Polycrystalline silicon reduction furnace lining coating and production method thereof
A manufacturing method and reduction furnace technology, which can be applied to manufacturing tools, glass manufacturing equipment, glass cutting devices, etc., and can solve problems such as reducing production costs
- Summary
- Abstract
- Description
- Claims
- Application Information
AI Technical Summary
Problems solved by technology
Method used
Image
Examples
example 1
[0021] Example 1: The inner wall of the reduction furnace is mechanically polished, cleaned with organic solvents and pure water, dried and then plated. The system is evacuated, and after reaching the predetermined vacuum degree (10 -4 Pa or so), use an infrared heating element to heat the furnace wall to 300-600°C for baking and degassing. After the degassing is completed, the inner wall of the reduction furnace is cleaned by ion glow discharge with argon gas. Using multi-arc ion plating technology, the furnace wall is the workpiece to be plated (negative potential relative to the multi-arc target), and the temperature of the inner wall of the reduction furnace is controlled at about 300-500°C. First, a layer of pure titanium with a thickness of 0.1-0.5 microns is prepared, and then Nitrogen, grow a layer of 1-10 micron TiN x layer, slowly cooled to room temperature, and the lining coating is prepared.
example 2
[0022] Example 2: The inner wall of the reduction furnace is mechanically polished, washed with organic solvents and pure water, dried and then plated. The system is evacuated, and after reaching the predetermined vacuum degree (10 -4 Pa around), using an infrared heating element to heat the inner wall of the reduction furnace to 300-500°C for baking and degassing. After the degassing is completed, argon gas is passed to perform glow discharge cleaning on the inner wall of the reduction furnace. Using the magnetron sputtering method, the furnace wall is the workpiece to be plated (positive potential relative to the sputtering target), deposit a layer of 0.1-0.5 micron thick pure titanium layer at an ambient temperature of 300-500 ° C, and then grow a layer of nitrogen gas 1-10 micron TiN x layer, slowly cooled to room temperature, and the lining coating is prepared.
example 3
[0023]Example 3: The inner wall of the reduction furnace is mechanically polished, washed with organic solvents and pure water, dried and then plated. The system is vacuumed and the inner wall of the reduction furnace is heated to 300-500°C, and baked for 15 hours to remove the water vapor and other impurity gases adsorbed on the furnace wall. TiCl 4 and ammonia NH 3 Reactive gas, deposition of titanium nitride TiN at a temperature of 400-500°C x After stopping the coating, slowly cool the furnace body to room temperature, and the lining coating is prepared.
[0024] According to the methods of the above embodiments, the lining coating of the reduction furnace can be produced, and the performance test also meets the relevant technical indicators, and also possesses the above-mentioned superiority and significant technical and economic effects compared with the prior art. .
PUM
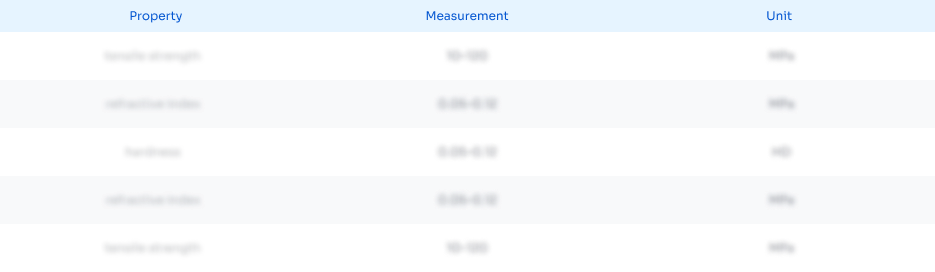
Abstract
Description
Claims
Application Information

- R&D Engineer
- R&D Manager
- IP Professional
- Industry Leading Data Capabilities
- Powerful AI technology
- Patent DNA Extraction
Browse by: Latest US Patents, China's latest patents, Technical Efficacy Thesaurus, Application Domain, Technology Topic, Popular Technical Reports.
© 2024 PatSnap. All rights reserved.Legal|Privacy policy|Modern Slavery Act Transparency Statement|Sitemap|About US| Contact US: help@patsnap.com