Piezoelectric elastic wave deicing method
A piezoelectric elastic wave and piezoelectric vibrator technology, applied in the field of deicing the outer surface of outdoor equipment, to achieve low energy consumption, avoid the influence of wing strength and vibration characteristics, and small volume and weight
- Summary
- Abstract
- Description
- Claims
- Application Information
AI Technical Summary
Problems solved by technology
Method used
Image
Examples
Embodiment 1
[0023] In the piezoelectric elastic wave deicing method of the present invention, the signal generator generates two alternating voltages with a phase difference of π / 2, which are respectively amplified by two power amplifiers and applied to piezoelectric vibrators of two different vibration modes (the first on the piezoelectric vibrator of the first mode and the piezoelectric vibrator of the second mode). The piezoelectric vibrator of the first vibration mode is selected as the first-order in-plane longitudinal stretching vibration mode E1 of the deiced surface, and the piezoelectric vibrator of the second vibration mode is selected as the second-order out-of-plane bending vibration mode B2. figure 2 (a) shows the first-order in-plane longitudinal stretching vibration mode E1 based on the deiced surface ( figure 2 (b)) and the second out-of-plane bending vibration mode B2 ( figure 2 (c)) Schematic illustration of traveling wave-like elastic wave generation. In order to e...
Embodiment 2
[0026]In the piezoelectric elastic wave deicing method of the present invention, the signal generator generates two alternating voltages with a phase difference of π / 2, which are respectively amplified by two power amplifiers and applied to piezoelectric vibrators of two different vibration modes (the first on the piezoelectric vibrator of the first mode and the piezoelectric vibrator of the second mode). The piezoelectric vibrator of the first vibration mode is selected as the B10 vibration mode of the surface to be deiced, and the piezoelectric vibrator of the second vibration mode is selected as the B06 vibration mode. In vibration mechanics, a double subscript (mn) is usually used to describe the natural mode shape of a two-dimensional structure, and the positive integers m and n represent the number of nodal lines of the mode shape parallel to the x and y axis directions, respectively. Thus, B10 means that the mode forms one wave in the y-direction, and B06 means that the...
PUM
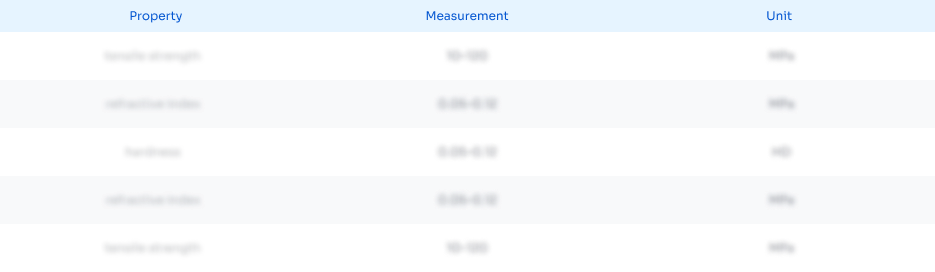
Abstract
Description
Claims
Application Information

- R&D
- Intellectual Property
- Life Sciences
- Materials
- Tech Scout
- Unparalleled Data Quality
- Higher Quality Content
- 60% Fewer Hallucinations
Browse by: Latest US Patents, China's latest patents, Technical Efficacy Thesaurus, Application Domain, Technology Topic, Popular Technical Reports.
© 2025 PatSnap. All rights reserved.Legal|Privacy policy|Modern Slavery Act Transparency Statement|Sitemap|About US| Contact US: help@patsnap.com