Organic piezoelectric damping coating and preparation method thereof
A damping coating and piezoelectric technology, applied in polyester coatings, epoxy resin coatings, polyurea/polyurethane coatings, etc., to achieve the effect of simple and easy process and good damping performance
- Summary
- Abstract
- Description
- Claims
- Application Information
AI Technical Summary
Problems solved by technology
Method used
Examples
preparation example Construction
[0023] The preparation method of the above-mentioned materials provided by the present invention is as follows: weigh the components according to the formula ratio, mix and disperse them, then add additives, mechanically stir and mix evenly, and finally polarize the formed piezoelectric organic coating in the electric field of a high-voltage direct-current oil bath .
[0024] The present invention will be further described below in conjunction with examples of implementation, but the present invention is not limited.
Embodiment 1~4
[0026] Treat lead titanate powder with silane coupling agent KH550, wash with ethanol aqueous solution, dry and grind; epoxy resin varnish includes main component epoxy resin 6101 solution and curing agent component epoxy resin curing agent T31. Add the treated lead titanate powder and carbon black into the epoxy resin 6101 solution according to the formula ratio, mechanically stir for 10 minutes at room temperature, and then put the mixture in an ultrasonic mixer at a temperature of 90°C and a frequency of 80Hz. Ultrasonic vibration for 3 hours, then add dispersant BYK-180, defoamer BYK-A530, drier JUST-2100 and epoxy resin curing agent T31 according to the formula ratio, and mix evenly to obtain epoxy resin piezoelectric damping coating. Put the sample in an oil bath for polarization, the polarization temperature is 100°C, the polarization voltage is 10kV / mm, and the polarization time is 30min. See Table 1 for the formulation proportions of Implementation Cases 1 to 4, and s...
Embodiment 5~8
[0028] Treat lead titanate powder with silane coupling agent KH550, wash with ethanol aqueous solution, dry and grind; unsaturated polyester varnish includes unsaturated polyester PE-988 solution as the main agent component and styrene as the curing agent component. Add the treated lead titanate powder and carbon black into the unsaturated polyester PE-988 solution according to the proportion of the formula, and mechanically stir for 10 minutes at room temperature, and then put the mixture in an ultrasonic mixer, at a temperature of 90°C and a frequency of Ultrasonic vibration at 80Hz for 3 hours, then add dispersant BYK-180, defoamer BYK-180 and curing agent styrene according to the formula ratio, and mix evenly to obtain unsaturated polyester piezoelectric damping coating. Put the sample in an oil bath for polarization, the polarization temperature is 100°C, the polarization voltage is 10kV / mm, and the polarization time is 30min. See Table 3 for the formulation proportions o...
PUM
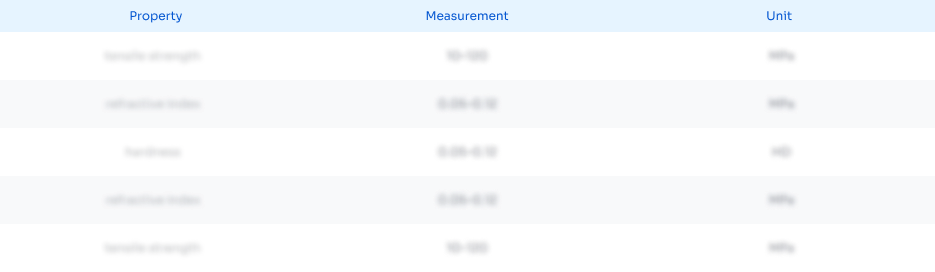
Abstract
Description
Claims
Application Information

- R&D
- Intellectual Property
- Life Sciences
- Materials
- Tech Scout
- Unparalleled Data Quality
- Higher Quality Content
- 60% Fewer Hallucinations
Browse by: Latest US Patents, China's latest patents, Technical Efficacy Thesaurus, Application Domain, Technology Topic, Popular Technical Reports.
© 2025 PatSnap. All rights reserved.Legal|Privacy policy|Modern Slavery Act Transparency Statement|Sitemap|About US| Contact US: help@patsnap.com