Textile water-based pigment printing binding agent and preparation method
A water-based paint and paint printing technology, applied in the direction of adhesive types, textiles and papermaking, ester copolymer adhesives, etc. Brightness, improved toughness and wear resistance, and storage stability
- Summary
- Abstract
- Description
- Claims
- Application Information
AI Technical Summary
Problems solved by technology
Method used
Image
Examples
Embodiment 1
[0032] 1. Emulsion polymerization:
[0033] 1) Raw material weight ratio: 33 grams of acrylonitrile, 34 grams of ethyl acrylate, 123 grams of butyl acrylate, 3.5 grams of acrylic acid, 3 grams of hydroxyethyl methacrylate, 2 grams of acrylamide, 1.5 grams of sodium lauryl sulfate , 6 grams of lauryl alcohol polyoxyethylene (10) ether, 300 grams of deionized water, 0.8 grams of ammonium persulfate, and 0.4 grams of sodium bisulfite;
[0034] 2) Mix 0.8 g of ammonium persulfate and 15 g of deionized water to obtain an aqueous solution of ammonium persulfate for use;
[0035] 3) Mix 0.4 g of sodium bisulfite and 15 g of deionized water to obtain an aqueous solution of sodium bisulfite for use;
[0036] 4) Add 175 grams of deionized water, 1.5 grams of the emulsifier sodium lauryl sulfate, and 6 grams of lauryl alcohol polyoxyethylene (10) ether into the pre-emulsion kettle, and then add all the monomer propylene 2 grams of amide, 33 grams of acrylonitrile, 34 grams of ethyl acr...
Embodiment 2
[0042] 1. Emulsion polymerization:
[0043] 1) Raw material weight ratio: 34 grams of acrylonitrile, 35 grams of ethyl acrylate, 124 grams of butyl acrylate, 3.7 grams of acrylic acid, 3.2 grams of hydroxyethyl methacrylate, 2.2 grams of acrylamide, 1.6 grams of sodium lauryl sulfate , 6.4 grams of lauryl alcohol polyoxyethylene (10) ether, 304 grams of deionized water, 0.82 grams of ammonium persulfate, and 0.41 grams of sodium bisulfite;
[0044] 2) Mix 0.82 g of ammonium persulfate and 15 g of deionized water to obtain an aqueous solution of ammonium persulfate for use;
[0045] 3) Mix 0.41 g of sodium bisulfite and 15 g of deionized water to obtain an aqueous solution of sodium bisulfite for use;
[0046]4) Add 177 grams of deionized water, 1.6 grams of the emulsifier sodium lauryl sulfate, and 6.4 grams of polyoxyethylene lauryl alcohol (10) ether into the pre-milk kettle, and then add all the monomer propylene 2.2 grams of amide, 34 grams of acrylonitrile, 35 grams of ...
Embodiment 3
[0052] 1. Emulsion polymerization:
[0053] 1) Raw material weight ratio: 34.5 grams of acrylonitrile, 35.5 grams of ethyl acrylate, 124.5 grams of butyl acrylate, 3.8 grams of acrylic acid, 3.3 grams of hydroxyethyl methacrylate, 2.3 grams of acrylamide, 1.7 grams of sodium lauryl sulfate , 6.8 grams of lauryl alcohol polyoxyethylene (10) ether, 308 grams of deionized water, 0.86 grams of ammonium persulfate, and 0.43 grams of sodium bisulfite;
[0054] 2) Mix 0.86 g of ammonium persulfate and 15 g of deionized water to obtain an aqueous solution of ammonium persulfate for use;
[0055] 3) Mix 0.43 g of sodium bisulfite and 15 g of deionized water to obtain an aqueous solution of sodium bisulfite for use;
[0056] 4) Add 179 grams of deionized water, 1.7 grams of the emulsifier sodium lauryl sulfate, and 6.8 grams of lauryl alcohol polyoxyethylene (10) ether into the pre-milk kettle, and then add all the monomer propylene 2.3 grams of amide, 34.5 grams of acrylonitrile, 35....
PUM
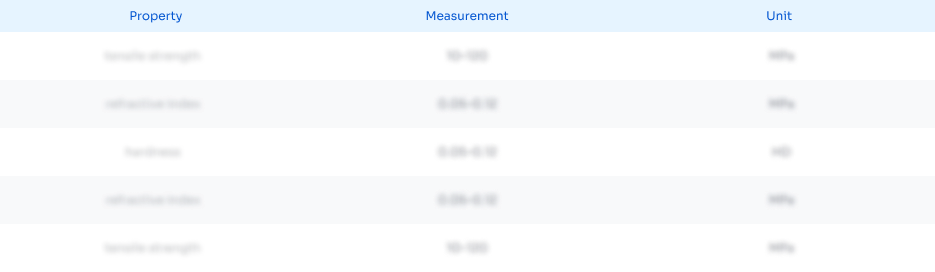
Abstract
Description
Claims
Application Information

- R&D
- Intellectual Property
- Life Sciences
- Materials
- Tech Scout
- Unparalleled Data Quality
- Higher Quality Content
- 60% Fewer Hallucinations
Browse by: Latest US Patents, China's latest patents, Technical Efficacy Thesaurus, Application Domain, Technology Topic, Popular Technical Reports.
© 2025 PatSnap. All rights reserved.Legal|Privacy policy|Modern Slavery Act Transparency Statement|Sitemap|About US| Contact US: help@patsnap.com