Organic fiber friction material composition for brake pad
A technology of organic fibers and friction materials, which is applied in the field of automobile brake pads, can solve the problems of heat dissipation, poor wear resistance, and large changes in friction performance of brake pads, and achieve good recovery performance, low heat decay, and sensitive braking.
- Summary
- Abstract
- Description
- Claims
- Application Information
AI Technical Summary
Problems solved by technology
Method used
Examples
Embodiment 1
[0022] Example 1: By weight, 3 parts of chromite powder, 7 parts of barite powder (600 mesh), 4 parts of calcined petroleum coke, 3 parts of flake graphite, 13 parts of boric acid modified phenolic resin, and 5 parts of sepiolite fiber 4 parts of ceramic fiber, 3 parts of antimony sulfide, 7 parts of bronze powder, 3 parts of glass wool, 2 parts of zircon, 7 parts of phosphorus potassium titanate, 8 parts of vermiculite powder (20-40 mesh), 1.5 parts of carbon fiber 5 parts of aramid pulp, 2.5 parts of wood pulp fiber, 5 parts of viscose fiber, 7 parts of silicon carbide, and 10 parts of cellulose fiber are put into the high-speed disperser, stirred into powder, taken out, and put into the forming mold It is pressed and formed, then compounded with a steel back and placed in a flat vulcanizer at a high temperature of 270°C and a pressure of 18MPa for 15 minutes, then the brake pads are taken out, and the burrs are removed to become a finished product.
Embodiment 2
[0023] Example 2: By weight ratio, 7 parts of chromite powder, 6 parts of barite powder (600 mesh), 5 parts of calcined petroleum coke, 4 parts of flake graphite, 10 parts of boric acid modified phenolic resin, and 6 parts of sepiolite fiber 5 parts, ceramic fiber 5 parts, antimony sulfide 1.5 parts, bronze powder 4.5 parts, glass wool 4 parts, zircon 2.5 parts, phosphorous potassium titanate 8 parts, vermiculite powder (20-40 mesh) 9.5 parts, carbon fiber 2 parts , 6 parts of aramid pulp, 1 part of wood pulp fiber, 3 parts of viscose fiber, 8 parts of silicon carbide, and 7 parts of cellulose fiber are put into the high-speed disperser, stirred into powder, taken out, put into the forming mold and pressed Forming, then compounding with the steel back, put it into a flat vulcanizing machine at a high temperature of 270°C and a pressure of 18MPa, keep it for 15 minutes, then take out the brake pads, remove the burrs and become a finished product.
Embodiment 3
[0024] Example 3: 5 parts of chromite powder, 4 parts of barite powder (600 mesh), 6.5 parts of calcined petroleum coke, 4.5 parts of flake graphite, 12 parts of boric acid modified phenolic resin, and 5 parts of sepiolite fiber were prepared by weight. 7 parts of ceramic fiber, 2 parts of antimony sulfide, 6 parts of bronze powder, 4 parts of glass wool, 1.5 parts of zircon, 7.3 parts of phosphorus potassium titanate, 9 parts of vermiculite powder (20-40 mesh), 1.7 parts of carbon fiber , 5 parts of aramid pulp, 2 parts of wood pulp fiber, 3 parts of viscose fiber, 6 parts of silicon carbide, and 8 parts of cellulose fiber are put into the high-speed disperser, stirred into powder, taken out, put into the forming mold and pressed Forming, then compounding with the steel back, put it into a flat vulcanizing machine at a high temperature of 270°C and a pressure of 18MPa, keep it for 15 minutes, then take out the brake pads, remove the burrs and become a finished product.
PUM
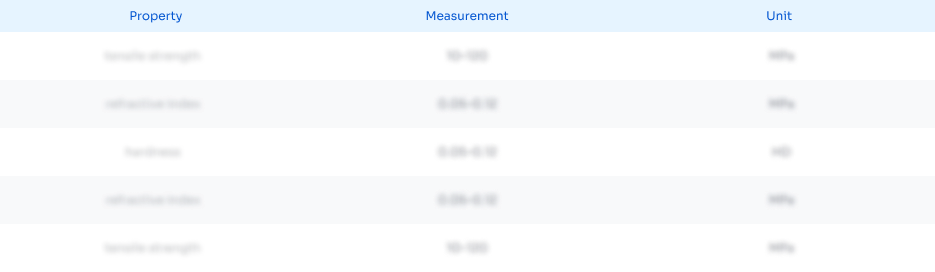
Abstract
Description
Claims
Application Information

- R&D
- Intellectual Property
- Life Sciences
- Materials
- Tech Scout
- Unparalleled Data Quality
- Higher Quality Content
- 60% Fewer Hallucinations
Browse by: Latest US Patents, China's latest patents, Technical Efficacy Thesaurus, Application Domain, Technology Topic, Popular Technical Reports.
© 2025 PatSnap. All rights reserved.Legal|Privacy policy|Modern Slavery Act Transparency Statement|Sitemap|About US| Contact US: help@patsnap.com