Compound perovskite oxide and preparation method thereof
A composite perovskite and oxide technology, applied in the field of electronic ceramics, can solve the problems of large lattice stress and failure to synthesize, and achieve the effect of suppressing lattice strain
- Summary
- Abstract
- Description
- Claims
- Application Information
AI Technical Summary
Problems solved by technology
Method used
Image
Examples
Embodiment 1
[0019] Composite perovskite oxide: CaCu 3 Ni 4 o 12 .
[0020] The preparation steps are:
[0021] (1) Using calcium oxide, copper oxide and nickel monoxide as raw materials, according to the general formula CaCu 3 Ni 4 o 12 The stoichiometric ratio for batching.
[0022] (2) Put the raw materials prepared in step (1) into a ball mill jar, add zirconia balls and absolute ethanol as the ball milling medium, the mass of the added zirconia balls is twice the mass of the raw materials, and the added absolute ethanol The mass is 0.5 times that of the raw material, and the wet milling method is used for ball milling and mixing for 4 hours at a speed of 450 rpm, and the mixed slurry is taken out and dried at 140°C.
[0023] (3) Put the powder dried in step (2) into a niobium crucible, and then press the powder together with the niobium crucible under a one-way pressure of 200MPa.
[0024] (4) Place the block formed in step (3) in a high-pressure sintering furnace, first apply...
Embodiment 2
[0027] Composite perovskite oxide CaCu 3 Sb 4 o 12 .
[0028] The preparation steps are:
[0029] (1) Using calcium oxide, copper oxide and antimony pentoxide as raw materials, according to the general formula CaCu 3 Sb 4 o 12 The stoichiometric ratio for batching.
[0030] (2) Put the raw materials prepared in step (1) into a ball mill jar, add zirconia balls and absolute ethanol as the ball milling medium, the mass of the added zirconia balls is 6 times the mass of the raw materials, and the added absolute ethanol The mass is 1 times that of the raw material, and the wet milling method is used for ball milling and mixing for 12 hours at a speed of 350 rpm, and the mixed slurry is taken out and dried at 100°C.
[0031] (3) Put the powder dried in step (2) into a molybdenum crucible, and then press the powder together with the molybdenum crucible under a one-way pressure of 300MPa.
[0032] (4) Place the block formed in step (3) in a high-pressure sintering furnace, fi...
Embodiment 3
[0036] Composite perovskite oxide: CaCu 3 Bi 4 o 12 .
[0037] The preparation steps are:
[0038] (1) Using calcium oxide, copper oxide and bismuth trioxide as raw materials, according to the general formula CaCu 3 Bi 4 o 12 The stoichiometric ratio of
[0039] material.
[0040] (2) Put the raw materials prepared in step (1) into the ball milling tank, add zirconia balls and absolute ethanol as the ball milling medium, the mass of the added zirconia balls is 8 times the mass of the raw materials, and the added absolute ethanol The mass is twice that of the raw material, and the wet milling method is used for ball milling and mixing for 24 hours at a speed of 200 rpm, and the mixed slurry is taken out and dried at 80°C.
[0041] (3) Put the powder dried in step (2) into a titanium crucible, and then press the powder together with the titanium crucible under a one-way pressure of 400MPa.
[0042] (4) Place the block formed in step (3) in a high-pressure sintering furnac...
PUM
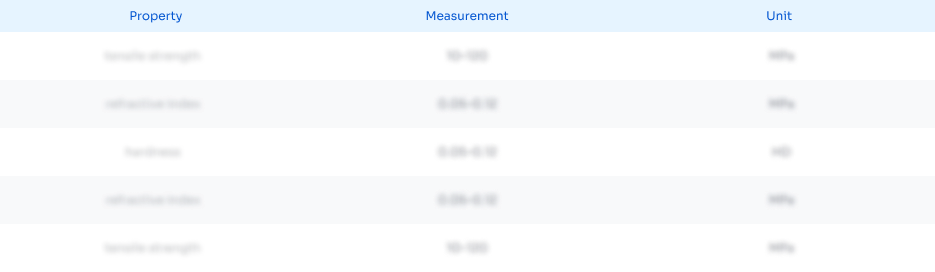
Abstract
Description
Claims
Application Information

- R&D
- Intellectual Property
- Life Sciences
- Materials
- Tech Scout
- Unparalleled Data Quality
- Higher Quality Content
- 60% Fewer Hallucinations
Browse by: Latest US Patents, China's latest patents, Technical Efficacy Thesaurus, Application Domain, Technology Topic, Popular Technical Reports.
© 2025 PatSnap. All rights reserved.Legal|Privacy policy|Modern Slavery Act Transparency Statement|Sitemap|About US| Contact US: help@patsnap.com