Preparation method of ether ester copolymer water reducer
A preparation process and technology of water reducing agent, which are applied in the field of preparation technology of ether ester type polymer water reducing agent, can solve the problem of restricting the application and development of polycarboxylic acid series water reducing agent, difficult to popularize water reducing agent in a large range, and stable in quality. problems such as poor performance, to achieve the effects of easy control of the process, stable product performance and mild reaction conditions
- Summary
- Abstract
- Description
- Claims
- Application Information
AI Technical Summary
Problems solved by technology
Method used
Image
Examples
Embodiment 1
[0021] A) Mix 68.4g of MgO and 28g of diatomaceous earth evenly, add it to 400ml of aqueous solution containing 23g of aluminum chloride, stir for 1hr, wash, dry, calcinate at 500℃ for 1hr, grind and sieving to obtain a Mg-Al composite catalyst. The catalyst powder contains 65% magnesium oxide, 8.4% alumina, and 26.2% diatomaceous earth.
[0022] B) Put 120g of petroleum ether and 60g of dodecanethiol into the reactor, add a mixture of 200g of methyl acrylate and 20g of azobisisobutyronitrile by dripping, dripping for 30min, and react at 70℃ for 5h, Then the heating was stopped, and the reaction mixture was poured into 1 times the mass of the reaction mixture to purify the polymer in deionized water to obtain a polymethyl acrylate with a viscosity average molecular weight of 5000.
[0023] C) Add the product obtained in B) to the above catalyst (the amount is 0.2wt% of the amount of polymethyl acrylate), the ethoxylation temperature is 150°C, and add ethylene oxide (the amount of ...
Embodiment 2
[0025] A) 300ml of an aqueous solution containing 85g of aluminum nitrate and 27g of diatomaceous earth was added dropwise to 150ml of a dispersion containing 58g of CaO, and stirred at room temperature for 1 hour to obtain a mixed catalyst slurry, which was passed through a strong basic anion exchange resin Remove NO 3 - After the ion exchange is completed, the catalyst is separated from the ion resin, dried, calcined at 500° C. for 1 hr, ground and sieved to obtain a Ca-Al composite catalyst. The catalyst powder contains 60% calcium oxide, 12% alumina, and 28% diatomaceous earth.
[0026] B) Add 155g of cyclohexane and 80g of sodium bisulfite into the reactor, add a mixture of 150g of methyl acrylate and 15g of dibenzoyl peroxide by dripping, dripping time 40min, and react at 30℃ for 8h , Then stop heating, pour the reaction mixture system into deionized water twice the mass of the mixture to purify the polymer to obtain polymethyl acrylate with a viscosity average molecular we...
Embodiment 3
[0029] A) Mix 20g MgO with 9g4A zeolite, add it to 500ml of 1.9% gallium nitrate aqueous solution, stir vigorously for 1hr, dry at 110℃ for 2hr, calcinate at 500℃ for 1hr, grind and sieving to obtain a gallium ion-containing MgO Composite catalyst. The catalyst powder contains 61.6% of magnesium oxide, 10.7% of gallium oxide, and 27.7% of 4A zeolite.
[0030] B) Add 320g of tetrahydrofuran and 38g of dithioester into the reactor, add a mixture of 40g of methyl acrylate and 2g of azobisisobutyronitrile by dripping, dripping for 60min, react at 80℃ for 7h, then stop Heating, pour the reaction mixture system into deionized water 5 times the mass of the mixture to purify the polymer to obtain polymethyl acrylate with a viscosity average molecular weight of 90,000.
[0031] C) Add the product obtained in A) to the above catalyst (the amount is 2wt% of the amount of polymethyl acrylate), the ethoxylation temperature is 220°C, and add ethylene oxide (the amount of ethylene oxide and the ...
PUM
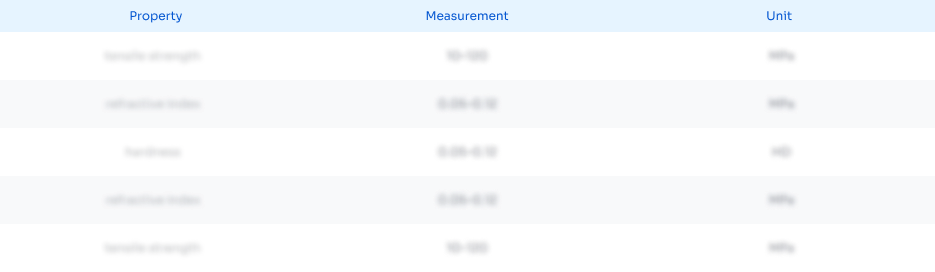
Abstract
Description
Claims
Application Information

- R&D Engineer
- R&D Manager
- IP Professional
- Industry Leading Data Capabilities
- Powerful AI technology
- Patent DNA Extraction
Browse by: Latest US Patents, China's latest patents, Technical Efficacy Thesaurus, Application Domain, Technology Topic, Popular Technical Reports.
© 2024 PatSnap. All rights reserved.Legal|Privacy policy|Modern Slavery Act Transparency Statement|Sitemap|About US| Contact US: help@patsnap.com