Flaky flat viscose fiber and preparation method thereof
A flat viscose and fiber technology, applied in the field of cellulose fiber, can solve the problems of restricting the development of flat viscose fiber, high price, and few reports on the development of flat fiber, so as to achieve superior moisture permeability, full hand feeling and reduce equipment investment Effect
- Summary
- Abstract
- Description
- Claims
- Application Information
AI Technical Summary
Problems solved by technology
Method used
Image
Examples
Embodiment 1
[0024] The dissolved sodium carbonate solution is injected into the spinning viscose through a syringe pump before viscose spinning, and is fully mixed with the spinning viscose solution to obtain a mixed spinning viscose. 40wt% of a fiber.
[0025] The mixed spun viscose was spun in a coagulation bath containing sulfuric acid 120g / l, zinc sulfate 11g / l, sodium sulfate 330g / l, and a temperature of 51°C.
[0026] The formed nascent fiber is drawn, and the spray-guided draft is 45%, and then plasticized and drawn, washed with water, desulfurized, oiled and dried to obtain sheet-like flat viscose fiber.
Embodiment 2
[0028] The sodium bicarbonate solution that dissolves is joined in the viscose solution after the yellowing finishes, fully mixes with the viscose solution, the add-on of sodium bicarbonate is 45wt% of methyl cellulose in the cellulose viscose, then through mixing, The steps of dissolving, filtering, defoaming, ripening, and filtering before spinning are used to obtain the mixed spinning viscose.
[0029] The mixed spun viscose was spun in a coagulation bath containing 140 g / l of sulfuric acid, 9 g / l of aluminum sulfate and 335 g / l of sodium sulfate at a temperature of 50°C.
[0030] The formed nascent fibers are drawn, and the spray-guided draft is 55%, and then plasticized and drawn, washed with water, desulfurized, oiled and dried to obtain sheet-like flat viscose fibers.
Embodiment 3
[0032] The mixed solution of dissolved sodium carbonate and sodium bicarbonate is added to the viscose solution in the post-dissolution process, fully mixed with the viscose solution, and the total addition of sodium carbonate and sodium bicarbonate is cellulose viscose. 38wt% of the fiber, and then through the steps of dissolving, filtering, defoaming, ripening, and pre-spinning filtration to obtain mixed spinning viscose.
[0033] The mixed spun viscose was spun in a coagulation bath containing 105 g / l of sulfuric acid, 10 g / l of zinc sulfate and 10 g / l of aluminum sulfate, 290 g / l of sodium sulfate, and a temperature of 55°C.
[0034] The formed nascent fiber is drawn, and its spray draft is 37%, and then plasticized and drawn, washed with water, desulfurized, oiled and dried to obtain sheet-like flat viscose fiber.
PUM
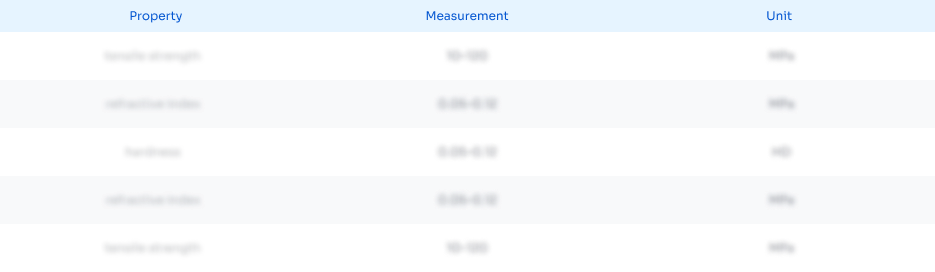
Abstract
Description
Claims
Application Information

- R&D
- Intellectual Property
- Life Sciences
- Materials
- Tech Scout
- Unparalleled Data Quality
- Higher Quality Content
- 60% Fewer Hallucinations
Browse by: Latest US Patents, China's latest patents, Technical Efficacy Thesaurus, Application Domain, Technology Topic, Popular Technical Reports.
© 2025 PatSnap. All rights reserved.Legal|Privacy policy|Modern Slavery Act Transparency Statement|Sitemap|About US| Contact US: help@patsnap.com