Method for producing aluminum oxide by using alkaline method
An alumina and alkali process technology, applied in the direction of alumina/aluminum hydroxide, etc., can solve the problems of large material flow, high energy consumption, poor technical economy, etc., and achieve small material flow, low energy consumption, and solid residue volume less effect
- Summary
- Abstract
- Description
- Claims
- Application Information
AI Technical Summary
Problems solved by technology
Method used
Examples
Embodiment 1
[0039] The raw material is bauxite from a certain place, the main chemical composition is Al 2 o 3 56%, SiO 2 22%, the ground fineness is -80 mesh limestone powder and sodium carbonate and evaporated carbonation decomposition mother liquor according to CaO and SiO 2 The molar ratio of 1.1, Na 2 O and Al 2 o 3 + Fe 2 o 3 The molar ratio is 1.4 to control the ingredients to prepare raw meal; burn the raw meal slurry at a temperature of 1200°C to obtain qualified clinker; use the adjusting liquid to leach the clinker under the condition of 80-90°C, and the alumina in the clinker The leaching rate was 86%, and the leaching rate of sodium oxide in clinker was 81%.
[0040] The concentration of caustic alkali for the solid phase residue after the clinker is dissolved is Na 2 o K 30g / L lye was leached for 300 minutes at a temperature of 95°C, the leaching liquid-solid ratio was 3, and Al in the solid phase residue 2 o3 The leaching rate is 19%, the Na in the solid phase...
Embodiment 2
[0042] The raw material is bauxite from a certain place, the main chemical composition is Al 2 o 3 55.21%, SiO 2 15.28%, the ground fineness is -80 mesh lime powder and sodium carbonate and evaporated carbonation decomposition mother liquor according to CaO and SiO 2 The molar ratio of 1.2, Na 2 O and Al 2 o 3 + Fe 2 o 3 The molar ratio is 1.6 to control the ingredients to prepare raw meal; burn the raw meal slurry at a temperature of 1220°C to obtain qualified clinker; use the adjusting liquid to leach the clinker under the condition of 75-95°C, and the alumina in the clinker The leaching rate can reach 91%, and the leaching rate of sodium oxide in clinker is 83%.
[0043] The concentration of caustic alkali for the solid phase residue after the clinker is dissolved is Na 2 o K 100g / L lye was leached for 240 minutes at a temperature of 95°C, the leaching liquid-solid ratio was 5, and Al in the solid phase residue 2 o 3 The leaching rate is 21%, the Na in the so...
Embodiment 3
[0045] The raw material is white nepheline syenite (the main chemical composition is Al 2 o 3 23.21%, SiO 2 55.90%), the ground fineness is -80 mesh limestone powder and sodium carbonate and evaporated carbonation decomposition mother liquor according to CaO and SiO 2 The molar ratio is 1.0, Na 2 O and Al 2 o 3 + Fe 2 o 3 The molar ratio of the raw material is 2.0 to control the ingredients to prepare raw meal; the raw material slurry is fired at a temperature of 1230°C to obtain qualified clinker; the clinker is leached with an adjustment solution at a temperature of 80-90°C, and alumina in the clinker The leaching rate is 83%, and the leaching rate of sodium oxide in clinker is 79%. .
[0046] The concentration of caustic alkali for the solid phase residue after the clinker is dissolved is Na 2 o K 120g / L, α k The sodium aluminate solution of 10.5 was leached for 120 minutes at a temperature of 90°C, the leaching liquid-solid ratio was 7, and the Al in the so...
PUM
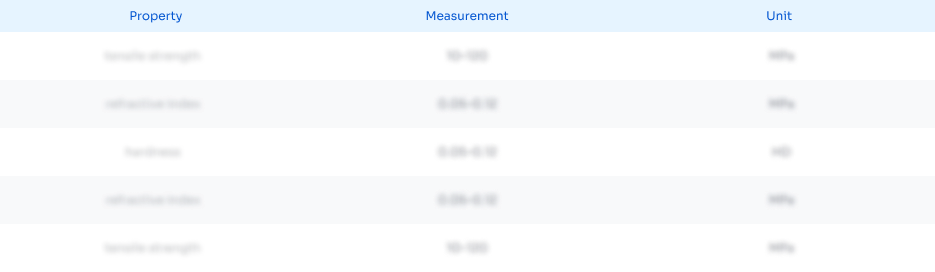
Abstract
Description
Claims
Application Information

- R&D
- Intellectual Property
- Life Sciences
- Materials
- Tech Scout
- Unparalleled Data Quality
- Higher Quality Content
- 60% Fewer Hallucinations
Browse by: Latest US Patents, China's latest patents, Technical Efficacy Thesaurus, Application Domain, Technology Topic, Popular Technical Reports.
© 2025 PatSnap. All rights reserved.Legal|Privacy policy|Modern Slavery Act Transparency Statement|Sitemap|About US| Contact US: help@patsnap.com