Preparation method for silicon nitride heating body
A technology of a silicon nitride heating element and a manufacturing method, which is applied in the direction of heating element materials, can solve the problems of reducing safety and reliability, degrading the insulation performance of materials, and large grain boundary stress, so as to improve reliability and safety, Effect of eliminating material stress and promoting crystallization
- Summary
- Abstract
- Description
- Claims
- Application Information
AI Technical Summary
Problems solved by technology
Method used
Image
Examples
Embodiment 1)
[0022] The silicon nitride heating element in this embodiment is composed of silicon nitride heating element and a high-temperature metal heating wire arranged in the silicon nitride heating element. The metal heating wire is tungsten wire, molybdenum wire or tungsten-molybdenum alloy wire.
[0023] The manufacturing method of the above-mentioned silicon nitride heating element comprises:
[0024] Step 1. Put the silicon nitride powder and the high-temperature liquid phase sintering aid into anhydrous ethanol at a weight ratio of 0.96:0.04 to 0.80:0.20 and mix (specifically, a ball mill mixer can be used for mixing), and mix for 10-72 hours Afterwards, the formulation is made through spray granulation;
[0025] Step 2, embedding the metal heating wire in the formula and dry-pressing for molding, then further pressing for molding by cold isostatic pressing of 180-220MPa, and holding the pressure for 3-10 minutes to make a green body;
[0026] Step 3, drying after evenly coati...
Embodiment 2)
[0032] On the basis of embodiment 1, the manufacturing method of the silicon nitride heating element of the present embodiment comprises:
[0033] 92wt% silicon nitride powder, 3wt% Al 2 o 3 , 3wt% of Y 2 o 3 , 1wt% MgO, 1wt% AlN, add 99.9% absolute ethanol and mix evenly for 72 hours, then put it into an explosion-proof spray granulation tower and spray granulate to make the formula.
[0034]Pour the formula into the mold, and then embed the metal heating wire in the powder and dry press to form it. The size is 120*20*10. Then the dry-pressed blank is packaged and put into cold isostatic pressing equipment for isostatic pressing. The pressure of isostatic pressing is 200 MPa, and the holding time is 3-10 minutes. Mix high-purity absolute ethanol and boron nitride fine powder to form a thick slurry, apply a layer of uniform boron nitride isolation layer on the surface of the green body by scraping method, and dry it. A boron nitride isolation layer is also coated on the c...
PUM
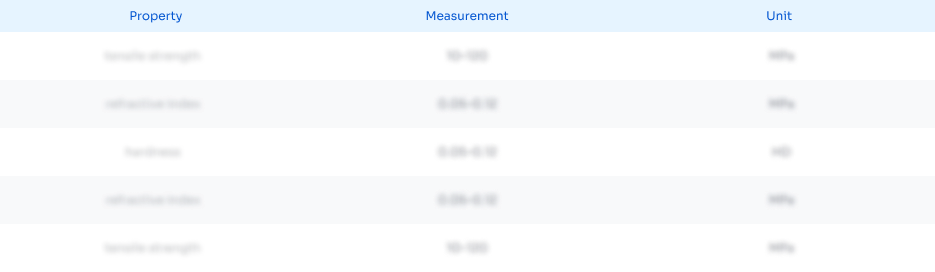
Abstract
Description
Claims
Application Information

- Generate Ideas
- Intellectual Property
- Life Sciences
- Materials
- Tech Scout
- Unparalleled Data Quality
- Higher Quality Content
- 60% Fewer Hallucinations
Browse by: Latest US Patents, China's latest patents, Technical Efficacy Thesaurus, Application Domain, Technology Topic, Popular Technical Reports.
© 2025 PatSnap. All rights reserved.Legal|Privacy policy|Modern Slavery Act Transparency Statement|Sitemap|About US| Contact US: help@patsnap.com