Rare earth-containing heat-resisting magnesium alloy
A magnesium alloy and rare earth technology, which is applied in the field of Mg-Al-RE heat-resistant die-casting magnesium alloys and rare earth-containing heat-resistant magnesium alloys, can solve the problems of increased application cost, use temperature not exceeding 120°C, poor alloy plasticity, etc. Achieve the effect of improving competitiveness, inhibiting dislocation climbing, and improving high temperature performance
- Summary
- Abstract
- Description
- Claims
- Application Information
AI Technical Summary
Problems solved by technology
Method used
Image
Examples
Embodiment 1
[0016] like figure 1 as shown, It can be seen from the microstructure that after the addition of rare earth, the Mg17All2 phase with poor thermal stability at the grain boundary is significantly suppressed, and the rare earth combines with aluminum in the magnesium alloy to form Al 11 (Ce, La) 3 and A1 2 Nd Mainly distributed in the grain boundaries and inside the grains.
[0017] Adopt cerium lanthanum rare earth and pure neodymium to prepare heat-resistant magnesium alloy containing rare earth, weight 50Kg, alloy chemical composition is as shown in Table 1:
[0018] Table 1 The chemical composition of rare earth-containing heat-resistant magnesium alloy prepared by using cerium-lanthanum rare earth and pure neodymium (Wt%)
[0019] Al RE RE ratio mn Mg 4.0 3.8 Ce:La:Nd=35:60:5 0.28 margin
[0020] The preparation process is as follows:
[0021] (1) Raw material preparation: magnesium ingot, weight 44.90kg; Al ingot, weight 1.07kg; cer...
Embodiment 2
[0026] The rare earth-containing heat-resistant magnesium alloy is prepared by using the magnesium-cerium-lanthanum-neodymium master alloy, the weight is 100Kg, and the chemical composition of the alloy is shown in Table 1:
[0027] Table 2 Chemical composition of rare earth-containing heat-resistant magnesium alloys prepared by magnesium-cerium-lanthanum-neodymium master alloy (Wt%)
[0028] Al RE RE ratio mn Mg 4.0 4.2 Ce:La:Nd=40:55:5 0.20 margin
[0029] The preparation process is as follows:
[0030] (1) Raw material preparation: magnesium ingot, weight 74.80kg; aluminum ingot, weight 2.66kg; magnesium-20% (cerium, lanthanum, neodymium) rare earth master alloy (rare earth weight ratio, Ce:La:Nd=40:55:5): , weight 21.00kg; Al-13%Mn master alloy, weight 1.54kg;
[0031] (2) Pretreatment: Preheat magnesium ingots, aluminum ingots, aluminum-manganese master alloys and magnesium-20% (cerium, lanthanum and neodymium) rare earth master al...
Embodiment 3
[0035] Adopt magnesium-cerium lanthanum neodymium master alloy and neodymium rare earth to prepare heat-resistant magnesium alloy containing rare earth, weight 100Kg, alloy chemical composition is as shown in Table 1:
[0036] Table 3 Chemical composition of rare earth-containing heat-resistant magnesium alloys prepared by using magnesium-cerium-lanthanum-neodymium master alloy and neodymium rare earth (Wt%)
[0037] Al RE RE ratio mn Mg 4.1 3.9 Ce:La:Nd=38:57:5 0.25 margin
[0038] The preparation process is as follows:
[0039] (1) Raw material preparation: magnesium ingot, weight 77.46kg; aluminum ingot, weight 1.89kg; magnesium-20% (cerium lanthanum) rare earth master alloy (rare earth weight ratio, Ce:La =38:57), weight 18.53kg; neodymium Rare earth, weight 0.20 kg; Al-13%Mn master alloy, weight 1.92 kg;
[0040] (2) Pretreatment: Preheat magnesium ingots, aluminum ingots, aluminum-manganese master alloys, magnesium-20% (cerium-lanthanum...
PUM
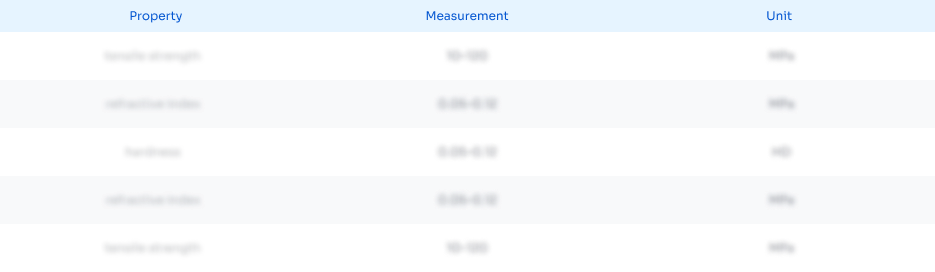
Abstract
Description
Claims
Application Information

- R&D
- Intellectual Property
- Life Sciences
- Materials
- Tech Scout
- Unparalleled Data Quality
- Higher Quality Content
- 60% Fewer Hallucinations
Browse by: Latest US Patents, China's latest patents, Technical Efficacy Thesaurus, Application Domain, Technology Topic, Popular Technical Reports.
© 2025 PatSnap. All rights reserved.Legal|Privacy policy|Modern Slavery Act Transparency Statement|Sitemap|About US| Contact US: help@patsnap.com