Method for producing superfine white carbon black, ferric hydroxide and aluminum oxide by using coal ash
A technology of iron hydroxide and fine white carbon black, applied in the directions of alumina/aluminum hydroxide, iron oxide/iron hydroxide, aluminum fluoride, etc., can solve the problem of low output of water treatment agent, inability to industrialize production, and single cost of material higher question
- Summary
- Abstract
- Description
- Claims
- Application Information
AI Technical Summary
Problems solved by technology
Method used
Image
Examples
experiment example 1
[0100] 1. Grinding: Grinding the fly ash to a grinder to a size below 200 microns to a dipping process;
[0101] 2. Extraction of aluminum and iron:
[0102] 2.1 First immersion: Put 100g of ground fly ash into a beaker, then add 700ml of hot water at 60°C according to the ratio of fly ash to 2Mol acid leaching solvent of 1:8, and then add 700ml of hot water at 60°C, then transfer the liquid-filled beaker into In the water bath filled with water, after adding 100ml 93% concentrated sulfuric acid under heating and stirring, the temperature of the solution in the beaker rises rapidly, at this time, add 22g of anhydrous NaF Afterwards, heating and leaching under stirring for 6 hours and then proceeding to the middle storage 1 process, the stirring speed is: 200 rpm; the temperature of the water bath is set at 95°C,
[0103] 2.2 Storage 1: Put the beaker with the mixed solution after immersion in the previous step outside the water bath for 10 minutes, and you can see the ash in ...
experiment example 2
[0146] 1. Grinding: same as in Experimental Example 1;
[0147] 2. Extraction of aluminum and iron:
[0148] 2.1 First immersion: Put 100g of ground fly ash into a beaker, then add 730ml of hot water at 60°C according to the ratio of fly ash to 3Mol acid leaching solvent of 1:9, and then add 730ml of hot water at 60°C, then press the After adding 16g of anhydrous NaF at a ratio of 100:16 by weight, move the liquid-filled beaker into a water bath filled with oil, and then add 170ml of 93% concentrated sulfuric acid according to the aforementioned solid-to-liquid ratio of concentrated sulfuric acid under heating and stirring. , the temperature of the solution in the reaction kettle rises rapidly, and the temperature of the preparation solution is controlled at about 120°C under stirring and heating leaching. After continuous leaching for 6 hours, it will go to the middle storage 1 process. The stirring speed is: 250 rpm; Hourly water replenishment 50ml;
[0149] 2.2 Storage 1:...
experiment example 3
[0189] 1. Grinding: same as in Experimental Example 1;
[0190] 2. Extraction of aluminum and iron:
[0191] 2.1 First immersion: Put 100g of ground fly ash into a beaker, and then add 60% of water according to the ratio of fly ash to 4Mol acid leaching solvent of 1:10 solid-to-liquid ratio. 。 After 770ml of C hot water, move the liquid-filled beaker into a water bath filled with oil, add 230ml of 93% concentrated sulfuric acid under heating and stirring, and the temperature of the solution in the beaker rises rapidly. After adding 22g of anhydrous NaF at a weight ratio of 100:22, heating and leaching under stirring for 6 hours and then proceeding to the middle storage 1 process, the stirring speed is: 230 rpm; the temperature of the water bath is set at 120°C;
[0192] 2.2 Storage 1: the same as in Experimental Example 1;
[0193] 2.3 Filtration and washing: same as in Experimental Example 1;
[0194] 2.4 Crystallization and overflow: the same as in Experimental Example 1;...
PUM
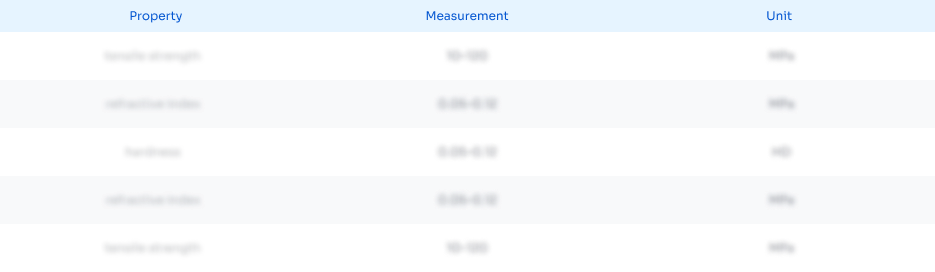
Abstract
Description
Claims
Application Information

- R&D Engineer
- R&D Manager
- IP Professional
- Industry Leading Data Capabilities
- Powerful AI technology
- Patent DNA Extraction
Browse by: Latest US Patents, China's latest patents, Technical Efficacy Thesaurus, Application Domain, Technology Topic, Popular Technical Reports.
© 2024 PatSnap. All rights reserved.Legal|Privacy policy|Modern Slavery Act Transparency Statement|Sitemap|About US| Contact US: help@patsnap.com