Rotary contact-type testing machine and method for testing high temperature and wear resistance of refractory materials
A refractory material, high-temperature wear-resistant technology, applied in the field of rotary contact testing machine, can solve the problems of irregular area, large error, and the inability to use easily oxidized refractory materials, etc., achieve stable grinding pressure and speed, reduce test error, and test The effect of high temperature
- Summary
- Abstract
- Description
- Claims
- Application Information
AI Technical Summary
Problems solved by technology
Method used
Image
Examples
Embodiment 1
[0017] Such as figure 1 As shown, a rotary contact testing machine for testing the high-temperature wear resistance of refractory materials, the main body is an electric furnace that can automatically control the temperature rise, constant temperature and temperature drop according to the program within the range of room temperature to 1650 °C. There is a groove 3 for placing the sample to be tested at the furnace door 2, and a collection tank 5 is provided at the bottom of the furnace body 6 to prevent the powder from sticking and accumulating in the furnace body; the furnace body 6 is connected to the nitrogen cylinder 13 through a pipeline , a cylindrical rotating body 1 is arranged in the furnace body 6, and the rotating body 1 is driven by a rotating power device 8. In order to protect the rotating power device 8, a water cooling device 7 is provided between the furnace body 6 and the rotating power device 8, and the rotating power device Device 8 comprises rotary motor 9...
Embodiment 2
[0035] A rotary contact testing machine for testing the high-temperature wear resistance of refractory materials, the structure and software flow are the same as those in Embodiment 1.
[0036] Using this testing machine to test the high temperature wear resistance of refractory materials, the steps are as follows:
[0037] 1. The size of the sample is 114mm×114mm×65mm. Shaped refractory samples are cut into sample specifications, and unshaped refractory materials are formed by pouring or ramming. The test surface of the sample should be flat and free of visible cracks;
[0038] 2. Basic test parameter settings: including experimental temperature 1600°C, heating rate 15°C / min before 1000°C, 8°C / min after 1000°C, constant temperature time 90 minutes; grinding pressure 850N; grinding time 25 minutes;
[0039] 3. Placement of the sample, place the pre-prepared sample to be tested in the groove reserved on the furnace door and fix it, close the furnace door and adjust the rot...
Embodiment 3
[0045] A rotary contact testing machine for testing the high-temperature wear resistance of refractory materials, the structure is the same as in Example 1, and the test control software flow is as follows image 3 shown.
[0046] The process is as follows:
[0047] a: input parameters, start;
[0048] b: Control the temperature rise of the furnace, and judge whether it reaches the set temperature; "Yes", start the hydraulic push rod to control the rotating body to move forward, and if the result is "No", continue to control the temperature rise of the furnace;
[0049] c: Judging whether the set pressure is reached, if "Yes", start the rotating motor to start the grinding test, and start the grinding timing; "No", the hydraulic push rod will continue to move forward;
[0050] d: When the pressure decay is greater than 50%, the test ends;
[0051] e: Judging whether the set grinding displacement has been reached, if "Yes", the test ends and the grinding timing is stopped, i...
PUM
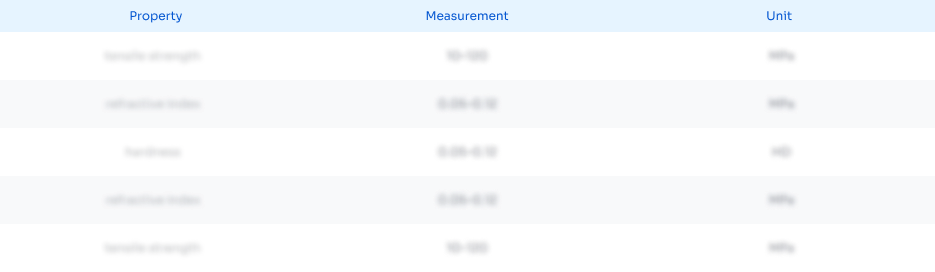
Abstract
Description
Claims
Application Information

- R&D
- Intellectual Property
- Life Sciences
- Materials
- Tech Scout
- Unparalleled Data Quality
- Higher Quality Content
- 60% Fewer Hallucinations
Browse by: Latest US Patents, China's latest patents, Technical Efficacy Thesaurus, Application Domain, Technology Topic, Popular Technical Reports.
© 2025 PatSnap. All rights reserved.Legal|Privacy policy|Modern Slavery Act Transparency Statement|Sitemap|About US| Contact US: help@patsnap.com