C, stir for 10 hours, and the speed of the stirring paddle is 800 r / min; after the solution is evenly stirred, add 0.5 g of elemental boron, and continue stirring for 10 hours. After the boron doping is uniform, the solution is moved into a stainless steel autoclave lined with polytetrafluoroethylene, distilled water is added, the water level is controlled at 80% of the height of the reactor, and the constant temperature of the blast drying oven is controlled at 150°C, and the hydrothermal reaction is carried out for 18 hours , A white gel-like substance was obtained after the reaction. Wash the white gel-like substance and place it in a tubular heating fur...
Embodiment 2
[0050] 48.2g of cetyltrimethylammonium chloride was dissolved in 400ml of deionized water, and the pH value of the solution was adjusted to 10 with sodium bicarbonate to obtain an alkaline solution; 70g of tetraethyl orthosilicate and 51.4g of Al 2 o 3 Dissolve in the above alkaline solution in a water bath at 80°C and stir for 15 hours at a stirring speed of 1200r / min; add 0.68g of elemental boron to the solution and continue stirring for 10 hours; transfer the mixed solution into a high-pressure reactor, Control the constant temperature of the blast drying oven at 180° C., and carry out the hydrothermal reaction for 24 hours. After the reaction, a white gel-like substance is obtained. The white gel was repeatedly washed with ethanol and deionized water, and then calcined in a muffle furnace at 800°C for 6 hours to obtain a white blocky solid. Control the temperature of the muffle furnace at 1700°C to melt the white blocky solid. Add 41g of graphite to the liquid and dispers...
Embodiment 3
[0055] Dissolve 28.5g of cetyltrimethylammonium bromide and 19.4g of octadecyltrimethylammonium chloride in 500ml of deionized water, adjust the pH value of the solution to 8 with glacial acetic acid; add 170g of kaolin, at 70°C Stir in a water bath for 24 hours, the stirring speed is controlled at 1500r / min; add 0.8g elemental boron to the mixed solution, and continue to stir for 10 hours; move the boron-doped mixed solution into the reaction kettle, control the temperature at 220°C, and adjust the water volume in the reaction kettle To normal, carry out hydrothermal reaction for 36h; wash the white gel after hydrothermal reaction with absolute ethanol and deionized water successively, control the temperature of the tubular heating furnace at 800°C, and calcinate the white gel for 10h, The obtained white solid calcined product is then heated and melted in a muffle furnace at 1600°C, and 37g of graphite is added to the molten liquid to make holes. Carry out secondary calcinati...
PUM
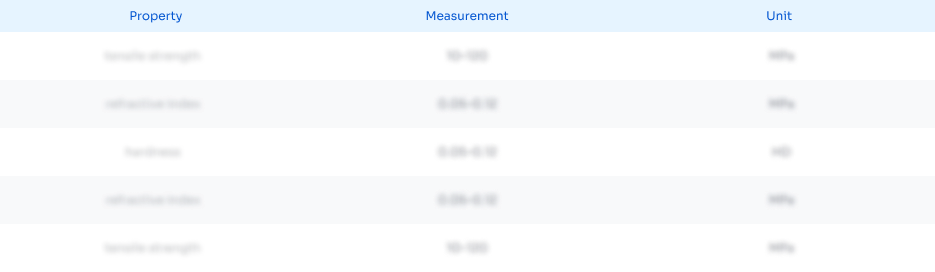
Abstract
Description
Claims
Application Information

- R&D
- Intellectual Property
- Life Sciences
- Materials
- Tech Scout
- Unparalleled Data Quality
- Higher Quality Content
- 60% Fewer Hallucinations
Browse by: Latest US Patents, China's latest patents, Technical Efficacy Thesaurus, Application Domain, Technology Topic, Popular Technical Reports.
© 2025 PatSnap. All rights reserved.Legal|Privacy policy|Modern Slavery Act Transparency Statement|Sitemap|About US| Contact US: help@patsnap.com