Waterborne polyurethane, preparation method therefor and waterborne transfer painting
A technology for water-based polyurethane and transfer coatings, applied in the field of coatings, can solve the problems of environmental pollution, hidden dangers in production safety, and high cost and price of organic solvents
- Summary
- Abstract
- Description
- Claims
- Application Information
AI Technical Summary
Problems solved by technology
Method used
Image
Examples
preparation example Construction
[0022] The embodiment of the present invention discloses a kind of preparation method of waterborne polyurethane, comprises the following steps:
[0023] A) reacting isophorone diisocyanate with polyester diol to obtain a prepolymer;
[0024] B) performing chain extension reaction after mixing the prepolymer, alcohol chain extender and hydrophilic chain extender;
[0025] C) Mix the compound and salt-forming agent obtained in step B) with water, and react to obtain water-based polyurethane.
[0026] The invention provides a method for preparing water-based polyurethane. According to the invention, before preparing the water-based polyurethane, raw materials are strictly selected.
[0027] Aromatic water-based polyurethane is similar to oil-based polyurethane, which has obvious yellowing and poor weather resistance, and is a low-end popular product; aliphatic water-based polyurethane has good color retention and weather resistance, but the price is high, and it is a high-end p...
Embodiment 1
[0049] Distill 200g of polycaprolactone diol at 130°C for 2h and then cool down to room temperature, add 150g of isophorone diisocyanate and 2g of stannous octoate to react at 80-140°C for 2-3h, After cooling down, add 15g of dimethylolpropionic acid and 10g of 1,4-butanediol and continue the reaction for 4 to 8 hours, then cool down and add 20g of triethylamine and 50g of N-methylpyrrolidone as salt forming agents, and finally add 553g of deionized water to carry out Chain extension to obtain water-based polyurethane.
Embodiment 2
[0051] Distill 160g of polycaprolactone diol at 130°C for 2h and then cool down to room temperature, add 180g of isophorone diisocyanate and 5g of stannous octoate to react at 80-140°C for 2-3h, After cooling down, add 20g of dimethylolpropionic acid and 15g of 1,4-butanediol and continue the reaction for 4 to 8 hours, then cool down and add 25g of triethylamine and 55g of N-methylpyrrolidone as salt-forming agents, and finally add 540g of deionized water to carry out Chain extension to obtain water-based polyurethane.
PUM
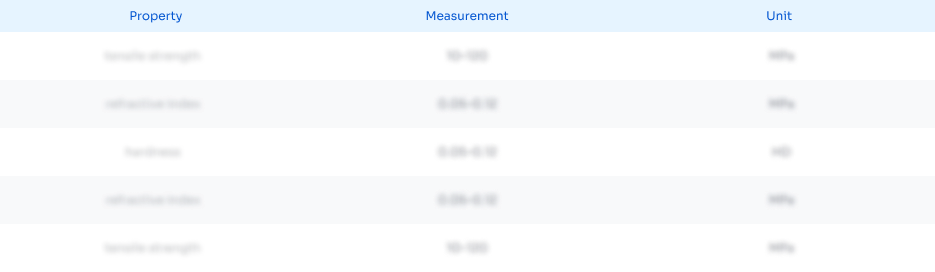
Abstract
Description
Claims
Application Information

- Generate Ideas
- Intellectual Property
- Life Sciences
- Materials
- Tech Scout
- Unparalleled Data Quality
- Higher Quality Content
- 60% Fewer Hallucinations
Browse by: Latest US Patents, China's latest patents, Technical Efficacy Thesaurus, Application Domain, Technology Topic, Popular Technical Reports.
© 2025 PatSnap. All rights reserved.Legal|Privacy policy|Modern Slavery Act Transparency Statement|Sitemap|About US| Contact US: help@patsnap.com