Method for circulative and comprehensive utilization of waste acids generated in acid preparation process through smoke smelting
A technology for smelting flue gas and acid circulation, which is used in the field of sulfur concentrate flotation system liquid purification, smelting flue gas acid production and cyanide tailings flotation copper concentrate, which can solve the impact of surrounding environment, difficult building materials, raw materials, etc. To deal with high cost problems, to reduce pollution, improve economic benefits, and achieve the effect of zero emissions
- Summary
- Abstract
- Description
- Claims
- Application Information
AI Technical Summary
Problems solved by technology
Method used
Image
Examples
Embodiment 1
[0016] 1) Sulfur-containing minerals (including various non-ferrous metal sulfide ores, pyrite, etc.) roasting flue gas acid production process produces waste acid
[0017] Sulfur-containing minerals are roasted with oxygen in the air at 600-1000°C to produce mixed flue gas containing sulfur dioxide, sulfur trioxide, water, mine dust and other volatile elements, which are sequentially subjected to dry dust removal, electrostatic dust removal, and wet dust removal. Purification removes impurities that affect the production of sulfuric acid. Among them, wet purification is a method of fully mixing the flotation system liquid with the mixed flue gas for purification. The acidic wastewater with a mass percentage of 2-15% sulfuric acid produced during the purification process is waste acid. The waste acid is retained separately; after the removal of impurities, the sulfur dioxide flue gas that meets the needs of sulfuric acid production is used for sulfuric acid production to produc...
Embodiment 2
[0029] 1) Sulfur-containing minerals (including various non-ferrous metal sulfide ores, pyrite, etc.) roasting flue gas acid production process produces waste acid
[0030] Sulfur-containing minerals and oxygen in the air are roasted at 600-1000°C to produce mixed flue gas containing sulfur dioxide, sulfur trioxide, water, mine dust and other volatile elements, which have been subjected to dry dust removal, electrostatic dust removal, and wet dust removal successively. Purification removes impurities that affect the production of sulfuric acid. Among them, wet purification is a method of fully mixing the flotation system liquid with the mixed flue gas for purification. The acidic wastewater with a mass percentage of 2-15% sulfuric acid produced during the purification process is waste acid. The waste acid is retained separately; after the removal of impurities, the sulfur dioxide flue gas that meets the needs of sulfuric acid production is used for sulfuric acid production to p...
Embodiment 3
[0042] 1) Sulfur-containing minerals (including various non-ferrous metal sulfide ores, pyrite, etc.) roasting flue gas acid production process produces waste acid
[0043]Sulfur-containing minerals and oxygen in the air are roasted at 600-1000°C to produce mixed flue gas containing sulfur dioxide, sulfur trioxide, water, mine dust and other volatile elements, which have been subjected to dry dust removal, electrostatic dust removal, and wet dust removal successively. Purification removes impurities that affect the production of sulfuric acid. Among them, wet purification is a method of fully mixing the flotation system liquid with the mixed flue gas for purification. The acidic wastewater with a mass percentage of 2-15% sulfuric acid produced during the purification process is waste acid. The waste acid is retained separately; after the removal of impurities, the sulfur dioxide flue gas that meets the needs of sulfuric acid production is used for sulfuric acid production to pr...
PUM
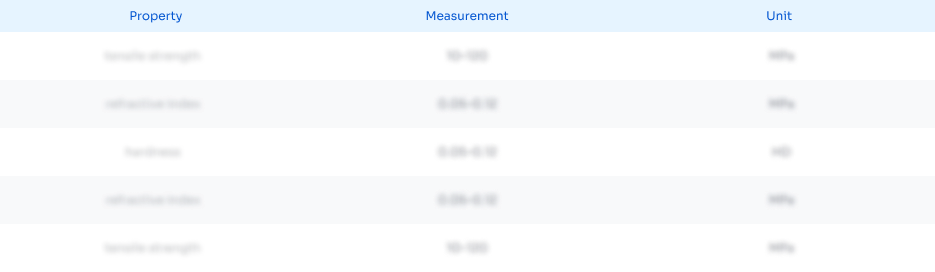
Abstract
Description
Claims
Application Information

- R&D
- Intellectual Property
- Life Sciences
- Materials
- Tech Scout
- Unparalleled Data Quality
- Higher Quality Content
- 60% Fewer Hallucinations
Browse by: Latest US Patents, China's latest patents, Technical Efficacy Thesaurus, Application Domain, Technology Topic, Popular Technical Reports.
© 2025 PatSnap. All rights reserved.Legal|Privacy policy|Modern Slavery Act Transparency Statement|Sitemap|About US| Contact US: help@patsnap.com