Preparation method of hexafluorobenzene and chloropentafluorobenzene
A technology of chloropentafluorobenzene and chloropentafluorobenzene, which is applied in the field of preparation of hexafluorobenzene and chloropentafluorobenzene, can solve the problems of unfavorable industrial production, coking of reactors, and low conversion rate, and achieve a process synthesis route Short, avoid coking, less loss effect
- Summary
- Abstract
- Description
- Claims
- Application Information
AI Technical Summary
Problems solved by technology
Method used
Image
Examples
Embodiment 1
[0048] In the reactor, add raw material hexachlorobenzene 130g, active potassium fluoride 260g, and catalyst tetrakis (diethylamino) phosphonium bromide 1.3g, after dehydrating with dichloromethane, add dry benzonitrile 130g, after the addition is completed, put The reactor is heated up slowly to 580°C and kept at constant temperature for 30 hours. The reaction pressure is 8.0-8.2Mpa. Stop heating. When the temperature drops to 300°C, open the valve to evaporate the reactant and solvent together and condense for recovery. Record the productive rate data of reaction product and see Table 1:
[0049] Table I:
[0050] Example
C 6 f 6 ,%
C 6 f 5 C1,%
Other fluorochlorobenzenes, %
Other high boiling substances, %
1
31.6
30.3
33.3
4.8
[0051] Other fluorochlorobenzenes refer to: C 6 f 4 C1 2 、C 6 f 3 C1 3 、C 6 f 2 C1 4 、C 6 FC1 5 Wait.
[0052] Other high boilers refer to products other than fluorochlorobe...
Embodiment 2、3、4、5
[0054] According to the operation steps of Example 1, keeping other reaction conditions unchanged, respectively controlling the reaction temperature to 500°C, 550°C, 600°C, and 650°C, the yield data of the measured reaction products are shown in Table 2:
[0055] Table II:
[0056] Example
Embodiment 6、7、8
[0058] According to the operation steps of Example 1, keep other reaction conditions unchanged, respectively control the ratio of the mass of hexachlorobenzene and catalyst to 1:005, 1:0.015, 1:0.03, and measure the yield data of reaction products in Table 3:
[0059] Table three:
[0060] Example
PUM
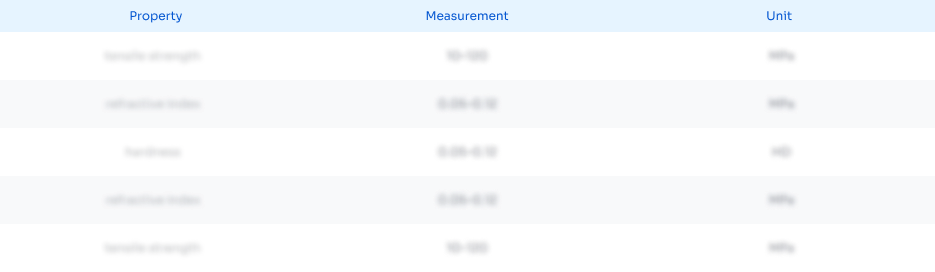
Abstract
Description
Claims
Application Information

- R&D
- Intellectual Property
- Life Sciences
- Materials
- Tech Scout
- Unparalleled Data Quality
- Higher Quality Content
- 60% Fewer Hallucinations
Browse by: Latest US Patents, China's latest patents, Technical Efficacy Thesaurus, Application Domain, Technology Topic, Popular Technical Reports.
© 2025 PatSnap. All rights reserved.Legal|Privacy policy|Modern Slavery Act Transparency Statement|Sitemap|About US| Contact US: help@patsnap.com