BOPP thermosensitive membrane and production method thereof
A manufacturing method and heat-sensitive technology, which can be used in chemical instruments and methods, papermaking, textiles and papermaking, etc., can solve problems such as unsatisfactory use requirements, achieve high protection performance and printing adaptability, meet firm bonding, and excellent three-proof performance effect
- Summary
- Abstract
- Description
- Claims
- Application Information
AI Technical Summary
Problems solved by technology
Method used
Image
Examples
Embodiment 1
[0035] The manufacture method of above-mentioned BOPP thermosensitive film, comprises the steps:
[0036] (1) Choose a light-sub-BOPP film as the coating substrate, and the weight is 55g / m 2 ;
[0037] (2) Preparation of primer coating solution: Add hollow balls into the batching tank, start stirring, add dispersant, pure acrylic latex, water-based chlorinated polypropylene emulsion, CMC, defoamer, lubricant, and stir at low speed Stir for 30 minutes to form an undercoat coating solution for use;
[0038] Described undercoat is made up of following component by weight shown:
[0039] Dispersant: 0.7 parts, hollow ball: 60 parts, pure acrylic latex: 30 parts, water-based chlorinated polypropylene emulsion: 5 parts, CMC: 1.5 parts, defoamer: 0.8 parts, lubricant: 2 parts.
[0040](3) Preparation of chromogenic layer coating solution: add water to the chromogenic layer batching tank, start stirring, add dispersant, defoamer, color developer 3,3′-diallyl-4,4′-di Hydroxydipheny...
Embodiment 2
[0048] The manufacture method of above-mentioned BOPP thermosensitive film, comprises the steps:
[0049] (1) Use double-sided glossy BOPP film as the coating substrate, with a weight of 65g / m 2 ;
[0050] (2) Preparation of primer coating solution: Add hollow balls into the batching tank, start stirring, add dispersant, pure acrylic latex, water-based chlorinated polypropylene emulsion, CMC, defoamer, lubricant, and stir at low speed Stir for 30 minutes to form an undercoat coating solution for use;
[0051] Described undercoat is made up of following components by weight shown:
[0052] Dispersant: 0.7 parts, hollow sphere: 61 parts, pure acrylic latex: 28 parts, water-based chlorinated polypropylene emulsion: 6 parts, CMC: 1.5 parts, defoamer: 0.8 parts, lubricant: 2 parts.
[0053] (3) Preparation of chromogenic layer coating solution: Add water to the chromogenic layer batching tank, start stirring, add dispersant, defoamer, color developer 2,4-diphenylsulfone phenol g...
PUM
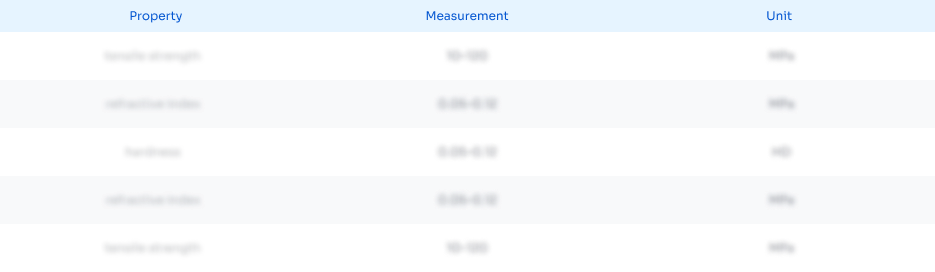
Abstract
Description
Claims
Application Information

- Generate Ideas
- Intellectual Property
- Life Sciences
- Materials
- Tech Scout
- Unparalleled Data Quality
- Higher Quality Content
- 60% Fewer Hallucinations
Browse by: Latest US Patents, China's latest patents, Technical Efficacy Thesaurus, Application Domain, Technology Topic, Popular Technical Reports.
© 2025 PatSnap. All rights reserved.Legal|Privacy policy|Modern Slavery Act Transparency Statement|Sitemap|About US| Contact US: help@patsnap.com