Method for production of high purity manganese sulfate by using pyrolusite as raw material
A production method, the technology of manganese sulfate, applied in the direction of manganese sulfate, etc., can solve the problems of high impurity content, failure to meet the technical index requirements of high-purity manganese sulfate, low main content of the product, etc., and achieve simple operation, quality controllability and Highly reproducible, quality-assured results
- Summary
- Abstract
- Description
- Claims
- Application Information
AI Technical Summary
Problems solved by technology
Method used
Image
Examples
Embodiment 1
[0018] a. Carbon fire method reduction-leaching of pyrolusite: mix pyrolusite powder and reduced coal powder in a mass ratio of 100:18, put them into a reduction furnace, roast at a temperature of 800-900°C, roast for 2 hours, and discharge the material for cooling Finally, after the reducing material and deionized water are slurried at a solid-to-liquid ratio of 1:4, sulfuric acid with a weight concentration of 98% is added. The amount of sulfuric acid added is 1.05 times the amount of acid required in theory, and the reaction time is stirred at 60°C for 2 hours. Then add iron and manganese powder, oxidize and remove iron for 1 hour, the amount of manganese powder added is 1.05 to 1.1 times the theoretical requirement, add ammonium sulfide, the amount of ammonium sulfide added is 1% of the dry weight of the reduced ore, react at room temperature for 60 minutes, filter ;
[0019] b. Remove calcium and magnesium impurities: add barium fluoride to the filtrate obtained in step ...
Embodiment 2
[0023] a. Carbon fire method reduction-leaching of pyrolusite: mix pyrolusite powder and reduced coal powder in a mass ratio of 100:18, put them into a reduction furnace, roast at a temperature of 800-900°C, roast for 2 hours, and discharge the material for cooling Finally, the reducing material and deionized water are slurried at a solid-to-liquid ratio of 1:4, and sulfuric acid with a weight concentration of 98% is added. The amount of sulfuric acid added is 1.07 times the amount of acid required in theory. , then add iron and manganese powder to oxidize and remove iron for 0.7h, the addition of manganese powder is 1.06 times of the theoretical requirement, add manganese sulfide, the addition of manganese sulfide is 1% of the dry weight of reduced ore, react at room temperature for 40min, and filter;
[0024] b. Remove calcium and magnesium impurities: add manganese fluoride to the filtrate obtained in step a, the amount added is 5 times the theoretical molar mass, react at ...
Embodiment 3
[0028] a. Carbon fire method reduction-leaching of pyrolusite: mix pyrolusite powder and reduced coal powder in a mass ratio of 100:18, put them into a reduction furnace, roast at a temperature of 800-900°C, roast for 2 hours, and discharge the material for cooling Finally, after reducing the raw material and deionized water to slurry at a solid-to-liquid ratio of 1:4, add sulfuric acid with a weight concentration of 98%, the amount of sulfuric acid added is 1.08 times the amount of acid required in theory, and the reaction time is stirred at 80°C for 2 hours. Then add iron and manganese powder to oxidize and remove iron for 1 hour. The amount of manganese powder added is 1.1 times the theoretical requirement. Add hydrogen sulfide. The amount of hydrogen sulfide added is 1% of the dry weight of the reduced ore, react at room temperature for 45 minutes, and filter;
[0029] b. Remove calcium and magnesium impurities: add barium fluoride to the filtrate obtained in step a, the a...
PUM
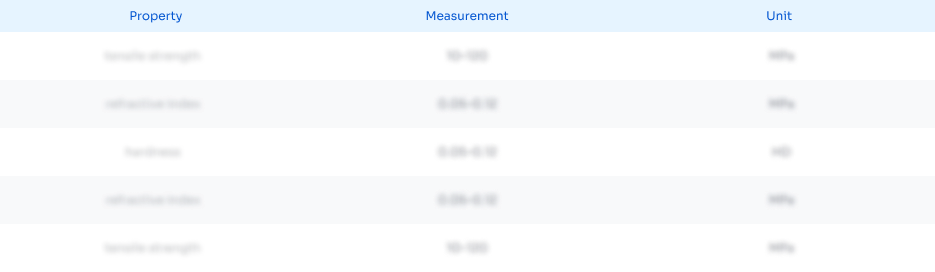
Abstract
Description
Claims
Application Information

- R&D
- Intellectual Property
- Life Sciences
- Materials
- Tech Scout
- Unparalleled Data Quality
- Higher Quality Content
- 60% Fewer Hallucinations
Browse by: Latest US Patents, China's latest patents, Technical Efficacy Thesaurus, Application Domain, Technology Topic, Popular Technical Reports.
© 2025 PatSnap. All rights reserved.Legal|Privacy policy|Modern Slavery Act Transparency Statement|Sitemap|About US| Contact US: help@patsnap.com