Textile frost resistance test standard sample and preparation method thereof
A technology for testing standards and standard samples, which is applied in the field of textile frost resistance test standard samples and its preparation, which can solve the problems of undetectable textile frost resistance and lack of methods for textile frost resistance, and achieve short inspection cycle and stable hardness , Check the effect of easy operation
- Summary
- Abstract
- Description
- Claims
- Application Information
AI Technical Summary
Problems solved by technology
Method used
Image
Examples
Embodiment 1
[0033] Embodiment 1 textile frost resistance test standard sample and its preparation
[0034] 1. Experimental materials
[0035] Fabric: polyester, warp and weft fineness 75*100 denier, warp and weft density 18.5 / 32 polyester white canvas, Wujiang Sanlian Printing and Dyeing Co., Ltd.
[0036]Chemicals: methacrylamide, chemically pure, Shanghai Lingfeng Chemical Co., Ltd.; water-based epoxy resin emulsion AB-EP-20, water-based epoxy curing agent AB-HGA, Zhejiang Anbang New Material Development Co., Ltd.; polyacetic acid Vinyl ester M-430, Hangzhou Meigao Huayi Chemical Co., Ltd.; formic acid, ammonia water, potassium persulfate, commercially available.
[0037] 2. Experimental method: Stiffening finishing method of polyester imitation silk
[0038] First, AB-EP-20 and AB-HGA are made into an epoxy resin finishing agent at a mass ratio of 1:0.6, and then mixed according to a mass ratio of polyvinyl acetate:epoxy resin finishing agent at a mass ratio of 7:1, and stirred evenl...
Embodiment 2
[0051] Example 2 Optimization Test of Polyester Stiffening Finishing Process
[0052] Select the prepared stiffening agent 100g / l, and test the finishing process conditions to determine the best stiffening formula and process conditions.
[0053] 1. The influence of pre-baking temperature
[0054] The experimental conditions are as follows: Squeezing rate: 100%, immersion time 1min, two dipping and two rolling, pre-baking for 3min, baking at 180°C for 3min. The experimental results are shown in Table 2.
[0055] Table 2 Effect of pre-drying temperature on polyester stiffness
[0056]
[0057] It can be seen from Table 2 that as the pre-drying temperature increases, the extension length of the polyester fabric increases, but when the temperature rises to 95°C, the stiffness does not increase significantly when the temperature continues to rise, so the preferred pre-drying temperature is 95°C. .
[0058] 2. The influence of pre-baking time
[0059] The experimental condi...
PUM
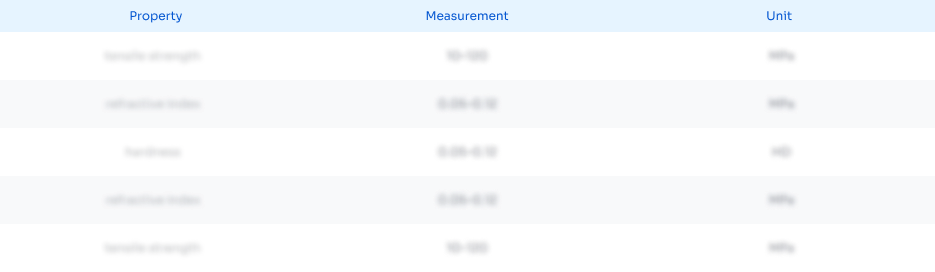
Abstract
Description
Claims
Application Information

- Generate Ideas
- Intellectual Property
- Life Sciences
- Materials
- Tech Scout
- Unparalleled Data Quality
- Higher Quality Content
- 60% Fewer Hallucinations
Browse by: Latest US Patents, China's latest patents, Technical Efficacy Thesaurus, Application Domain, Technology Topic, Popular Technical Reports.
© 2025 PatSnap. All rights reserved.Legal|Privacy policy|Modern Slavery Act Transparency Statement|Sitemap|About US| Contact US: help@patsnap.com