Preparing method for Ti-Si alloy target materials
A manufacturing method and technology of titanium-silicon alloy, applied in the field of metallurgy, can solve the problems of composition segregation, poor alloy ductility, brittle cracks, etc., and achieve the effects of wide composition ratio, high yield and fine grain size
- Summary
- Abstract
- Description
- Claims
- Application Information
AI Technical Summary
Problems solved by technology
Method used
Image
Examples
Embodiment approach 1
[0018] Embodiment 1: choose titanium powder with a purity of 99.9%, silicon powder with a purity of 99.99%, the average particle size of titanium powder is 42 μm, and the average particle size of silicon powder is 32 μm. Into the mixer, the mixing time is 9 hours. Put the mixed powder into the graphite mold, the size of the graphite mold is Ф300x300, the wall thickness is 20mm, then put it into the vacuum hot pressing furnace, apply 5MPa pressure to the upper and lower pressure heads for pre-compression, and then the vacuum system starts to vacuum, when the vacuum degree When it reaches 1*10-2Pa, raise the temperature to 650°C, keep it warm for 2 hours, then quickly raise the temperature to 1000°C, the heating rate is 70°C / min, and pressurize to 10MPa, keep it warm for 4 hours, stop heating, and take it out of the furnace after cooling with the furnace. Machined to get the final 90 / 10 titanium silicon round target.
Embodiment approach 2
[0019] Embodiment 2: choose titanium powder with a purity of 99.95%, silicon powder with a purity of 99.99%, the average particle size of titanium powder is 62 μm, and the average particle size of silicon powder is 40 μm. Into the mixer, mixing time 1 hour. Put the mixed powder into the graphite mold, the size of the graphite mold is Ф350x350, the wall thickness is 20mm, and then put it into the vacuum hot pressing furnace, apply 10MPa pressure to the upper and lower pressure heads for pre-compression, and then the vacuum system starts to vacuum, when the vacuum degree When it reaches 1*10-2Pa, raise the temperature to 700°C, keep it warm for 3 hours, then rapidly raise the temperature to 1100°C, the heating rate is 80°C / min, and pressurize to 40MPa, keep it warm for 2 hours, stop heating, and take it out of the furnace after cooling with the furnace. Machined to get the final 70 / 30 titanium silicon round target.
Embodiment approach 3
[0020] Embodiment 3: choose titanium powder with a purity of 99.99%, silicon powder with a purity of 99.91%, the average particle size of titanium powder is 80 μm, and the average particle size of silicon powder is 100 μm. Pack into the mixer, and the mixing time is 7 hours. Put the mixed powder into the graphite mold, the size of the graphite mold is Ф400x400, the wall thickness is 20mm, and then put it into the vacuum hot pressing furnace, apply 15MPa pressure to the upper and lower pressure heads for pre-compression, and then the vacuum system starts to vacuum, when the vacuum degree When it reaches 1*10-2Pa, raise the temperature to 750°C, keep it warm for 4 hours, then quickly raise the temperature to 1300°C, the heating rate is 100°C / min, and pressurize to 80MPa, keep it warm for 6 hours, stop heating, and take it out of the furnace after cooling , machining to get the final 50 / 50 titanium silicon round target.
PUM
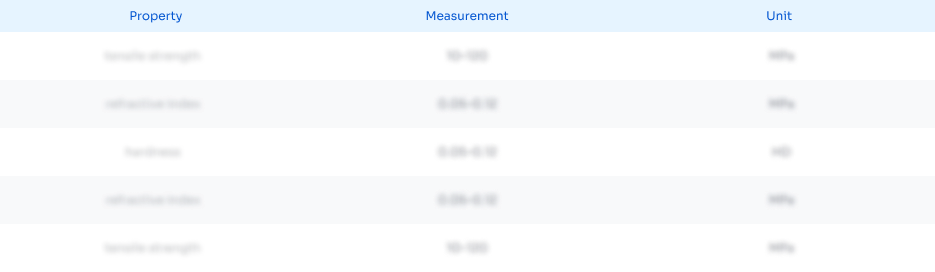
Abstract
Description
Claims
Application Information

- R&D
- Intellectual Property
- Life Sciences
- Materials
- Tech Scout
- Unparalleled Data Quality
- Higher Quality Content
- 60% Fewer Hallucinations
Browse by: Latest US Patents, China's latest patents, Technical Efficacy Thesaurus, Application Domain, Technology Topic, Popular Technical Reports.
© 2025 PatSnap. All rights reserved.Legal|Privacy policy|Modern Slavery Act Transparency Statement|Sitemap|About US| Contact US: help@patsnap.com