Anti-crack mortar as well as external wall decoration component with anti-crack mortar and preparation process of external wall decoration component with anti-crack mortar
An anti-cracking mortar, an industrial technology, applied in the direction of building structure, layered products, construction, etc., can solve the problem of insufficient anti-cracking performance of anti-cracking mortar, and achieve the effect that it is not easy to break and fall off
- Summary
- Abstract
- Description
- Claims
- Application Information
AI Technical Summary
Problems solved by technology
Method used
Image
Examples
Embodiment 1
[0023] S101: cutting the EPS material every 500mm.
[0024] To prepare anti-cracking mortar, mix 400 parts of 42.5R ordinary Portland cement, 700 parts of river sand, 8 parts of industrial gelatin, 3 parts of wood fiber, 0.5 parts of German BASF superplasticizer (model F10), 1.5 parts of methyl hydroxypropyl cellulose, 10 parts of redispersible latex powder. The mass ratio of Deutsche Mark 5010, 8031H and 5044 in the redispersible latex powder is 3:1:6.
[0025] S102: Add water with a mass ratio of 0.4 to cement, and stir evenly.
[0026] S103: Making a grid cloth, arranging alkali-resistant glass fibers vertically and horizontally on the EPS material to make a grid cloth with a grid spacing of 10 mm.
[0027] S104: forming by machine, pouring cement mortar on the grid cloth, the pouring thickness is 5mm.
[0028] S105: Natural conservation, after 42 days of natural conservation, inspection and storage.
Embodiment 2
[0030] S201: Cut the EPS material every 700mm.
[0031] Prepare anti-cracking mortar, mix 350 parts of 42.5R ordinary Portland cement, 800 parts of river sand, 6.5 parts of industrial gelatin, 4 parts of wood fiber, 0.35 parts of German BASF superplasticizer (model is F10), 2 parts of methyl hydroxypropyl cellulose, 8 parts of redispersible latex powder. The mass ratio of Deutsche Mark 5010, 8031H and 5044 in the redispersible latex powder is 3:1:6.
[0032] S202: Add water with a mass ratio of 0.3 to cement, and stir evenly.
[0033] S203: making a mesh cloth, arranging alkali-resistant glass fibers vertically and horizontally on the EPS material to make a mesh cloth with a mesh spacing of 12 mm.
[0034] S204: forming by machine, pouring cement mortar on the grid cloth, the pouring thickness is 2mm.
[0035] S205: Natural conservation, after 45 days of natural conservation, inspection and storage.
Embodiment 3
[0037] S301: Cut the EPS material every 500mm.
[0038] Prepare anti-cracking mortar, mix 450 parts of 42.5R ordinary Portland cement, 600 parts of river sand, 9.5 parts of industrial gelatin, 2 parts of wood fiber, 0.65 parts of German BASF superplasticizer (model is F10), 1 part of methyl hydroxypropyl cellulose, 12 parts of redispersible latex powder. The mass ratio of Deutsche Mark 5010, 8031H and 5044 in the redispersible latex powder is 3:1:6.
[0039] S302: Add water with a mass ratio of 0.5 to cement, and stir evenly.
[0040] S303: making a mesh cloth, arranging alkali-resistant glass fibers vertically and horizontally on the EPS material to make a mesh cloth with a mesh spacing of 10 mm.
[0041] S304: forming by machine, pouring cement mortar on the grid cloth, the pouring thickness is 9mm.
[0042] S305: Natural conservation, after 40 days of natural conservation, inspection and storage.
PUM
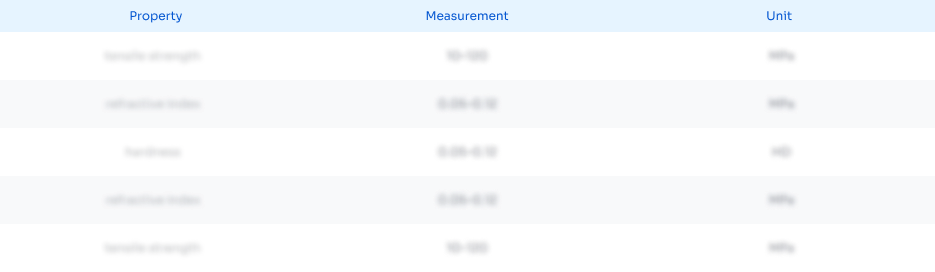
Abstract
Description
Claims
Application Information

- R&D
- Intellectual Property
- Life Sciences
- Materials
- Tech Scout
- Unparalleled Data Quality
- Higher Quality Content
- 60% Fewer Hallucinations
Browse by: Latest US Patents, China's latest patents, Technical Efficacy Thesaurus, Application Domain, Technology Topic, Popular Technical Reports.
© 2025 PatSnap. All rights reserved.Legal|Privacy policy|Modern Slavery Act Transparency Statement|Sitemap|About US| Contact US: help@patsnap.com