Alloy material applicable to inert anode of metal molten salt electrolytic cell
A technology of alloy materials and inert anodes, applied in the direction of electrodes, electrolysis process, electrolysis components, etc., can solve the problems that cannot meet the needs of industrial applications, and achieve the effects of improving electrolysis efficiency, improving corrosion resistance, and reducing pollution
- Summary
- Abstract
- Description
- Claims
- Application Information
AI Technical Summary
Problems solved by technology
Method used
Examples
Embodiment 1
[0032] An alloy material suitable for the inert anode of the metal molten salt electrolytic cell. The mass composition of the alloy is: 47% copper, 30% nickel, 15% iron, and 8% aluminum. The alloy is melted in the temperature range of 1300-1500°C in an intermediate frequency induction furnace, and then cast by water cooling. After heat treatment, the cast ingot is cut into small discs with a diameter of 25mm and a thickness of 30mm, and the density of the small discs is more than 98% of the theoretical density. The high temperature oxidation resistance test was carried out at 850°C, and the oxidation time was 200-300 hours. The results showed that the oxidation weight gain rate of the alloy was less than 0.01 mg / cm 2 h.
Embodiment 2
[0034] An alloy material suitable for the inert anode of the metal molten salt electrolytic cell, the alloy mass composition is: 75.7% copper, 15% nickel, 5% iron, 4% aluminum, 0.3% lanthanum. The alloy is melted in the temperature range of 1200-1400°C in a vacuum induction furnace, and then cast by water cooling. Electrolytic tests show that the alloy has greatly improved oxide film adhesion and robustness and anti-interference to temperature fluctuations.
Embodiment 3
[0036] An alloy material suitable for the inert anode of the metal molten salt electrolytic cell, the alloy mass composition is: 67% copper, 15% nickel, 10% iron, 6% aluminum, 2% zinc. The alloy is melted in the temperature range of 1200-1400°C in an intermediate frequency induction furnace, then cast in water cooling, and then slightly processed to form an anode product. In KF-NaF-AlF 3 -Al 2 o 3 In the electrolysis test of the system 200A, the electrolysis temperature is 750°C, and the anode current density is 0.5A / cm 2 , Electrolyzed for 300 hours, can get primary aluminum with a quality of more than 99.7%. The alloy anode forms a mixed ceramic protective layer mainly composed of copper aluminate on the surface through in-situ electrochemical polarization.
PUM
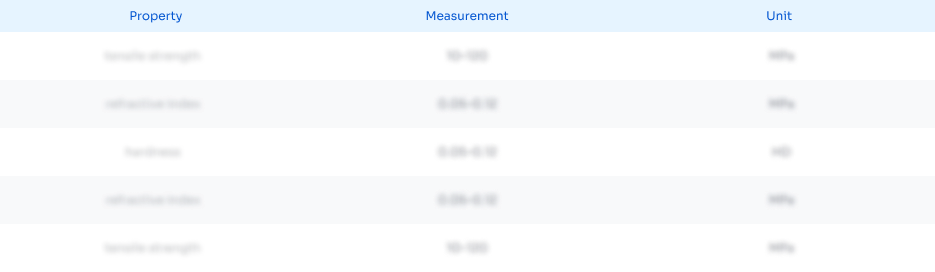
Abstract
Description
Claims
Application Information

- R&D Engineer
- R&D Manager
- IP Professional
- Industry Leading Data Capabilities
- Powerful AI technology
- Patent DNA Extraction
Browse by: Latest US Patents, China's latest patents, Technical Efficacy Thesaurus, Application Domain, Technology Topic, Popular Technical Reports.
© 2024 PatSnap. All rights reserved.Legal|Privacy policy|Modern Slavery Act Transparency Statement|Sitemap|About US| Contact US: help@patsnap.com