Process for recovering distillation waste liquid generated by producing 1,4-butanediol
A technology of butanediol and waste liquid, applied in the preparation of organic compounds, organic chemistry, chemical instruments and methods, etc., can solve the problems of inability to deal with salt content, underutilization of residual liquid, waste of waste liquid resources, etc. Broad market and application prospects, good for environmental protection, and high product recovery
- Summary
- Abstract
- Description
- Claims
- Application Information
AI Technical Summary
Problems solved by technology
Method used
Examples
Embodiment 1
[0023] A kind of production 1, the concrete steps of the recovery process of the distillation waste liquid of 4-butanediol are as follows:
[0024] (1) Salting-out-extraction
[0025] The distillation waste liquid produced in the refining process of 1,4-butanediol produced by the Rapper method is used as raw material, the waste water discharged during the production of 1,4-butanediol is used as the extraction agent, and sodium sulfate is used as the salting-out agent. The salting-out-extraction is carried out in an acidic (sulfuric acid) environment. That is, according to raw material: extractant: salting-out agent: the mass ratio of sulfuric acid with a mass concentration of 98% is 1: 0.8: 0.08: 0.04, the extractant is first added to the raw material, stirred and mixed evenly, and mixed into a mixed solution. Add sulfuric acid dropwise to the mixed solution, stir evenly, then add the salting-out agent to the mixed solution after adding the sulfuric acid dropwise, heat and st...
Embodiment 2
[0031] A recovery process for distillation waste liquid producing 1,4-butanediol, same as implementation case 1, wherein:
[0032] In the (1) step, the mass ratio of raw material: extractant: salting-out agent: mass concentration of 98% sulfuric acid is 1: 1: 0.7: 0.15, the temperature of the mixed solution is 40° C., and the stratification is allowed to stand for 30 minutes.
[0033] In step (2), the lower water phase was cooled and crystallized at 0° C. for 3 h, and the upper oil phase was cooled and crystallized at 5° C. for 5 h. First collect butanol by-products under the condition of 0.08MPa vacuum in the kettle; then collect 1,4-butanediol product under the condition of 0.096MPa vacuum in the kettle; then collect 3 under the condition of 0.096MPa vacuum in the kettle -tetrahydrofuran methanol by-product; finally, the fusel alcohol is collected under the condition of 0.096MPa vacuum in the kettle.
[0034] In step (3), the mass ratio of substrate at the bottom of the ket...
Embodiment 3
[0036] A recovery process for distillation waste liquid producing 1,4-butanediol, same as implementation case 1, wherein:
[0037] In step (1), the mass ratio of raw materials: extractant: salting-out agent: sulfuric acid with a mass concentration of 98% is 1:2:1.5:0.1, the temperature of the mixed solution is 50° C., and the mixture is allowed to stand for 20 minutes.
[0038] In step (2), the lower water phase was cooled and crystallized at -5°C for 2 hours, and the upper oil phase was cooled and crystallized at 0°C for 4 hours. First collect butanol by-products under the condition of 0.07MPa vacuum in the kettle; then collect 1,4-butanediol product under the condition of 0.095MPa vacuum in the kettle; then collect 3 under the condition of 0.095MPa vacuum in the kettle -tetrahydrofuran methanol by-product; finally, the fusel alcohol is collected under the condition of 0.095MPa vacuum in the kettle.
[0039] In step (3), the mass ratio of substrate at the bottom of the kettl...
PUM
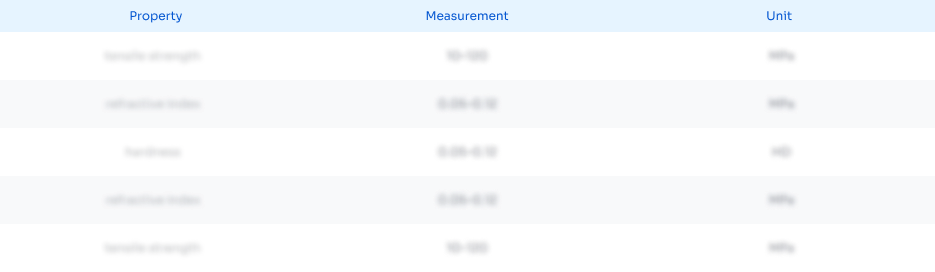
Abstract
Description
Claims
Application Information

- R&D
- Intellectual Property
- Life Sciences
- Materials
- Tech Scout
- Unparalleled Data Quality
- Higher Quality Content
- 60% Fewer Hallucinations
Browse by: Latest US Patents, China's latest patents, Technical Efficacy Thesaurus, Application Domain, Technology Topic, Popular Technical Reports.
© 2025 PatSnap. All rights reserved.Legal|Privacy policy|Modern Slavery Act Transparency Statement|Sitemap|About US| Contact US: help@patsnap.com