Backboard fabricating method
A manufacturing method and backplane technology, applied in the direction of ion implantation plating, coating, metal material coating process, etc., can solve the problems of intergranular cracking, immaturity, and insufficiently uniform grains, and achieve the effect of uniform grains
- Summary
- Abstract
- Description
- Claims
- Application Information
AI Technical Summary
Problems solved by technology
Method used
Image
Examples
Embodiment Construction
[0035] In order to make the above objects, features and advantages of the present invention more comprehensible, specific implementations of the present invention will be described in detail below in conjunction with the accompanying drawings.
[0036] In the following description, many specific details are set forth in order to fully understand the present invention, but the present invention can also be implemented in other ways than those described here, so the present invention is not limited by the specific embodiments disclosed below.
[0037] As mentioned in the background art section, the internal structure of the backplane produced in the prior art is uneven and not refined enough, and distortion and deformation appear. In order to overcome the above-mentioned defects, the present invention provides a manufacturing method of the backboard, which changes the internal organizational structure of the backboard so that the organizational structure of the backboard is more ...
PUM
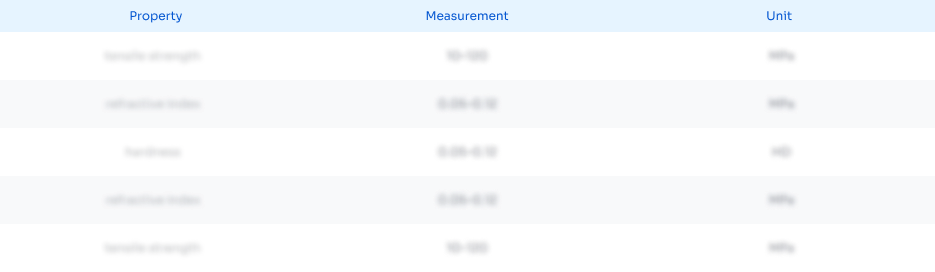
Abstract
Description
Claims
Application Information

- R&D
- Intellectual Property
- Life Sciences
- Materials
- Tech Scout
- Unparalleled Data Quality
- Higher Quality Content
- 60% Fewer Hallucinations
Browse by: Latest US Patents, China's latest patents, Technical Efficacy Thesaurus, Application Domain, Technology Topic, Popular Technical Reports.
© 2025 PatSnap. All rights reserved.Legal|Privacy policy|Modern Slavery Act Transparency Statement|Sitemap|About US| Contact US: help@patsnap.com