Iron-based amorphous powder and method for preparing coil-embedded integral-forming inductor
An amorphous powder, embedded technology, applied in the direction of inductance/transformer/magnet manufacturing, circuits, electrical components, etc., can solve the problems of scratching the insulating layer on the surface of the coil, high economy, coarse particle size of amorphous powder, etc. Achieve the effects of improving power supply efficiency, reducing core loss, and restoring magnetic performance
- Summary
- Abstract
- Description
- Claims
- Application Information
AI Technical Summary
Problems solved by technology
Method used
Image
Examples
Embodiment 1
[0064] The composition is Fe prepared by single-roll rapid quenching method 78 Si 9 B 13 The Fe-based amorphous thin ribbon was preheated at 350°C for 1 hour under a nitrogen atmosphere, and then compound crushed, and the -600 mesh ultrafine Fe-based amorphous powder was sieved, and the powder was crushed at 420 Vacuum stress relief annealing at ℃, heat preservation for 1h, then mixed with 5wt% cyanate and 0.6wt% zinc stearate, then sealed with 2.5 turns of flat coil, pressed under 600MPa pressure, the inductance size is 10mm square, The height is 4mm, and the curing treatment after the inductor is formed is: 80°C for 1h, 120°C for 1h. The inductance value of the prepared coil embedded integral molding is 0.45μH, Figure 4 It is the temperature rise saturation curve of the coil-embedded integrated inductor prepared from the ultrafine Fe-based amorphous powder in this embodiment.
[0065] As a comparison, a commercial coil-embedded integrated molded inductor (comparative ex...
Embodiment 2
[0068] The composition is Fe prepared by single-roll rapid quenching method 80 SiBC 2 The Fe-based amorphous thin ribbon was preheated at 350°C for 1 hour under a nitrogen atmosphere, and then compound crushed, and the -600 mesh ultrafine Fe-based amorphous powder was sieved, and the powder was crushed at 400 Vacuum stress relief annealing at ℃, heat preservation for 1h, then mixed with 5wt% cyanate and 0.6wt% zinc stearate, then sealed with 2.5 turns of flat coil, pressed under 600MPa pressure, the inductance size is 10mm square, The height is 4mm, and the curing treatment after the inductor is formed is: 80°C for 1h, 120°C for 1h. The inductance value of the prepared coil embedded integral molding is 0.45μH, Figure 5 It is the temperature rise saturation curve of the coil-embedded integrated inductor prepared from the ultrafine Fe-based amorphous powder in this embodiment.
[0069] As a comparison, a commercial coil-embedded integrated molded inductor (comparative exampl...
PUM
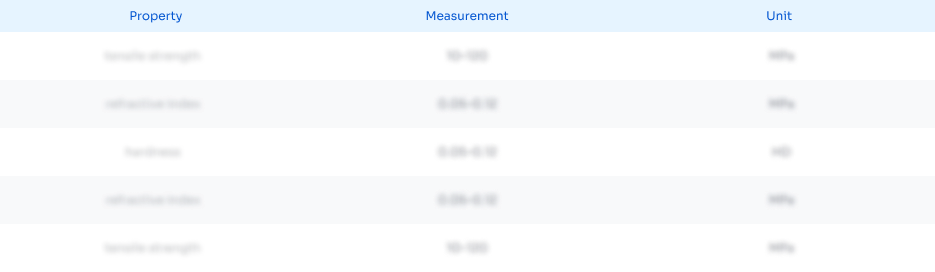
Abstract
Description
Claims
Application Information

- R&D
- Intellectual Property
- Life Sciences
- Materials
- Tech Scout
- Unparalleled Data Quality
- Higher Quality Content
- 60% Fewer Hallucinations
Browse by: Latest US Patents, China's latest patents, Technical Efficacy Thesaurus, Application Domain, Technology Topic, Popular Technical Reports.
© 2025 PatSnap. All rights reserved.Legal|Privacy policy|Modern Slavery Act Transparency Statement|Sitemap|About US| Contact US: help@patsnap.com