Polyethylene terephthalate nucleating agent and preparation method thereof
A technology of polyethylene terephthalate and nucleating agent is applied in the field of nucleating agent and preparation of polyethylene terephthalate, and can solve the problem of difficult industrialization, complicated operation process, and difficulty in finding compatibilization. It can improve the melting and crystallization temperature, the preparation process is simple, and the crystallization rate can be accelerated.
- Summary
- Abstract
- Description
- Claims
- Application Information
AI Technical Summary
Problems solved by technology
Method used
Image
Examples
Embodiment 1
[0025] (1) Synthesis of polystyrene-b-poly(styrene-alt-maleic anhydride) diblock copolymer
[0026] Mix 106 g of styrene, 2.45 g of maleic anhydride, 0.0684 g of cumyl bisthiobenzoate (CDB), and 0.0208 g of azobisethylbutyronitrile (AIBN) into the reaction flask, and set the temperature at 60°C in a nitrogen atmosphere. React for 12 hours. The product was filtered through a large amount of methanol precipitation, and purified twice by THF dissolution-methanol precipitation. Dry in a vacuum oven at 60°C for 24 hours to obtain a polystyrene-b-poly(styrene-alt-maleic anhydride) diblock copolymer.
[0027] (2) Preparation of polystyrene-b-poly(styrene-alt-maleic anhydride) diblock ionomer
[0028] Dissolve the dried polystyrene-b-poly(styrene-alt-maleic anhydride) diblock copolymer in 1,4-dioxane solution, add sodium hydroxide to the solution in methanol saturated Solution, when its pH value is about 7 as measured by pH test paper, stop dropping methanol solution. The solution...
Embodiment 2
[0030] (1) Synthesis of polystyrene-b-poly(styrene-alt-maleic anhydride) diblock copolymer
[0031]Mix 52 g of styrene, 0.273 g of CDB and 0.04145 g of AIBN into the reaction flask, react at 60°C for 24 h in a nitrogen atmosphere, and synthesize a macromolecular PS-RAFT reagent with a relative molecular weight of 12670. The purification of the product is the same as in Example 1 . Dry in a vacuum oven at 60° C. for 24 hours to obtain a dry PS-RAFT reagent.
[0032] Mix 7.38 g of styrene, 6.9 g of maleic anhydride, 3 g of PS-RAFT reagent, 0.019 g of AIBN and 50 ml of cyclohexanone solvent into the reaction flask, react at 60°C for 35 minutes in a nitrogen atmosphere, and extend the chain The relative molecular weight of the synthesized poly(styrene-alt-maleic anhydride) block was 7341. Example 1 of crude product purification method, drying in a vacuum oven at 60°C for 24 hours to obtain polystyrene-b-poly(styrene-alt-maleic anhydride) diblock copolymer.
[0033] (2) Preparat...
Embodiment 3
[0036] (1) Synthesis of polystyrene-b-poly(styrene-alt-maleic anhydride) diblock copolymer
[0037] Mix 10.6 g of styrene, 9.8 g of maleic anhydride, 0.0546 g of CDB and 0.0164 g of AIBN and 50 ml of solvent into the reaction flask, and react at 60°C for about 2 hours under the protection of nitrogen to obtain the macromolecular SMA-RAFT The reagent has a relative molecular weight of about 16,000. After the product is purified, it is dried in a vacuum oven at 60°C for 24 hours to obtain a dry macromolecular SMA-RAFT reagent.
[0038] Mix 50 g of styrene, 3 g of SMA-RAFT reagent and 0.0154 g of AIBN into the reaction flask, and react at 60°C for 8 hours in a nitrogen atmosphere, polystyrene-b-poly(styrene-alt-malay anhydride) diblock copolymers. The product purification method was the same as that of Example 1, and it was dried in a vacuum oven at 60° C. for 24 hours to obtain a polystyrene-b-poly(styrene-alt-maleic anhydride) diblock copolymer.
[0039] (2) Polystyrene-b-pol...
PUM
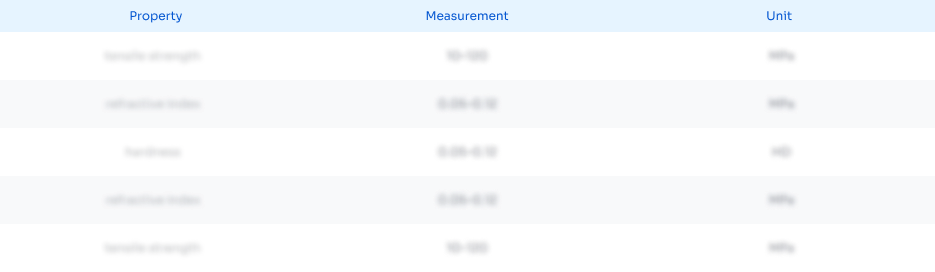
Abstract
Description
Claims
Application Information

- R&D
- Intellectual Property
- Life Sciences
- Materials
- Tech Scout
- Unparalleled Data Quality
- Higher Quality Content
- 60% Fewer Hallucinations
Browse by: Latest US Patents, China's latest patents, Technical Efficacy Thesaurus, Application Domain, Technology Topic, Popular Technical Reports.
© 2025 PatSnap. All rights reserved.Legal|Privacy policy|Modern Slavery Act Transparency Statement|Sitemap|About US| Contact US: help@patsnap.com