V-based low temperature sintering microwave medium ceramic material and preparation method thereof
A technology of microwave dielectric ceramics and microwave dielectric materials, applied in the field of V-based low-temperature sintered microwave dielectric ceramic materials and its preparation, and new microwave dielectric ceramic materials, which can solve the problems of low performance and achieve high Q×f value and low sintering temperature , The effect of reducing manufacturing costs
- Summary
- Abstract
- Description
- Claims
- Application Information
AI Technical Summary
Problems solved by technology
Method used
Image
Examples
Embodiment 1
[0018] (1) First, the chemical raw material Li 2 CO 3 , MgO and NH 4 VO 3 Moore Billy 2 CO 3 : MgO: NH 4 VO 3 =0.5:4:3 to prepare the main powder.
[0019] (2) Mix the main powder prepared in step (1) evenly, add alcohol to the main powder according to the weight ratio of the main powder and alcohol as 1:1, and mix for 4 hours by wet grinding method. Dry at 120°C, press into blocks after drying, and then raise the pressed block-shaped raw materials from room temperature to 800°C at a heating rate of 5°C / min and keep it at this temperature for 4 hours to make sintered blocks.
[0020] (3) Crush the burnt block made in step (2), add alcohol to the powder according to the mass ratio of powder and alcohol as 1:1, put it into a nylon tank and ball mill it for 4 hours, take it out, put it in the oven Dry at 120°C, granulate and press into small discs, deglue at 550°C, cool in the furnace to obtain porcelain material, and then sinter the ceramic material at 950°C for 4 hours...
Embodiment 2
[0023] (1) First, the chemical raw material Li 2 CO 3 , MgO and NH 4 VO 3 Moore Billy 2 CO 3 : MgO: NH 4 VO 3 =0.5:4:3 to prepare the main powder.
[0024] (2) Mix the main powder prepared in step (1) evenly, add alcohol to the main powder according to the weight ratio of the main powder and alcohol at 1:1, mix for 6 hours by wet grinding method, and grind it finely Dry at 140°C, press into blocks after drying, then raise the pressed block-shaped raw materials from room temperature to 850°C at a heating rate of 5°C / min and keep at this temperature for 4 hours to make sintered blocks.
[0025] (3) Crush the sintered block made in step (2), ball mill for 4 hours, put it in an oven for drying, and then add 0.5% Bi by weight 2 o 3, made into powder, according to the volume ratio of powder and alcohol 1:1, add alcohol to the powder, put it into a nylon tank and ball mill for 6 hours, take it out, put it in an oven and dry it at 130°C, after granulation Pressed into small...
Embodiment 3
[0028] (1) First, the chemical raw material Li 2 CO 3 , MgO and NH 4 VO 3 Moore Billy 2 CO 3 : MgO: NH 4 VO 3 =0.5:4:3 to prepare the main powder.
[0029] (2) Mix the main powder prepared in step (1) evenly, add alcohol to the main powder according to the weight ratio of the main powder and alcohol at 1:1, mix for 8 hours by wet grinding method, and grind it finely Dry at 140°C, press into blocks after drying, then raise the pressed block-shaped raw materials from room temperature to 850°C at a heating rate of 5°C / min and keep at this temperature for 4 hours to make sintered blocks.
[0030] (3) Pulverize the burnt block made in step (2), ball mill for 8 hours, put it into an oven for drying, and then add 1% Bi by weight 2 o 3 , made into powder, according to the volume ratio of powder and alcohol is 1:1, add alcohol to the powder, put it into a nylon tank for ball milling for 6 hours, take it out, put it in an oven and dry it at 140°C, after granulation Pressed in...
PUM
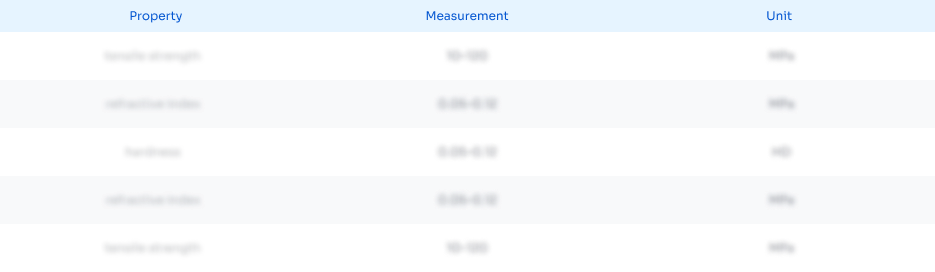
Abstract
Description
Claims
Application Information

- R&D
- Intellectual Property
- Life Sciences
- Materials
- Tech Scout
- Unparalleled Data Quality
- Higher Quality Content
- 60% Fewer Hallucinations
Browse by: Latest US Patents, China's latest patents, Technical Efficacy Thesaurus, Application Domain, Technology Topic, Popular Technical Reports.
© 2025 PatSnap. All rights reserved.Legal|Privacy policy|Modern Slavery Act Transparency Statement|Sitemap|About US| Contact US: help@patsnap.com