Method for comprehensive recovery of valuable metals from tin anode mud
A technology for tin anode slime and valuable metals, applied in the field of hydrometallurgy, can solve the problems of low removal rate of antimony, unrecoverable, short processing flow, etc., achieving good comprehensive recovery effect and reducing the degree of environmental pollution Effect
- Summary
- Abstract
- Description
- Claims
- Application Information
AI Technical Summary
Problems solved by technology
Method used
Examples
example 1
[0019] Example 1: The tin anode slime is crushed to a particle size of over 20 meshes, tin anode slime (Sn 37.60%, Sb 13.57%, Ag 0.27529%, Bi 0.72%, Cu 1.85%, Pb 18.12%, As 3.15%) mixed with sodium hydroxide, Water is mixed according to the mass ratio of 1:1:5, the pH value of the mixed material is greater than 12, put into the autoclave, the stirring speed is adjusted to 600rpm, the temperature is raised to 160°C under airtight conditions, and the temperature is stirred for 20min. Cooling, discharging, filtering. The tin leaching rate is 92%, and the antimony leaching rate is 88%. Add excess metal tin to the filtrate and heat it to above 80°C to purify and remove impurities. After purification, the liquid was heated to 70°C for electrowinning, cell voltage 2.8V, current efficiency 81%, cathode tin test results: Sn 99.04%, Sb 0.134%, As 0.11%, Bi 0.01%, Cu 0.063%, Pb 0.098%, Fe 0.022%, S 0.001%. The test results of the leaching slag after drying: Ag 1.16%, Bi 3.12, Cu 7.91,...
example 2
[0020]Example 2: The tin anode slime is crushed to a particle size of over 20 meshes, tin anode slime (Sn 39.00%, Sb 22.12%, Ag 0.47842%, Bi 2.64%, Cu 3.82%, Pb 2.96%, As 2.10%) and sodium hydroxide, Potassium sulfide and water are mixed according to the mass ratio of 1:1:0.02:5. The pH value of the mixed material liquid is greater than 12. Put it into the autoclave, adjust the stirring speed to 500rpm, raise the temperature to 210°C under airtight conditions, and pass oxygen to the autoclave. The pressure was 4MPa, and the mixture was stirred at constant temperature for 10 minutes. Cooling, discharging, filtering. The tin leaching rate is 96%. Add excess metal tin to the filtrate, heat it to 95°C, and purify and remove impurities. After purification, the liquid was heated to 80°C for electrowinning, the cell voltage was 2.6V, and the current efficiency was 89%. The cathode tin test results: Sn 99.95%, Sb 0.0086%, As 0.0010%, Bi 0.0011%, Cu 0.0035%, Pb 0.0044%, Fe 0.0052%, ...
example 3
[0021] Example 3: The tin anode slime is crushed to a particle size of over 20 meshes, tin anode slime (Sn 41.64%, Sb 23.15%, Ag 0.15637%, Bi 1.94%, Cu 4.02%, Pb 1.53%, As 2.61%) and potassium hydroxide, Sodium sulfide and water are mixed according to the mass ratio of 1:0.1:1:6, the pH value of the mixed material is greater than 12, put into the autoclave, the stirring speed is adjusted to 400rpm, the temperature is raised to 140°C under airtight conditions, and the temperature is stirred for 30min. Cooling, discharging, filtering. The tin leaching rate is 91%, and the antimony leaching rate is 86%. The filtrate is directly electrowinning, the solution temperature is 40°C, the cell voltage is 2.5V, and the current efficiency is 76%. The test results of the cathode tin-antimony alloy: Sn 8.15%, Sb 90.36%, As 0.69%, Bi 0.012%, Cu 0.0005%, Pb 0.0003%, Fe 0.036%. The test results after drying the leaching slag: Ag 0.81180%, Bi 10.12, Cu 19.28, Pb10.10. Oxidative roasting at 700...
PUM
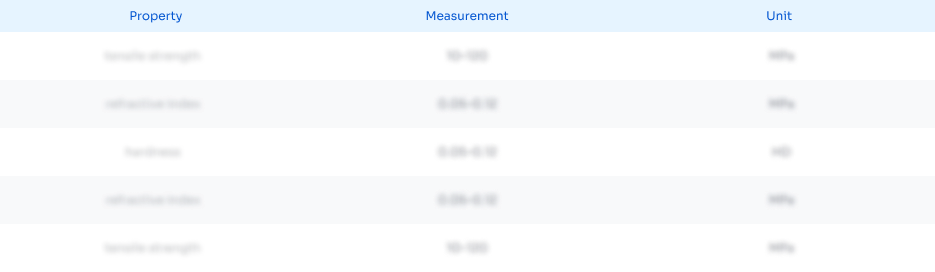
Abstract
Description
Claims
Application Information

- R&D
- Intellectual Property
- Life Sciences
- Materials
- Tech Scout
- Unparalleled Data Quality
- Higher Quality Content
- 60% Fewer Hallucinations
Browse by: Latest US Patents, China's latest patents, Technical Efficacy Thesaurus, Application Domain, Technology Topic, Popular Technical Reports.
© 2025 PatSnap. All rights reserved.Legal|Privacy policy|Modern Slavery Act Transparency Statement|Sitemap|About US| Contact US: help@patsnap.com