Epoxy resin double-component adhesion agent prepared by using cold box process as well as casting mixture and casting formed body
A method of epoxy resin and epoxy resin technology, applied in casting molding equipment, molds, cores, etc., can solve the problems of poor impact resistance and insignificant toughening effect
- Summary
- Abstract
- Description
- Claims
- Application Information
AI Technical Summary
Problems solved by technology
Method used
Image
Examples
Embodiment 1
[0052] Preparation of Polyurethane Modified Epoxy Resin
[0053] (1) Put 180 kg of melted benzyl ether phenolic resin (weight average molecular weight 600) into the reaction kettle, heat and stir, dehydrate under vacuum (vacuum degree is 15mm Hg), until the temperature reaches 120°C without bubbles. Cool down to 60°C, add 15 kg of polyisocyanate PM-200;
[0054] (2) Adjust the condenser of the reaction kettle to the reflux state, pass steam under stirring to raise the temperature, raise the temperature to 70°C within 30 minutes, and keep the temperature at 70-90°C for 180 minutes;
[0055] (3) After the heat preservation is over, cool the material to 60°C, add 805 kg of epoxy resin DER331, raise the temperature in the kettle to 110°C within 60 minutes, and keep the temperature at 110-150°C for 180 minutes, then cool down, that is Obtain polyurethane modified epoxy resin.
[0056] The preparation of component I: 600 kilograms of above-mentioned polyurethane modified epoxy res...
Embodiment 2
[0059] Preparation of Polyurethane Modified Epoxy Resin
[0060] (1) Put 160 kilograms of melted benzyl ether phenolic resin (weight average molecular weight 800) into the reaction kettle, heat and stir, dehydrate under vacuum (vacuum degree is 15 mm Hg), until the temperature reaches 120 ° C without bubbles. Cool down to 60°C, add 20 kg of polyisocyanate PM-200;
[0061] (2) Adjust the condenser of the reaction kettle to the reflux state, pass steam under stirring to raise the temperature, raise the temperature to 70°C within 30 minutes, and keep the temperature at 70-90°C for 180 minutes;
[0062] (3) After the heat preservation is over, cool the material to 60°C, add 820 kg of epoxy resin DER331, raise the temperature in the kettle to 110°C within 60 minutes, and keep the temperature at 110-150°C for 180 minutes, then cool down, that is Obtain polyurethane modified epoxy resin.
[0063] Preparation of component I: add 630 kilograms of the above-mentioned polyurethane modi...
Embodiment 3
[0066] Preparation of Polyurethane Modified Epoxy Resin
[0067] (1) Put 134 kg of melted benzyl ether phenolic resin (weight average molecular weight 1200) into the reaction kettle, heat and stir, dehydrate under vacuum (vacuum degree is 15 mm Hg), until the temperature reaches 120 ° C without bubbles. Cool down to 60°C, add 16 kg of polyisocyanate PM-200;
[0068] (2) Adjust the condenser of the reaction kettle to the reflux state, pass steam under stirring to raise the temperature, raise the temperature to 70°C within 30 minutes, and keep the temperature at 70-90°C for 180 minutes;
[0069] (3) After the heat preservation is over, cool the material to 60°C, add 850 kg of epoxy resin DER331, raise the temperature in the kettle to 110°C within 60 minutes, and keep the temperature at 110-150°C for 180 minutes, then cool down, that is Obtain polyurethane modified epoxy resin.
[0070] The preparation of component I: 610 kilograms of above-mentioned polyurethane modified epoxy...
PUM
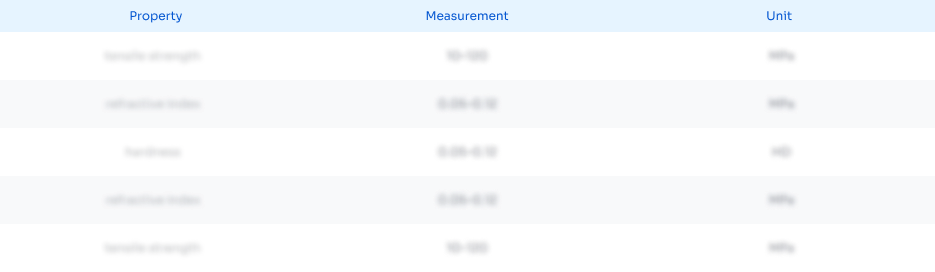
Abstract
Description
Claims
Application Information

- Generate Ideas
- Intellectual Property
- Life Sciences
- Materials
- Tech Scout
- Unparalleled Data Quality
- Higher Quality Content
- 60% Fewer Hallucinations
Browse by: Latest US Patents, China's latest patents, Technical Efficacy Thesaurus, Application Domain, Technology Topic, Popular Technical Reports.
© 2025 PatSnap. All rights reserved.Legal|Privacy policy|Modern Slavery Act Transparency Statement|Sitemap|About US| Contact US: help@patsnap.com