Preparation method of small-size density-controllable silicon nanodot array
A technology of silicon nano and dot arrays, which is applied in the field of preparation of small-sized density thyristor nano dot arrays by electrochemical etching, and achieves good application prospects, uniform size distribution, and controllable nano dot size and density
- Summary
- Abstract
- Description
- Claims
- Application Information
AI Technical Summary
Problems solved by technology
Method used
Image
Examples
Embodiment 1
[0059] (1) Depositing an aluminum film on a silicon wafer: Deposit an aluminum film with a thickness of 1 μm on a single crystal silicon by magnetron sputtering.
[0060] (2) Annealing: anneal the silicon wafer after the aluminum film is deposited in a nitrogen atmosphere at 350° C. for 6 h to increase the grain size of the deposited aluminum film and improve the bonding degree between it and the substrate.
[0061] (3) Carrying out anodic oxidation on the aluminum film: in 15wt% sulfuric acid, the oxidation is carried out at a voltage of 20V. Oxidation proceeds to stop at point E. figure 1 A typical current density / time curve of the anodic oxidation process on a silicon substrate is given, where point E represents the complete end of oxidation, and any time after point E can be selected to stop the oxidation process.
[0062] (4) Remove the anodic aluminum oxide film formed in step 3 and the silicon dioxide spots on the surface of the silicon substrate: use 6% phosphoric aci...
Embodiment 2
[0065] (1) Depositing an aluminum film on a silicon wafer: an aluminum film with a thickness of 1.5 μm is deposited on a single crystal silicon by electron beam evaporation.
[0066] (2) Annealing: anneal the silicon wafer after the aluminum film is deposited in a nitrogen atmosphere at 450° C. for 4 hours to increase the grain size of the deposited aluminum film and improve the bonding degree between it and the substrate.
[0067] (3) Anodizing the aluminum film: in 0.3M oxalic acid, oxidize at a voltage of 40V. Oxidation proceeds to stop at point E.
[0068] (4) Remove the anodic aluminum oxide film formed in step 3 and the silicon dioxide spots on the surface of the silicon substrate: use 6% phosphoric acid to remove the anodic aluminum oxide film in a water bath at 30° C. for 5 hours, and then use 1% hydrofluoric acid Soak the sample in acid for 5 min to remove silicon dioxide spots on the surface of the silicon substrate. The samples were then removed and exposed to air...
Embodiment 3
[0071] (1) Depositing an aluminum film on a silicon wafer: Deposit an aluminum film with a thickness of 2 μm on a single crystal silicon using thermal evaporation equipment.
[0072] (2) Annealing: anneal the silicon wafer after the aluminum film is deposited in a nitrogen atmosphere at 550° C. for 2 h to increase the grain size of the deposited aluminum film and improve the bonding degree between it and the substrate.
[0073] (3) Anodizing the aluminum film: oxidizing at a voltage of 60V in 0.3M sulfuric acid. Oxidation proceeds to stop at point E.
[0074] (4) Remove the anodic aluminum oxide film formed in step 3 and the silicon dioxide spots on the surface of the silicon substrate: use 6% phosphoric acid to remove the anodic aluminum oxide film in a 40°C water bath for 5 hours, and then use 5% hydrofluoric acid Soak the sample in acid for 5 min to remove silicon dioxide spots on the surface of the silicon substrate. The samples were then removed and exposed to air.
[...
PUM
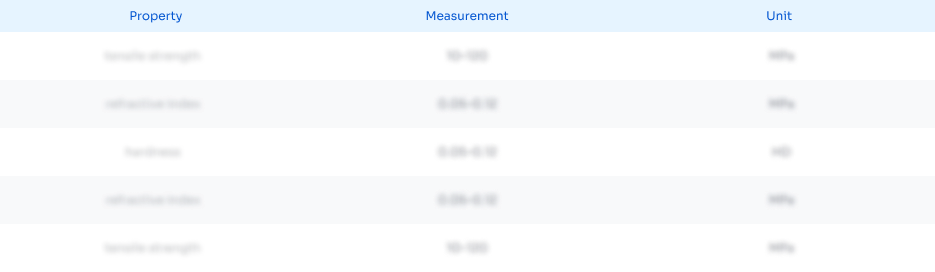
Abstract
Description
Claims
Application Information

- R&D Engineer
- R&D Manager
- IP Professional
- Industry Leading Data Capabilities
- Powerful AI technology
- Patent DNA Extraction
Browse by: Latest US Patents, China's latest patents, Technical Efficacy Thesaurus, Application Domain, Technology Topic, Popular Technical Reports.
© 2024 PatSnap. All rights reserved.Legal|Privacy policy|Modern Slavery Act Transparency Statement|Sitemap|About US| Contact US: help@patsnap.com