Preparation method of water-based polyurethane adhesive
A water-based polyurethane and adhesive technology, used in packaging films, shoe materials, and leather fields, can solve the problems of low solid content, hydrolysis resistance, low cohesive strength, etc., and achieve high bonding strength, good hydrolysis resistance, The effect of high solids content
- Summary
- Abstract
- Description
- Claims
- Application Information
AI Technical Summary
Problems solved by technology
Method used
Image
Examples
Embodiment 1
[0017] In the reaction equipment equipped with stirrer, thermometer and reflux condenser, add 146.14g of adipic acid, 61.03g of neopentyl glycol, 52.81g of 1,4-butanediol, 0.011g of catalyst antimony acetate, heat stabilizer Triphenyl phosphate 0.43g, start stirring, the temperature rises to 120~130°C to completely dissolve the adipic acid; keep refluxing for 1 hour with nitrogen gas to make the dibasic acid and dibasic alcohol interact to form a small molecular polyester; Reaction and dehydration at 150°C, control the temperature of the fractionation head at 100~102°C, gradually increase the temperature in the system to 240°C within 3~4 hours after the water is discharged, the temperature rises first slowly and then quickly; raise the temperature of the material to 240°C for 1 hour, and start Vacuum dehydration, so that the moisture generated by the polycondensation reaction escapes, and remove the small molecule polyester and a small amount of unreacted materials generated in...
Embodiment 2
[0021] 120g of polyester diol prepared by Example 1, 28.95gIPDI, 5.48gHDI are added with stirrer, thermometer, in the reaction device of reflux condenser, add 0.72g dibutyltin dilaurate, heat up after mixing React at 80-85°C for 2 hours, then add 2.32g of dimethylolpropionic acid dissolved in N-methylpyrrolidone NMP, 1.26g of 1,4-butanediol, 1.25g of trimethylolpropane, 0.48g of hydroxyl-terminated silicone oil Chain extension at 80°C, react for 3h, cool down to 35-40°C, add a certain amount of acetone, add 6.14g of 50% aqueous solution of sodium ethylenediaminoethanesulfonate, carry out chain extension at about 40°C for 1h, then add 1.52g of triethylamine was neutralized for 30min. Add the prepolymer to 156g of deionized water for high-speed dispersion and emulsification. The cooling water temperature is below 35°C. Finally, use 0.73g of post-chain extender ethylenediamine to perform chain extension, and distill and remove acetone to obtain a water-based polyurethane emulsion...
Embodiment 3
[0024] 120g is prepared by the polyester glycol of embodiment 1, 35.15gIPDI, 3gHDI is added and agitator is housed, and thermometer, in the reaction device of reflux condenser, add 0.72g dibutyltin dilaurate, heat up to after mixing uniformly React at 80-85°C for 2 hours, then add 1.65g of dimethylolpropionic acid dissolved in N-methylpyrrolidone NMP, 1.1g of 1,4-butanediol, 0.98g of trimethylolpropane, and 0.43g of hydroxyl-terminated silicone oil for chain extension Extend the chain at 80°C, react for 3 hours, cool down to 35-40°C, add a certain amount of acetone, add 8.12g of a 50% aqueous solution of sodium ethylenediaminoethanesulfonate, carry out chain extension at about 40°C for 1 hour, and then add 1.03 g triethylamine for neutralization for 30 minutes. Add the prepolymer to 142g of deionized water for high-speed dispersion and emulsification. The cooling water temperature is below 35°C. Finally, 0.84g of post-chain extender ethylenediamine is used for chain extension,...
PUM
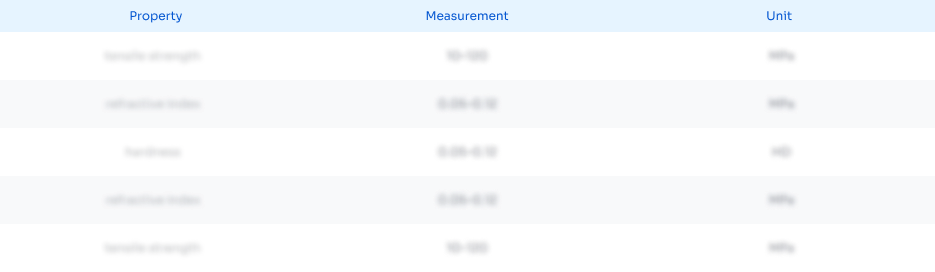
Abstract
Description
Claims
Application Information

- R&D Engineer
- R&D Manager
- IP Professional
- Industry Leading Data Capabilities
- Powerful AI technology
- Patent DNA Extraction
Browse by: Latest US Patents, China's latest patents, Technical Efficacy Thesaurus, Application Domain, Technology Topic, Popular Technical Reports.
© 2024 PatSnap. All rights reserved.Legal|Privacy policy|Modern Slavery Act Transparency Statement|Sitemap|About US| Contact US: help@patsnap.com