Method for compositely refining solidification structure of magnesium alloy by combination of current and Zr
A technology of solidification structure and magnesium alloy, which is applied in the field of metal materials and metallurgy, to achieve the effects of reducing cold shock, improving quality, and novel ideas
- Summary
- Abstract
- Description
- Claims
- Application Information
AI Technical Summary
Problems solved by technology
Method used
Image
Examples
Embodiment 1
[0041] WE43 magnesium alloy (Mg-4wt.%Y-2wt.%Nd-1wt.%Gd-0.5wt.%Zr, wherein, wt.% refers to the percentage of components in the total mass of the prepared magnesium alloy) batch melting refining The process is as follows: paint all tools in advance, and dry the tools, charge, and refining agent at 180°C for more than 4 hours; turn on the resistance furnace, preheat the stainless steel melting crucible 5 to dark red, add magnesium ingots, and start to pass through the protection at 500°C The gas mixing device 1 and the blowing pipe 4 are fed with CO with a volume ratio of 100:1. 2 +5F 6 Protect the gas until the melting and casting work is completely completed; heat the melting crucible 5 to 690°C until the pure magnesium is completely melted, adjust the temperature to 720-740°C, and add Mg-25wt.%Y master alloy after the temperature is stable; wait until it is completely melted, melt When the body temperature is stable at 720-740°C, add mixed rare earth master alloy (Mg-25wt.%Nd...
Embodiment 2
[0045] ZM6 magnesium alloy (Mg-2.6wt.% Nd-0.6wt.% Zn-0.8wt.% Zr) batching melting and refining process is as follows: all tools are painted in advance, and tools, charge and refining agent are dried at 180 ° C for 4 hours above; turn on the resistance furnace, preheat the stainless steel melting crucible 5 to dark red, add magnesium ingots, and start feeding CO with a volume ratio of 100:1 at 500°C 2 +SF 6 Protect the gas until the melting and casting work is completed; heat the melting crucible 5 to 690°C until the pure magnesium is completely melted, adjust the temperature to 720-740°C, and add Zn after the temperature is stable; when the Zn is completely melted, the melt temperature is stable at 720-740 At ℃, add Mg-30wt.%Nd master alloy, stir 2 minutes by refining spoon after melting completely; Adjust the temperature to 790 ℃ and add the Zr-containing compound (mass ratio is K2ZrF6: NaCl: KCl =2:1:1), after it is completely melted, stir it for 7-10 minutes; let it stand ...
Embodiment 3
[0049] ZM2 magnesium alloy (Mg-4.2wt.%Zn-Nd1.5wt.%-0.6wt.%Zr) batching melting and refining process is as follows: all tools are painted in advance, and tools, charge and refining agent are dried at 180 ° C for 4 hours above; turn on the resistance furnace, preheat the stainless steel melting crucible 5 to dark red, add magnesium ingots, and start feeding CO with a volume ratio of 100:1 at 500°C 2 +SF 6 Protect the gas until the melting and casting work is completed; heat the melting crucible 5 to 690°C until the pure magnesium is completely melted, adjust the temperature to 720-740°C, and add Zn after the temperature is stable; when the Zn is completely melted, the melt temperature is stable at 720-740 At ℃, add cerium-rich mixed rare earth, stir for 2 minutes with a refining spoon after completely melting; adjust the temperature to 780℃, add Mg-30wt.%Zr master alloy with a mass of 0.8% of the total amount of the alloy, and stir at the bottom after it is completely melted 7 ...
PUM
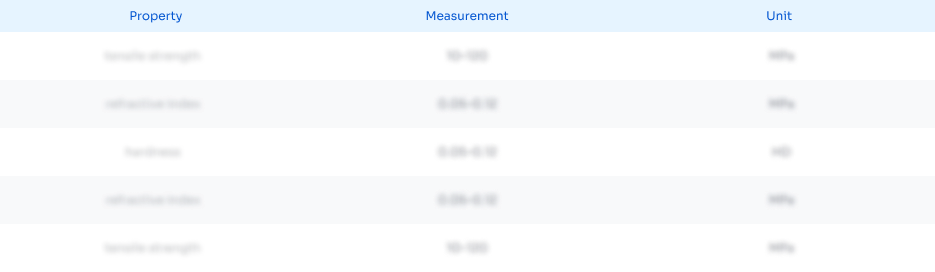
Abstract
Description
Claims
Application Information

- R&D
- Intellectual Property
- Life Sciences
- Materials
- Tech Scout
- Unparalleled Data Quality
- Higher Quality Content
- 60% Fewer Hallucinations
Browse by: Latest US Patents, China's latest patents, Technical Efficacy Thesaurus, Application Domain, Technology Topic, Popular Technical Reports.
© 2025 PatSnap. All rights reserved.Legal|Privacy policy|Modern Slavery Act Transparency Statement|Sitemap|About US| Contact US: help@patsnap.com