Comprehensive recycling process for polymetallic material containing gold and silver
A multi-metal, gold and silver technology, applied in the direction of improving process efficiency, etc., can solve the problems of low gold and silver direct yield, long process flow, slow capital turnover, etc., and achieve simple process, simple equipment, and reduced consumption Effect
- Summary
- Abstract
- Description
- Claims
- Application Information
AI Technical Summary
Problems solved by technology
Method used
Image
Examples
Embodiment 1
[0039] The specific steps of a comprehensive recovery process of a gold-silver-containing polymetallic material are as follows:
[0040] (1) Raw material pretreatment: take 500g of raw material and grind it, which contains bismuth 6.32%, tin 7.58%, copper 8.12%, antimony 6.53%, lead 28.68%, silver 836.26g / t, gold 9.36g / t;
[0041] (2) Primary leaching: add 200 g of sulfuric acid, 100 g of ferric chloride, and 2000 g of water to the raw material; stir and react for 3.5 hours at a temperature of 85-95 °C, and filter to obtain 288.32 g of primary leaching residue; 1953.00 mL of primary leaching solution, of which Bismuth 15.56g / L, copper 19.86 g / L, tin 18.45 g / L;
[0042] (3) Separation of bismuth, copper and tin:
[0043] 3a Add sodium hydroxide to the primary leaching solution to adjust the pH to 2.5, share 57.10 g of sodium hydroxide, and filter to obtain 1898.00 mL of bismuth removal solution, 48.54 g of bismuth oxychloride (including 61.98% of bismuth), and the direct yield...
Embodiment 2
[0053] The specific steps of a comprehensive recovery process of a gold-silver-containing polymetallic material are as follows:
[0054] (1) Raw material pretreatment: take 10kg of raw material and grind it, which contains bismuth 8.62%, tin 28.18%, copper 6.53%, antimony 9.28%, lead 10.06%, silver 8362.48g / t, gold 50.34g / t;
[0055] (2) Primary leaching: add sulfuric acid 4kg, ferric chloride 2kg, and water 40kg to the raw material; stir and react for 3.5 hours at a temperature of 85-95° C. to obtain 4.32kg of primary leaching slag; 39.22L of primary leaching solution, wherein Bismuth 21.31g / L, copper 16.12g / L, tin 69.91g / L;
[0056] (3) Separation of bismuth, copper and tin:
[0057] 3a Add sodium hydroxide to the primary leaching solution to adjust the pH to 2.5, share 1.10 kg of sodium hydroxide, and filter to obtain 37.38 L of bismuth removal solution and 1.23 kg of bismuth oxychloride (including 67.32% of bismuth), and the direct yield of bismuth is 95.99% ;
[0058] ...
Embodiment 3
[0067] The specific steps of a comprehensive recovery process of a gold-silver-containing polymetallic material are as follows:
[0068] (1) Raw material pretreatment: take 10kg of raw material and grind it, which contains bismuth 6.31%, tin 3.14%, copper 10.53%, antimony 12.52%, lead 8.63%, silver 1032.23g / t, gold 89.53g / t;
[0069] (2) Primary leaching: add sulfuric acid 4kg, ferric chloride 2kg, 1 kg hydrochloric acid, and water 40kg to this raw material; filter to obtain primary leaching residue 3.82kg after stirring reaction under the condition of temperature 85-95 ℃ for 3 hours; primary leaching solution 38.68L, including bismuth 15.65g / L, copper 26.13g / L, tin 7.86g / L;
[0070] (3) Separation of bismuth, copper and tin:
[0071] 3a Add sodium hydroxide to the primary leaching solution to adjust the pH to 2.5, share 1.32kg of sodium hydroxide, filter to obtain 37.62L of bismuth removal solution, 0.88kg of bismuth oxychloride (including 68.53% of bismuth), and the direct ...
PUM
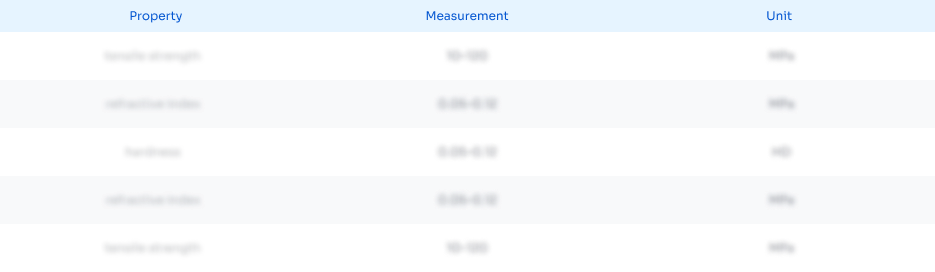
Abstract
Description
Claims
Application Information

- Generate Ideas
- Intellectual Property
- Life Sciences
- Materials
- Tech Scout
- Unparalleled Data Quality
- Higher Quality Content
- 60% Fewer Hallucinations
Browse by: Latest US Patents, China's latest patents, Technical Efficacy Thesaurus, Application Domain, Technology Topic, Popular Technical Reports.
© 2025 PatSnap. All rights reserved.Legal|Privacy policy|Modern Slavery Act Transparency Statement|Sitemap|About US| Contact US: help@patsnap.com