Method and device for reducing, extracting and separating rear earth through fused salt and liquid metal
A technology of liquid metal and liquid metal phase, which is applied in the field of rare earth separation devices, can solve the problems of difficulty in meeting separation requirements, high fuel consumption, and high radiation in the post-processing process, and achieve equipment miniaturization, resource saving, and small material volume Effect
- Summary
- Abstract
- Description
- Claims
- Application Information
AI Technical Summary
Problems solved by technology
Method used
Image
Examples
Embodiment 1
[0026] Example 1. a. Preparation of reducing agent: liquid aluminum is used for the cathode, and a spectrally pure graphite rod is used for the anode, and the mixture of low eutectic KCl-LiCl (51:43% by mass fraction) is added to the electrolytic cell and heated and melted as an electrolyte , at 800°C, constant current electrolysis was carried out, and the cathode current density was 1.3A cm -2 , Tank voltage 4.0-5.5V. After 300 minutes of electrolysis, the cathode electrolyzes to obtain lithium, which is dissolved in 4.8wt% of liquid aluminum to obtain a liquid aluminum-lithium alloy; b, extraction reaction: take out the anode and molybdenum wire, use the obtained liquid aluminum-lithium alloy as an extractant, and add 0.6 wt% of PrCl 3 , 0.6wt% SmCl 3 , The volume ratio of the molten salt containing mixed rare earth chloride to the liquid metal phase is 29:1. Open the inflation valve, fill with argon, the inflation rate is 5L / min, and under the protection of argon atmosph...
Embodiment 2
[0027]Example 2: a. Preparation of reducing agent: Liquid aluminum is used for the cathode, and a spectroscopically pure graphite rod is used for the anode, and the mixture of low eutectic KCl-LiCl (51:43% by mass fraction) is added to the electrolytic cell and heated and melted as an electrolyte , at 900°C, constant current electrolysis was carried out, and the cathode current density was 1.3A cm -2 , Tank voltage 4.0-5.5V. After 240 minutes of electrolysis, the cathode electrolyzes to obtain lithium, which is dissolved in 3.7wt% of liquid aluminum to obtain a liquid aluminum-lithium alloy; b, extraction reaction: take out the anode and molybdenum wire, use the obtained liquid aluminum-lithium alloy as an extractant, and add 1.5 wt% of PrCl 3 , 0.8wt% SmCl 3 , The volume ratio of the molten salt containing mixed rare earth chloride to the liquid metal phase is 35:1. Open the inflation valve, fill with argon, the inflation rate is 3L / min, and under the protection of argon a...
Embodiment 3
[0028] Example 3: a. Preparation of reducing agent: Liquid aluminum is used for the cathode, and a spectrally pure graphite rod is used for the anode, and the mixture of low eutectic KCl-LiCl (50.5:43% by mass fraction) is added to the electrolytic cell and heated and melted as an electrolyte , at 900°C, constant current electrolysis was carried out, and the cathode current density was 1.3A cm -2 , Tank voltage 4.0-5.5V. After 300 minutes of electrolysis, the cathode electrolyzes to obtain lithium, which is dissolved in 4.5wt% of liquid aluminum to obtain a liquid aluminum-lithium alloy; b, extraction reaction: take out the anode and molybdenum wire, use the obtained liquid aluminum-lithium alloy as an extractant, and add 0.8 wt% of PrCl 3 , 1.2wt% SmCl 3 , The volume ratio of molten salt containing mixed rare earth chloride to liquid metal phase is 29:1. Open the inflation valve, fill with argon, the inflation rate is 5L / min, and under the protection of argon atmosphere, s...
PUM
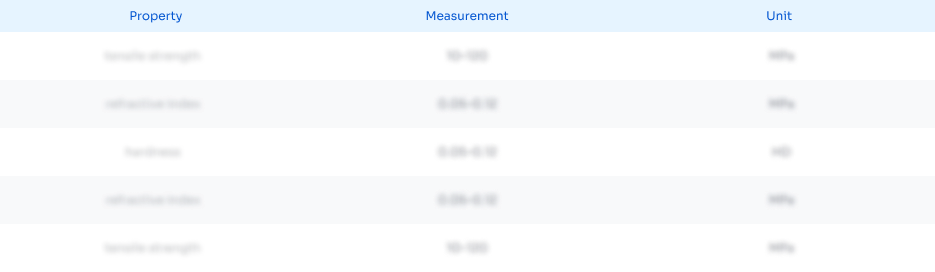
Abstract
Description
Claims
Application Information

- R&D Engineer
- R&D Manager
- IP Professional
- Industry Leading Data Capabilities
- Powerful AI technology
- Patent DNA Extraction
Browse by: Latest US Patents, China's latest patents, Technical Efficacy Thesaurus, Application Domain, Technology Topic, Popular Technical Reports.
© 2024 PatSnap. All rights reserved.Legal|Privacy policy|Modern Slavery Act Transparency Statement|Sitemap|About US| Contact US: help@patsnap.com