Loaded type polyolefin catalyst, preparation method and application
A polyolefin catalyst and supported technology, which is applied in the field of preparation and application of supported polyolefin catalysts and catalysts, can solve the problems of unfavorable industrial production and high content of polymer fine powder in the product, and achieve good shape, low subdivision content, The effect of high bulk density
- Summary
- Abstract
- Description
- Claims
- Application Information
AI Technical Summary
Problems solved by technology
Method used
Image
Examples
Embodiment 1
[0025] Add 1g of magnesium dichloride, 20ml of n-decane, 3ml of ethanol, and 6.5ml of isooctyl alcohol into the reactor that has been fully replaced by nitrogen, stir and heat up to 120°C, and react at constant temperature for 2 hours. The solids are completely dissolved to form a uniform solution. Cool down to 50°C, add 0.05ml of ethylene glycol monomethyl ether, and react for 2h. Cool down to -20°C and add 10ml of silicon tetrachloride dropwise. After the dropwise addition, raise the temperature to 60°C to react for 2 hours to obtain a milky white turbid solution. Lower the system to -10°C, add 15ml of titanium tetrachloride dropwise, react for 1 hour, then raise the temperature to 70°C for 2 hours. Stop stirring, let stand, separate layers, filter, wash with hexane four times (30 milliliters each), and dry to obtain a spherical powdery solid catalyst with good fluidity and uniform particle size distribution.
Embodiment 2
[0027] Add 1g of magnesium dichloride, 20ml of n-decane, 1.5ml of ethanol, and 7ml of isooctyl alcohol into the reactor fully replaced by nitrogen, stir and heat up to 120°C, and react at constant temperature for 2h, and the solids are completely dissolved to form a uniform solution. Cool down to 50°C, add 0.2ml of ethylene glycol monomethyl ether, and react for 2h. Cool down to -20°C, add 20ml of silicon tetrachloride dropwise, and then raise the temperature to 60°C to react for 2 hours to obtain a milky white turbid solution. Lower the system to -10°C, add 20ml of titanium tetrachloride dropwise, react for 1h, then raise the temperature to 90°C for 2h. Stop stirring, let stand, separate layers, filter, wash with hexane four times (30 milliliters each), and dry to obtain a spherical powdery solid catalyst with good fluidity and uniform particle size distribution.
Embodiment 3
[0029] Add 1g of magnesium dichloride, 20ml of n-decane, 2.5ml of ethanol, and 8.5ml of isooctyl alcohol into the reactor that has been fully replaced by nitrogen, stir and heat up to 90°C, and react at constant temperature for 2 hours. The solids are completely dissolved to form a uniform solution. Cool down to 50°C, add 0.02ml of ethylene glycol monomethyl ether, and react for 2h. Cool down to -15°C and add 15ml of silicon tetrachloride dropwise. After the dropwise addition, raise the temperature to 70°C for 2 hours to obtain a milky white turbid solution. Lower the system to -20°C, add 25ml of titanium tetrachloride dropwise, react for 1h, then raise the temperature to 90°C for 2h. Stop stirring, let stand, separate layers, filter, wash with hexane four times (30 milliliters each), and dry to obtain a spherical powdery solid catalyst with good fluidity and uniform particle size distribution.
PUM
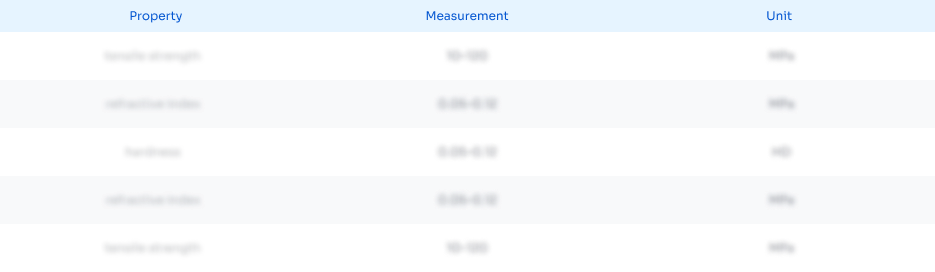
Abstract
Description
Claims
Application Information

- R&D
- Intellectual Property
- Life Sciences
- Materials
- Tech Scout
- Unparalleled Data Quality
- Higher Quality Content
- 60% Fewer Hallucinations
Browse by: Latest US Patents, China's latest patents, Technical Efficacy Thesaurus, Application Domain, Technology Topic, Popular Technical Reports.
© 2025 PatSnap. All rights reserved.Legal|Privacy policy|Modern Slavery Act Transparency Statement|Sitemap|About US| Contact US: help@patsnap.com