Drying technique for electric heating pipes
A technology of electric heating tube and drying process, which is applied in the direction of drying solid materials, the shape of heating elements, lighting and heating equipment, etc., which can solve the problems of high energy consumption, harsh production process, unfavorable energy saving, emission reduction and safe production, so as to reduce production Effects of energy consumption, shortened cooling time, and reduced possibility of secondary moisture
- Summary
- Abstract
- Description
- Claims
- Application Information
AI Technical Summary
Problems solved by technology
Method used
Examples
Embodiment 1
[0012] Example 1: A drying process for electric heating tubes, assembling resistance wires, heat-conducting fillers, metal tubes and other parts into electric heating tubes, and putting the electric heating tubes into a vacuum oven after being cleaned by cleaning liquid, and the temperature is -0.07 Heating and drying at a vacuum degree of MPa and a temperature of 150°C for 12 hours, then introducing the dried air into a vacuum oven to devacuumize, and when the vacuum oven reaches positive pressure, take out the electric heating tube immediately, apply glue to the nozzle, fill it and cure it .
Embodiment 2
[0013] Example 2: A drying process for electric heating tubes, assembling resistance wires, heat-conducting fillers, metal tubes and other parts into electric heating tubes, and putting the electric heating tubes into a vacuum oven after being cleaned by cleaning liquid, and the temperature is -0.09 Heating and drying at a vacuum degree of MPa and a temperature of 130°C for 10 hours, then introducing the dried air into a vacuum oven to devacuumize, and when the vacuum oven reaches positive pressure, immediately take out the electric heating tube, apply glue to the nozzle, fill it and cure it .
Embodiment 3
[0014] Example 3: A drying process for electric heating tubes, assembling resistance wires, heat-conducting fillers, metal tubes and other parts into electric heating tubes, and putting the electric heating tubes into a vacuum oven after being cleaned by cleaning solution, and the temperature is -0.08 Heating and drying at a vacuum degree of MPa and a temperature of 110°C for 11 hours, then introducing the dried air into a vacuum oven to devacuumize, and when the vacuum oven reaches positive pressure, take out the electric heating tube immediately, apply glue to the nozzle, fill and cure it .
PUM
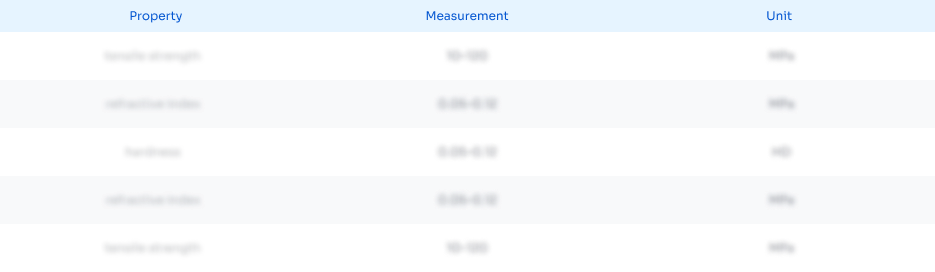
Abstract
Description
Claims
Application Information

- R&D
- Intellectual Property
- Life Sciences
- Materials
- Tech Scout
- Unparalleled Data Quality
- Higher Quality Content
- 60% Fewer Hallucinations
Browse by: Latest US Patents, China's latest patents, Technical Efficacy Thesaurus, Application Domain, Technology Topic, Popular Technical Reports.
© 2025 PatSnap. All rights reserved.Legal|Privacy policy|Modern Slavery Act Transparency Statement|Sitemap|About US| Contact US: help@patsnap.com