Chip welding method
A welding method and chip technology, which is applied in the field of chip welding and electronic parts welding, can solve the problems of low production efficiency, high price, and high price of unidirectional anisotropic conductive adhesive, so as to increase the product qualification rate, simplify the production process, and make up for equipment expensive effect
- Summary
- Abstract
- Description
- Claims
- Application Information
AI Technical Summary
Problems solved by technology
Method used
Image
Examples
Embodiment 1
[0040] Such as figure 1 and figure 2 In the chip soldering structure diagram shown, first, the solder paste 32 is placed on the surface of the pad 3 of the epoxy resin substrate 2 through the stencil printing process, and then the pad 31 of the chip 1 is aligned with the pad 3 of the substrate 2 by a manipulator. , according to the direction of arrow 4, and then heat the substrate with chip 1 through a reflow oven to solidify the solder to complete the process of chip soldering; in this process, the amount of solder is selected according to the size of the pad, Subject to sufficient connection. In actual operation, it can be adjusted by selecting the thickness of the stencil and the size of the printing window. The thickness of the steel mesh can be selected from 20um to 200um.
[0041] In the process of heating and curing the solder in the reflow oven, different solders are selected according to the material of the substrate and the corresponding heating temperature is us...
Embodiment 2
[0051] Such as figure 1 with figure 2 As shown in the chip welding structure diagram, first, the silver paste 32 is placed on the surface of the pad 3 of the polyethylene terephthalate (PET) substrate 2 by automatic dispensing equipment, and then the pad 31 of the chip 1 is placed on the surface of the pad 3 of the chip 1 by a robot. Align the pad 3 of the substrate 2 and install it, stick it in the direction of the arrow 4, and then heat the substrate with the chip 1 through the reflow oven to solidify the solder to complete the chip soldering process; in this process, the solder The amount is selected according to the size of the pad, whichever can be fully connected. In actual operation, it can be adjusted by setting parameters such as the pressure of the dispensing equipment. The thickness of the conductive agent can be selected from 30um to 300um.
[0052] In the process of heating and curing the solder in the reflow oven, different solders are selected according to t...
Embodiment 3
[0062] Such as figure 1 with figure 2 As shown in the chip welding structure diagram, first, the conductive glue or non-conductive glue 32 is placed on the surface of the pad 3 of the polyimide (PI) substrate 2 through the automatic dispensing equipment, and then the pad 31 of the chip 1 is placed on the surface of the pad 31 of the chip 1 by a robot. The pad 3 of the quasi-substrate 2 is installed, and it is pasted according to the direction of the arrow 4, and then the position of the substrate chip on which the chip 1 is installed is locally pressurized and heated to solidify the solder, and the process of chip soldering is completed; in this process, the flux of the solder The amount is selected according to the size of the pad, whichever can be fully connected. In actual operation, it can be adjusted by setting parameters such as the pressure of the dispensing equipment.
[0063] In the process of pressurizing and heating the solder to solidify, it is realized by setti...
PUM
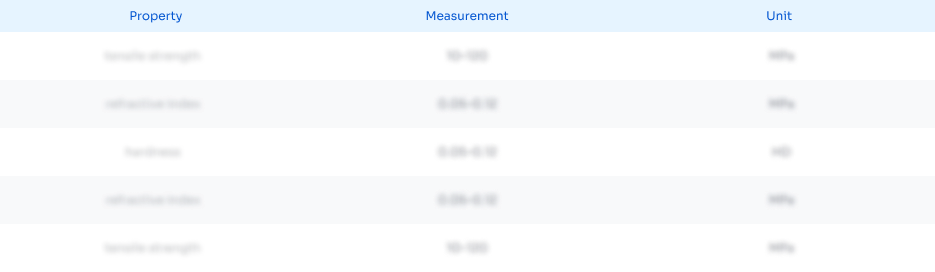
Abstract
Description
Claims
Application Information

- Generate Ideas
- Intellectual Property
- Life Sciences
- Materials
- Tech Scout
- Unparalleled Data Quality
- Higher Quality Content
- 60% Fewer Hallucinations
Browse by: Latest US Patents, China's latest patents, Technical Efficacy Thesaurus, Application Domain, Technology Topic, Popular Technical Reports.
© 2025 PatSnap. All rights reserved.Legal|Privacy policy|Modern Slavery Act Transparency Statement|Sitemap|About US| Contact US: help@patsnap.com