Microwave ceramic composition having anti-reduction characteristic, and microwave ceramic material thereof
A technology of microwave ceramics and components, applied in the field of microwave ceramic materials, can solve the problems of reducing the quality factor of dielectric ceramic materials and achieve the effect of low dielectric constant
- Summary
- Abstract
- Description
- Claims
- Application Information
AI Technical Summary
Problems solved by technology
Method used
Image
Examples
Embodiment 1
[0026] Example 1 Microwave Ceramic Material Comprising Zinc Oxide Addition
[0027] First, various pyroxene glass-ceramic materials with different phase structures are prepared by mixing at least two kinds of magnesium oxide (MgO), calcium oxide (CaO) and silicon dioxide (SiO 2 ) and other oxide powders, and formed after sintering at a temperature of 900 ° C, respectively CaSiO 3 (wollastonite), Ca 3 MgSi 2 o 8 (Rhodoxite), Ca 2 MgSi 2 o 7 (Akermanite) or CaMgSi 2 o 6 (diopside).
[0028]Then, taking the total amount of pyroxene glass-ceramic powder and zinc oxide powder as 100 mole percent, respectively take 3.5 to 6.5 mole percent (mole %), 7 to 10 mole percent (mole %), and 10.5 to 13.5 mole percent (mole percent) respectively. %) of zinc oxide powder, added to CaMgSi 2 o 6 Pyroxene glass-ceramic materials and mixed.
[0029] Afterwards, the sintering is continued for 2 hours at a sintering temperature of 900° C. in a nitrogen atmosphere to obtain the microwave ...
Embodiment 2
[0030] Example 2 Microwave Ceramic Material Containing Alumina Addition Components
[0031] In this embodiment, the microwave ceramic material containing alumina added components is prepared by the method of the above-mentioned embodiment 1. Pyroxene glass-ceramic material, and respectively take 3.5 to 6.5 mole percent (mole%), 7 to 10 mole percent (mole% ), 10.5 to 13.5 mole percent (mole%) of alumina powder to replace zinc oxide powder, to be added to CaMgSi 2 o 6 Pyroxene glass-ceramic materials and mixed.
[0032] Afterwards, the sintering is continued for 2 hours at a sintering temperature of 900° C. in a nitrogen atmosphere to obtain the microwave ceramic material of the present invention. Among them, the addition ratio of different alumina powders and the quality factor of the microwave ceramic material obtained after sintering at low sintering temperature and reducing atmosphere are shown in the above table 1, and the dielectric constant of the microwave ceramic mate...
Embodiment 3
[0033] Example 3 Microwave Ceramic Material Comprising Sodium Oxide Addition
[0034] The microwave ceramic material containing sodium oxide added components of this embodiment is to prepare the pyroxene glass-ceramic material according to the method of the above-mentioned embodiment 1, and respectively take 3.5 to 6.5 mole percent (mole%), 7 to 10 mole percent (mole%) %), 10.5 to 13.5 mole percent (mole%) of sodium oxide powder to replace zinc oxide powder, be added to CaMgSi 2 o 6 Pyroxene glass-ceramic materials and mixed.
[0035] Afterwards, the sintering is continued for 2 hours at a sintering temperature of 900° C. in a nitrogen atmosphere to obtain the microwave ceramic material of the present invention. Among them, the addition ratio of different sodium oxide powders and the quality factor of the microwave ceramic material after sintering at low sintering temperature and reducing atmosphere are shown in the above table 1, and the dielectric constant of the microwave...
PUM
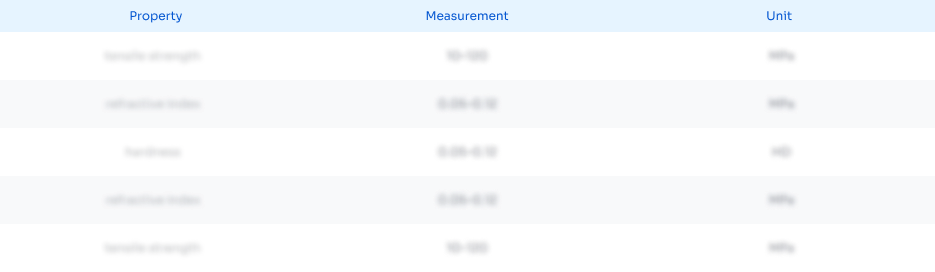
Abstract
Description
Claims
Application Information

- R&D
- Intellectual Property
- Life Sciences
- Materials
- Tech Scout
- Unparalleled Data Quality
- Higher Quality Content
- 60% Fewer Hallucinations
Browse by: Latest US Patents, China's latest patents, Technical Efficacy Thesaurus, Application Domain, Technology Topic, Popular Technical Reports.
© 2025 PatSnap. All rights reserved.Legal|Privacy policy|Modern Slavery Act Transparency Statement|Sitemap|About US| Contact US: help@patsnap.com