Acrylate emulsion used for vacuum aluminum plating and laser embossing and preparation method thereof
An acrylate, vacuum aluminum plating technology, applied in the direction of coating, can solve the problems of high temperature resistance, film performance impact, construction difficulties, etc., to achieve the effect of excellent temperature resistance, excellent water resistance and wide application range
- Summary
- Abstract
- Description
- Claims
- Application Information
AI Technical Summary
Problems solved by technology
Method used
Examples
Embodiment 1
[0038] This embodiment relates to an acrylic emulsion for vacuum aluminum plating and laser embossing, and its preparation method includes the following steps:
[0039] 1. Prepare materials according to the components and parts by weight described in Table 1;
[0040] 2. Use 9.5 parts of water to dissolve 0.3 parts of ammonium persulfate solvent uniformly to prepare an initiator solution for use; mix the polymerizable carboxylic acid, methacrylate, acrylate and silicon-containing crosslinkable monomer uniformly to form a mixture Single, spare;
[0041] 3. First dissolve 2 parts of emulsifier, 47.5 parts of water and 0.3 parts of pH buffer in the emulsifying kettle;
[0042] 4. When the temperature of the reaction kettle rises to 55°C, add 4 parts of mixed monomers to the reaction kettle, and disperse quickly (about 200 revolutions / min) for 1 hour under a nitrogen atmosphere;
[0043] 5. After the dispersion is uniform, the stirring is reduced to about 60 rpm, and the temperature is rai...
Embodiment 2
[0053] This embodiment relates to an acrylic emulsion for vacuum aluminum plating and laser embossing, and its preparation method includes the following steps:
[0054] 1. Prepare materials according to the components and parts by weight described in Table 1;
[0055] 2. Use 20 parts of water to uniformly prepare 0.4 part of ammonium persulfate solvent to prepare an initiator solution for use; mix the polymerizable carboxylic acid, methacrylate, acrylate and silicon-containing crosslinkable monomer uniformly to form a mixed unit Body, spare
[0056] 3. First dissolve 3 parts of polymerizable emulsifier, 60 parts of water and 0.4 part of pH buffer in the emulsifying kettle;
[0057] 4. When the temperature of the reaction kettle rises to 60°C, add 8 parts of mixed monomers to the reaction kettle, and disperse quickly (about 200 revolutions / min) for 1 hour under a nitrogen atmosphere;
[0058] 5. After the dispersion is uniform, the stirring is reduced to about 60 rpm, and the temperatur...
Embodiment 3
[0068] This embodiment relates to an acrylic emulsion for vacuum aluminum plating and laser embossing, and its preparation method includes the following steps:
[0069] 1. Prepare materials according to the components and parts by weight described in Table 1;
[0070] 2. Use 36 parts of water to uniformly dissolve 0.7 parts of ammonium persulfate into an initiator solution for use; mix the polymerizable carboxylic acid, methacrylate, acrylate and silicon-containing crosslinkable monomers uniformly to form a mixed unit Body, spare
[0071] 3. First dissolve 4 parts of emulsifier, 144 parts of water and 0.4 part of pH buffer in the emulsifying kettle;
[0072] 4. After the temperature of the reaction kettle rises to 50°C, add 13 parts of mixed monomers to the reaction kettle, and disperse quickly (about 200 revolutions / min) for 1 hour under a nitrogen atmosphere;
[0073] 5. After the dispersion is uniform, the stirring is reduced to about 60 rpm, and the temperature is raised. After the...
PUM
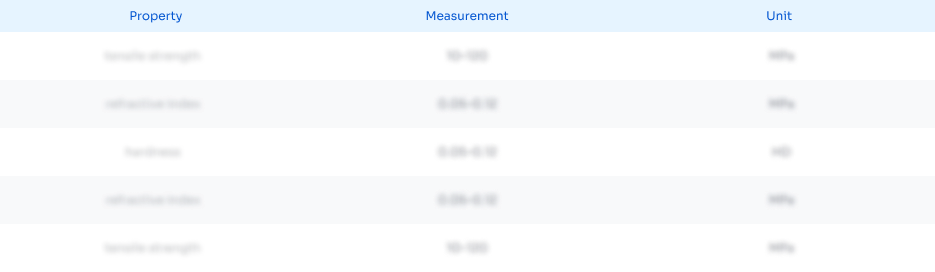
Abstract
Description
Claims
Application Information

- Generate Ideas
- Intellectual Property
- Life Sciences
- Materials
- Tech Scout
- Unparalleled Data Quality
- Higher Quality Content
- 60% Fewer Hallucinations
Browse by: Latest US Patents, China's latest patents, Technical Efficacy Thesaurus, Application Domain, Technology Topic, Popular Technical Reports.
© 2025 PatSnap. All rights reserved.Legal|Privacy policy|Modern Slavery Act Transparency Statement|Sitemap|About US| Contact US: help@patsnap.com