Plastic boat production method
A technology of plastic and hull materials, applied in the direction of ship hull, ship construction, non-magnetic metal hull, etc., can solve problems such as difficulties in disaster relief work, and achieve the effect of light weight and low production cost
- Summary
- Abstract
- Description
- Claims
- Application Information
AI Technical Summary
Problems solved by technology
Method used
Examples
Embodiment 1
[0027] Embodiment 1 (molding method produces plastic ship)
[0028] (1), according to the size and shape of the hull, make the corresponding hull hot-pressing mold; make the corresponding hot-pressing mold according to the size and shape of the seat on the boat; make the corresponding mold (boat head) according to the size and shape of the boat Make injection molds, blow molds for paddle rods); make corresponding foaming molds according to the size and shape of polystyrene foam lining plastic seats; make according to the shape and size of Velcro assemblies Injection mold.
[0029] (2) Heat the plastic sheet (such as polypropylene sheet) to 120-220°C with infrared rays, then immediately send the heated plastic sheet (such as polypropylene sheet) into the mold and press it into a certain shape with a press.
[0030] (3) Several molded plastic parts of different shapes are welded together with an ultrasonic welding machine, so that the shell of the plastic boat is successfully p...
Embodiment 2
[0034] Embodiment 2 (cutting, welding forming method produces plastic ship)
[0035] (1) According to the shape and size of the plastic boat, cut the plastic sheet (such as PC sheet) into the plates required to manufacture the plastic boat, and then weld these plastic plates with an ultrasonic welding machine.
[0036] (2) Heat the plastic sheet (such as polypropylene sheet) to 120-220°C with infrared heating equipment, and then send the heated plastic sheet (such as polypropylene plastic sheet) into the press to press it into the upper and lower bags of the plastic seat Covering board, and then assemble the foamed polystyrene foam seat filling board and the pressed polypropylene upper and lower cladding boards to form a complete plastic seat (the polystyrene foam board is sandwiched between the upper and lower covering boards of the polypropylene seat Between the panels, the upper and lower cladding panels of the polypropylene seat are connected by bayonet connections).
[0...
Embodiment 3
[0039] Embodiment 3 (cutting, welding molding with folding-resistant polypropylene sheet material, produces folding plastic boat)
[0040] (1) According to the shape and size of the plastic boat, the folding-resistant polypropylene plastic sheet is cut into a certain shape, and then the folding seam of the folding-resistant polypropylene sheet is processed. The processing method is to use high-frequency induction on the folding-resistant polypropylene sheet Heating machine for processing, high-frequency induction heating machine uses temperature and pressure to press the folding-resistant polypropylene sheet into the required crease (the crease can be made into a semi-circular arc), and then immediately fold the crease 2 to 3 times by heat. Second, the folding range is 90 to 180 degrees.
[0041] (2) Assemble the cut foldable polypropylene plastic sheets into a plastic boat, weld the seams with an ultrasonic welding machine, and then fold the plastic boat.
[0042] (3) Heat t...
PUM
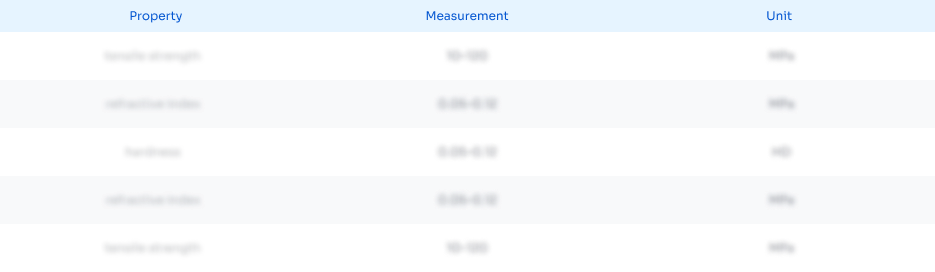
Abstract
Description
Claims
Application Information

- Generate Ideas
- Intellectual Property
- Life Sciences
- Materials
- Tech Scout
- Unparalleled Data Quality
- Higher Quality Content
- 60% Fewer Hallucinations
Browse by: Latest US Patents, China's latest patents, Technical Efficacy Thesaurus, Application Domain, Technology Topic, Popular Technical Reports.
© 2025 PatSnap. All rights reserved.Legal|Privacy policy|Modern Slavery Act Transparency Statement|Sitemap|About US| Contact US: help@patsnap.com