Gradient arsenic removing method for high-arsenic metallurgical wastes
A metallurgical waste and gradient technology, applied in the direction of improving process efficiency, can solve the problems of not meeting large-scale production, poor pyrolysis separation effect, serious secondary pollution, etc., and achieves low production cost and reduced arsenic content. , the effect of reducing waste water discharge
- Summary
- Abstract
- Description
- Claims
- Application Information
AI Technical Summary
Problems solved by technology
Method used
Image
Examples
Embodiment 1
[0035] Raw material, high arsenic fumes produced by a copper smelter in Jiadi, its main components are (%): As 25.38%, Cu 4.41%, Pb 45.28%. Take 100g of the above raw material, add 400mL of water, then raise the temperature to 95°C, stir at constant temperature for 3 hours, and then heat filter to obtain 86.43g of water leaching residue with arsenic content of 13.88%, and the arsenic removal rate is 52.73%. The leaching solution was cooled and crystallized to precipitate 11.27 g of arsenic trioxide. The water leaching slag continues to adopt oxidative acid leaching, the oxidizing agent is hydrogen peroxide, and the composition of the leaching solution is: (2mol / L H 2 SO 4 solution 200mL)+(30%H 2 o 2100mL), the leaching temperature was 70°C, and the mixture was stirred at constant temperature for 4 hours. The arsenic content of filter residue obtained after oxidative acid leaching was 1.61%, and the leaching rate was 90.4%. Combining water leaching and acid leaching, the t...
Embodiment 2
[0037] Raw material, high arsenic fume produced by a lead-zinc smelter in Yidi, its main components (%): As 21.25%, Pb 20.43%, Cu 3.14%, Zn 7.28%. Take 100g of the above-mentioned raw material, add water 300mL, then raise the temperature to 85°C, stir at constant temperature for 4 hours, then heat filter, the arsenic content in the water leaching residue is 11.54%, and the leaching rate is 54.30%. The water leaching slag continues to be leached by oxidative acid, the oxidant is hydrogen peroxide, and the composition of the leaching solution is: (1mol / L H 2 SO 4 solution 300mL)+(15%KMn 2 o 4 100mL), the leaching temperature was 70°C, and the mixture was stirred at constant temperature for 4 hours. The arsenic content of filter residue obtained after oxidative acid leaching was 1.42%, and the leaching rate was 91.3%. Combining water leaching and acid leaching, the total arsenic removal rate is 95.10%. The filtrate after water immersion is condensed and crystallized to prec...
Embodiment 3
[0039] Raw material, high-arsenic anode slime produced by an electrolysis plant in Bingdi, its main components (%): As 13.28%, Pb 22.15%, Cu 3.23%. Take 100g of the above-mentioned raw materials, add 500mL of water, then raise the temperature to 90°C, stir at constant temperature for 3 hours, then heat filter, the arsenic content in the water leaching residue is 7.89%, and the leaching rate is 43.43%. The water leaching slag continues to adopt oxidative acid leaching, the oxidant is hydrogen peroxide, and the composition of the leachate is: (0.8mol / L H 2 SO 4 solution 300mL)+(15%NaClO 4 100mL), the leaching temperature was 27°C (room temperature), and stirred for 4 hours. The arsenic content of filter residue obtained after oxidative acid leaching is 1.23%. Combining water leaching and acid leaching, the total arsenic removal rate is 93.21%. The filtrate after water immersion is condensed and crystallized to precipitate arsenic trioxide product with a purity of 92.2%.
PUM
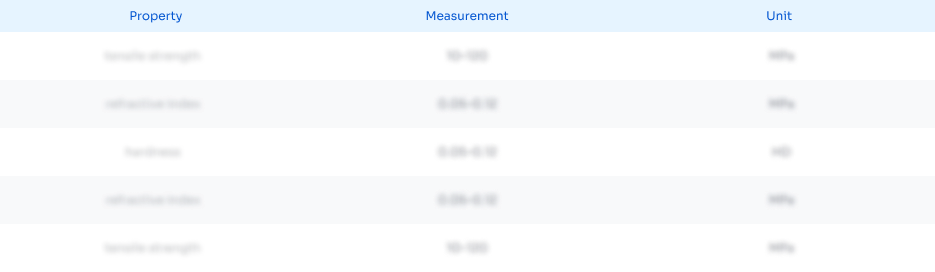
Abstract
Description
Claims
Application Information

- R&D
- Intellectual Property
- Life Sciences
- Materials
- Tech Scout
- Unparalleled Data Quality
- Higher Quality Content
- 60% Fewer Hallucinations
Browse by: Latest US Patents, China's latest patents, Technical Efficacy Thesaurus, Application Domain, Technology Topic, Popular Technical Reports.
© 2025 PatSnap. All rights reserved.Legal|Privacy policy|Modern Slavery Act Transparency Statement|Sitemap|About US| Contact US: help@patsnap.com