Process method for separating zinc, iron and cobalt and nickel ore concentrates from cobalt and nickel slag
A process method, cobalt-nickel slag technology, applied to the improvement of process efficiency, chemical instruments and methods, iron compounds, etc., can solve the problems of low economic benefit and complicated process flow, and achieve high price, obvious economic benefit and less time-consuming Effect
- Summary
- Abstract
- Description
- Claims
- Application Information
AI Technical Summary
Problems solved by technology
Method used
Image
Examples
Embodiment Construction
[0028] The present invention will be described in further detail below in conjunction with the accompanying drawings. Such as figure 1As shown, the cobalt-nickel slag is first added to the sulfuric acid solution at a solid-to-liquid ratio of 1:3-5, heated and leached under stirring to fully dissolve completely, and the time for the sulfuric acid solution to dissolve the cobalt-nickel slag is 30-40 minutes. Separate the leaching solution from liquid to solid to obtain leaching slag and zinc solution. After washing the leaching slag several times, return it to the cobalt-nickel slag warehouse, and the washing liquid flows back into the zinc solution. Dilute the filtrate to 2000 ml with water to obtain the concentration of zinc ions It is 120-150 g / L, that is, zinc solution 1. Add a small amount of stone powder (calcium carbonate) while measuring with precision PH test paper, adjust the pH of the zinc solution to 5.0, control the temperature at 80-85°C, add hydrogen peroxide (hy...
PUM
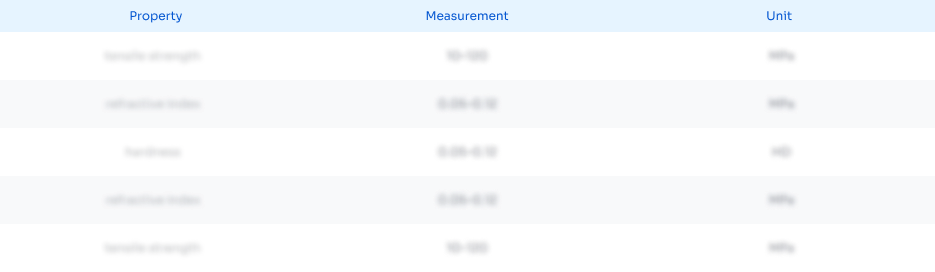
Abstract
Description
Claims
Application Information

- Generate Ideas
- Intellectual Property
- Life Sciences
- Materials
- Tech Scout
- Unparalleled Data Quality
- Higher Quality Content
- 60% Fewer Hallucinations
Browse by: Latest US Patents, China's latest patents, Technical Efficacy Thesaurus, Application Domain, Technology Topic, Popular Technical Reports.
© 2025 PatSnap. All rights reserved.Legal|Privacy policy|Modern Slavery Act Transparency Statement|Sitemap|About US| Contact US: help@patsnap.com