Active belite-sulphate aluminum cement clinker and preparation method for active belite-sulphate aluminum cement clinker
A Belite sulfoaluminate and cement clinker technology, which is applied in the field of building materials, can solve the problems of increased difficulty, increased production cost of cement clinker, complicated clinker calcination, etc., and achieves simple ingredients, reduced emissions, and reduced The effect of production costs
- Summary
- Abstract
- Description
- Claims
- Application Information
AI Technical Summary
Problems solved by technology
Method used
Image
Examples
Embodiment 1
[0016] Mix 3.25kg of crushed limestone 1 and 0.45kg of gypsum 1 with 1.30kg of fly ash 1 and grind them in a test ball mill until the sieve residue on an 80 μm square hole sieve is 8-12%. Add raw meal powder to 1% tap water, stir evenly, put it into a round abrasive mold with an inner diameter of 8cm and a depth of 2cm, press it into a cake with a small press, and dry the cake in an oven at 100°C. Take 10 pieces of material cakes each time, put them into a test electric furnace heated to 1320° C. and calcinate for 60 minutes until all the material cakes are completely burned. The calcined clinker is cooled to room temperature by fan blowing.
[0017] The weight percentages of the three raw materials are: 65.0% limestone 1, 26.0% fly ash 1, and 9.0% gypsum 1. Its chemical composition is shown in Table 1.
[0018] Table 1 Chemical composition of three kinds of raw materials
[0019] LOSS
[0020] After crushing the cooled clinker, use a ball mill to grind to a spe...
Embodiment 2
[0028] The fly ash 1 in the implementation case is replaced by another fly ash 2 with higher alumina content, and the limestone and gypsum remain unchanged. The three raw materials are 2.75kg limestone 1, 0.75kg gypsum 1, and 1.50kg powder The ratio of fly ash to 2 is mixed. The preparation method of raw meal and clinker is exactly the same as embodiment case 1.
[0029] The weight percentages of the three raw materials are: 55.0% of limestone, 30.0% of fly ash and 15.0% of gypsum. Its chemical composition is shown in Table 4.
[0030] Table 4 The chemical composition of the three raw materials
[0031] LOSS
SiO 2
Al 2 o 3
Fe 2 o 3
CaO
MgO
TiO 2
SO 3
fly ash 2
2.10
40.62
49.54
2.89
2.24
0.56
1.20
0.20
Limestone 1
43.66
0.50
0.20
0.14
54.20
1.10
0.00
0.03
plaster 1
3.69
2.24
0.69
0.58 ...
Embodiment 3
[0039] The fly ash 2 in the implementation case 2 is replaced by another fly ash 3, the limestone 1 is replaced by limestone 2, and the gypsum 1 is replaced by gypsum 2. The three raw materials are 561kg limestone, 145kg gypsum, and 294kg fly ash 2. The proportions are mixed evenly. Utilize the semi-industrialized vertical mill to grind all the materials until the sieve residue of the 80 μm square hole sieve is 8-12%, and obtain about 1 ton of raw meal powder. Feed the raw meal powder directly into the semi-industrialized kiln, control the appropriate feeding amount and the flow rate of the material in the kiln, ensure that there is sufficient ventilation and oxidizing atmosphere in the kiln, and make the material stay in the high temperature zone of 1300-1380 ° C for 30 -40 minutes, until all the clinker minerals are formed, and the fired clinker is cooled to room temperature by a single cylinder cooler.
[0040] The weight percentages of the three raw materials are: 56.1% o...
PUM
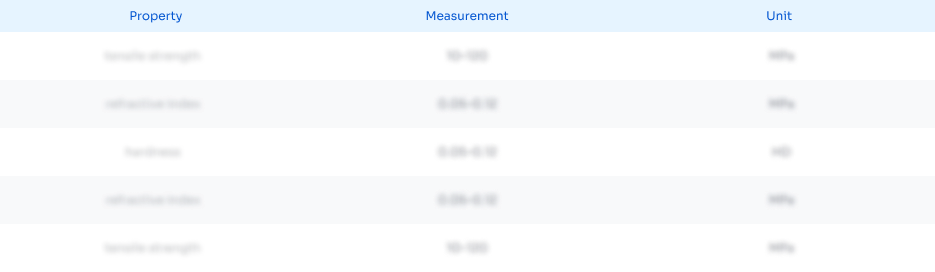
Abstract
Description
Claims
Application Information

- R&D
- Intellectual Property
- Life Sciences
- Materials
- Tech Scout
- Unparalleled Data Quality
- Higher Quality Content
- 60% Fewer Hallucinations
Browse by: Latest US Patents, China's latest patents, Technical Efficacy Thesaurus, Application Domain, Technology Topic, Popular Technical Reports.
© 2025 PatSnap. All rights reserved.Legal|Privacy policy|Modern Slavery Act Transparency Statement|Sitemap|About US| Contact US: help@patsnap.com