Method for drying electric furnace by using molten iron
A furnace method and molten iron technology, applied in the electric furnace furnace process, electric furnace molten iron furnace field, can solve the problems of increasing noise, radiation and dust pollution, affecting refining and continuous casting operations, slow production rhythm, etc., to save power consumption , Improvement of smelting environment and reduction of dust pollution
- Summary
- Abstract
- Description
- Claims
- Application Information
AI Technical Summary
Problems solved by technology
Method used
Examples
Embodiment Construction
[0028] The technical solution of the present invention will be further elaborated below in combination with a preferred embodiment, but these embodiments do not limit the present invention in any way. Any changes made by those skilled in the art in the implementation of the present invention under the inspiration of this specification will fall within the scope of the claims.
[0029] This embodiment involves the oven operation of the CONCAST ultra-high power electric arc furnace with a furnace capacity of 110 tons, and combined with the steel type C70DA to carry out the operation of oven smelting as a whole, specifically including the following steps:
[0030] (1) Pre-lay a layer of MgO ramming material on the bottom surface of the newly built furnace bottom, with a layer thickness of about 8mm;
[0031] (2) Lay a layer of light and thin material on the ramming material, which is wood material and iron sheet, and the layer thickness is about 20cm;
[0032] (3) Add 35 tons of...
PUM
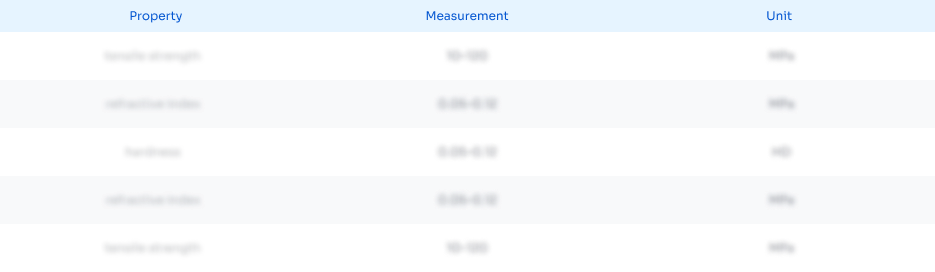
Abstract
Description
Claims
Application Information

- R&D
- Intellectual Property
- Life Sciences
- Materials
- Tech Scout
- Unparalleled Data Quality
- Higher Quality Content
- 60% Fewer Hallucinations
Browse by: Latest US Patents, China's latest patents, Technical Efficacy Thesaurus, Application Domain, Technology Topic, Popular Technical Reports.
© 2025 PatSnap. All rights reserved.Legal|Privacy policy|Modern Slavery Act Transparency Statement|Sitemap|About US| Contact US: help@patsnap.com