Direct reduction process for sponge iron production implemented by using non-catalytic conversion of CH4
A non-catalytic, sponge iron technology, applied in the field of iron or steel smelting, can solve the problems of long process flow, complex process route, insufficient conversion, etc., and achieve strong controllability of process parameters, simple process flow, and preheating temperature. low effect
- Summary
- Abstract
- Description
- Claims
- Application Information
AI Technical Summary
Problems solved by technology
Method used
Image
Examples
no. 1 example
[0038] This example utilizes CH 4 The direct reduction process for the production of sponge iron by non-catalytic conversion is:
[0039] The purified and pressure-regulated rich CH 4 The raw material gas and the furnace top gas output from the shaft furnace and obtained after cooling, dust removal, dehydration, pressurization, and decarburization enter the tube furnace together for preheating, and the preheating temperature is 400°C. The CH-enriched 4 The raw material gas is coke oven gas;
[0040] The preheated coal gas enters the non-catalytic pure oxygen reformer, where it undergoes a combustion reaction with oxygen and rapidly raises the temperature to 1300°C. CH 4 Non-catalytic conversion to CO+H 2 ;
[0041] The high-temperature gas discharged from the non-catalytic pure oxygen reformer is mixed with the top gas which has been cooled, dedusted, pressurized and decarburized at the front end, and then enters the shaft furnace to reduce iron ore to produce sponge iron;...
no. 2 example
[0044] This example utilizes CH 4 The direct reduction process for the production of sponge iron by non-catalytic conversion is:
[0045] The purified and pressure-regulated rich CH 4 The raw material gas and the furnace top gas output from the shaft furnace and obtained after cooling, dust removal, dehydration, pressurization, and decarburization enter the tube furnace together for preheating, and the preheating temperature is 380°C. The CH-rich gas in this embodiment 4 The feed gas is natural gas;
[0046] The preheated gas enters the non-catalytic pure oxygen reformer, where it undergoes a combustion reaction with oxygen and rapidly raises the temperature to 1200°C to convert CH 4 Non-catalytic conversion to CO+H 2 ;
[0047] The high-temperature gas discharged from the non-catalytic pure oxygen reformer is mixed with the top gas which has been cooled, dedusted, pressurized and decarburized at the front end, and then enters the shaft furnace to reduce iron ore to produc...
no. 3 example
[0050] This example utilizes CH 4 The direct reduction process for the production of sponge iron by non-catalytic conversion is:
[0051] The purified and pressure-regulated rich CH 4 The raw material gas and the furnace top gas output from the shaft furnace and obtained after cooling, dust removal, dehydration, pressurization, and decarburization enter the tube furnace together for preheating, and the preheating temperature is 350°C. The CH-enriched 4 The raw material gas is coke oven gas;
[0052] The preheated coal gas enters the non-catalytic pure oxygen reformer, where it undergoes a combustion reaction with oxygen and rapidly raises the temperature to 1400°C. CH 4 Non-catalytic conversion to CO+H 2 ;
[0053] The high-temperature gas discharged from the non-catalytic pure oxygen reformer is mixed with the top gas which has been cooled, dedusted, pressurized and decarburized at the front end, and then enters the shaft furnace to reduce iron ore to produce sponge iron;...
PUM
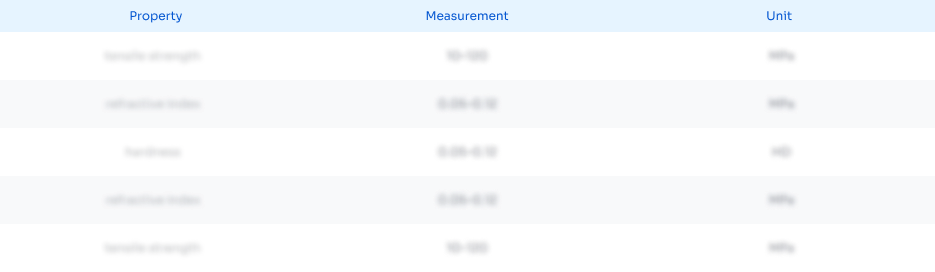
Abstract
Description
Claims
Application Information

- R&D
- Intellectual Property
- Life Sciences
- Materials
- Tech Scout
- Unparalleled Data Quality
- Higher Quality Content
- 60% Fewer Hallucinations
Browse by: Latest US Patents, China's latest patents, Technical Efficacy Thesaurus, Application Domain, Technology Topic, Popular Technical Reports.
© 2025 PatSnap. All rights reserved.Legal|Privacy policy|Modern Slavery Act Transparency Statement|Sitemap|About US| Contact US: help@patsnap.com