Wear-resistant SCR (Selective Catalytic Reduction) denitration catalyst and preparation method thereof
A denitrification catalyst and wear-resistant technology, which is applied in the direction of chemical instruments and methods, physical/chemical process catalysts, separation methods, etc., can solve the problems of wear-resistant strength cracking, collapse, catalyst wear, etc., to improve compactness and prolong service life The effect of improving the life and wear resistance
- Summary
- Abstract
- Description
- Claims
- Application Information
AI Technical Summary
Problems solved by technology
Method used
Image
Examples
Embodiment 1
[0018] The preparation method of the wear-resistant SCR denitration catalyst of the present embodiment comprises the following steps:
[0019] 1) Add 1.9kg aluminum isopropoxide to 1mol / L nitric acid solution to prepare hydrated alumina sol;
[0020] 2) Dry mix 39kg of titanium dioxide, 0.6kg of ammonium metavanadate and 2.65kg of ammonium metatungstate powder, and then add hydrated alumina sol, deionized water and oxalic acid to fully mix and stir;
[0021] 3) Add 7.4kg of silica sol with a mass fraction of 25% to the material obtained in step 2);
[0022] 4) Mix the materials obtained in step 3) evenly and add 2kg of structural additives;
[0023] 5) Extruding the material obtained in step 4), drying the carrier blank at 110° C. for 48 hours, and calcining at 550° C. for 10 hours to obtain the wear-resistant SCR denitration catalyst.
[0024] The main components and mass parts of the wear-resistant SCR denitration catalyst prepared in this example are: 89 parts of titanium...
Embodiment 2
[0026] The preparation method of the wear-resistant SCR denitration catalyst of the present embodiment comprises the following steps:
[0027] 1) Add 3.4kg aluminum isopropoxide to 1mol / L nitric acid solution to prepare hydrated alumina sol;
[0028] 2) Dry mix 33kg of titanium dioxide, 0.55kg of ammonium metavanadate and 2.4kg of ammonium metatungstate powder evenly, then add hydrated alumina sol, deionized water and oxalic acid to fully mix and stir;
[0029] 3) Add 12kg of silica sol with a mass fraction of 25% to the material obtained in step 2);
[0030] 4) Mix the materials obtained in step 3) evenly and add 2kg of structural additives;
[0031] 5) Extruding the material obtained in step 4), drying the carrier blank at 110° C. for 48 hours, and calcining at 550° C. for 10 hours to obtain the wear-resistant SCR denitration catalyst.
[0032] The main components and mass parts of the wear-resistant SCR denitration catalyst prepared in this example are: 85 parts of titani...
Embodiment 3
[0034] The preparation method of the wear-resistant SCR denitration catalyst of the present embodiment comprises the following steps:
[0035] 1) Add 8.3kg aluminum isopropoxide to 1mol / L nitric acid solution to prepare hydrated alumina sol;
[0036] 2) Dry mix 36kg of titanium dioxide, 0.55kg of ammonium metavanadate and 2.4kg of ammonium metatungstate powder evenly, then add hydrated alumina sol, deionized water and oxalic acid to fully mix and stir;
[0037] 3) Add 6.6kg of silica sol with a mass fraction of 25% to the material obtained in step 2);
[0038] 4) Mix the materials obtained in step 3) evenly and add 2kg of structural additives;
[0039] 5) Extruding the material obtained in step 4), drying the carrier blank at 110° C. for 48 hours, and calcining at 550° C. for 10 hours to obtain the wear-resistant SCR denitration catalyst.
[0040] The main components and mass parts of the wear-resistant SCR denitration catalyst prepared in this example are: 85 parts of titan...
PUM
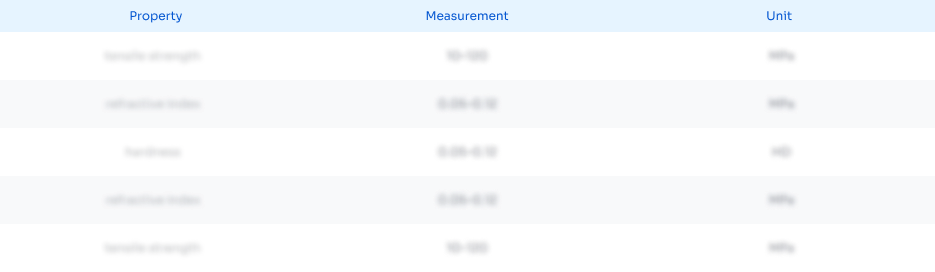
Abstract
Description
Claims
Application Information

- R&D
- Intellectual Property
- Life Sciences
- Materials
- Tech Scout
- Unparalleled Data Quality
- Higher Quality Content
- 60% Fewer Hallucinations
Browse by: Latest US Patents, China's latest patents, Technical Efficacy Thesaurus, Application Domain, Technology Topic, Popular Technical Reports.
© 2025 PatSnap. All rights reserved.Legal|Privacy policy|Modern Slavery Act Transparency Statement|Sitemap|About US| Contact US: help@patsnap.com