Method for preparing lithium ion battery cathode material in-situ carbon coated lithium manganese borate composite material
A technology of carbon-coated lithium manganese borate and carbon composite materials, applied in battery electrodes, circuits, electrical components, etc., can solve problems such as unsatisfactory discharge specific capacity of lithium manganese borate, easy oxidation of lithium manganese borate, and poor cycle stability. Achieve good cycle stability, easy to implement, and improve the effect of electrical conductivity
- Summary
- Abstract
- Description
- Claims
- Application Information
AI Technical Summary
Problems solved by technology
Method used
Image
Examples
Embodiment 1
[0035]Embodiment 1, the composite material (h-LiMnBO of hexagonal manganese borate lithium and carbon 3 C) Preparation
[0036] Add 0.4413g of lithium hydroxide, 1.1498g of manganese carbonate, and 0.6190g of boric acid into a 0.3mol / L ethanol solution of ascorbic acid (Li:Mn:B:carbon source=1.05:1:1:0.6), ball mill for 6h, and the above The slurry was dried in an oven at 80°C to obtain a powder. Under an argon protective atmosphere, the temperature was raised to 300°C at a rate of 10°C / min for 5 hours of pre-calcination to obtain a precursor; the precursor was ground, and then The same heating rate of 10°C / min was raised to 700-750°C for calcination for 10h (argon protection was required during this process). After naturally cooling down to room temperature, the obtained sample is a composite material of hexagonal manganese lithium borate and carbon (h-LiMnBO 3 C), the XRD diffraction pattern of the product is as follows figure 1 shown. It can be used as the positive elec...
Embodiment 2
[0037] Embodiment 2, the composite material (m-LiMnBO of monoclinic manganese lithium borate and carbon 3 C) Preparation
[0038] Lithium carbonate 0.7389g, manganese carbonate 2.2990g, boric acid 1.2365g and citric acid 0.2414g (Li: Mn: B: carbon source = 1: 1: 1: 0.05 molar ratio) are added in the ball mill jar, after adding 20ml of acetone Grinding for 6 hours, drying the above slurry at 60°C to obtain a powder, in an argon atmosphere, raising the temperature to 250°C at a rate of 10°C / min for 3 hours of pre-calcination, grinding the precursor, and then raising the temperature at the same rate The temperature was raised to 500°C for 10 hours at a rate of 10°C / min (argon protection was required during this process). After naturally cooling down to room temperature, the obtained sample is a composite material of monoclinic manganese lithium borate and carbon (m-LiMnBO 3 C), the XRD diffraction pattern of the product is as follows figure 2 shown. It can be used as the pos...
Embodiment 3
[0039] Embodiment 3, the composite material (h-LiMnBO of hexagonal manganese borate lithium and carbon 3 C) Preparation
[0040] Add 0.3696g of lithium carbonate, 1.1495g of manganese carbonate, and 0.6183g of boric acid into the ball mill jar, then add 0.1207g of citric acid (Li:Mn:B:carbon source=1:1:1:0.05), and acetone is used as a dispersant , ball milled for 5 hours, dried the above slurry at 60°C to obtain a powder, in an argon atmosphere, heated up to 250°C at a heating rate of 10°C / min for 3h pre-calcination, ground the precursor, and then The heating rate is 10°C / min, and the temperature is raised to 750°C for 15 hours of calcination (argon protection is required during this process). After naturally cooling down to room temperature, the obtained sample is a composite material of hexagonal manganese lithium borate and carbon (h-LiMnBO 3 C), the XRD diffraction pattern of the product is as follows Figure 4 (d) shown. It can be used as the positive electrode activ...
PUM
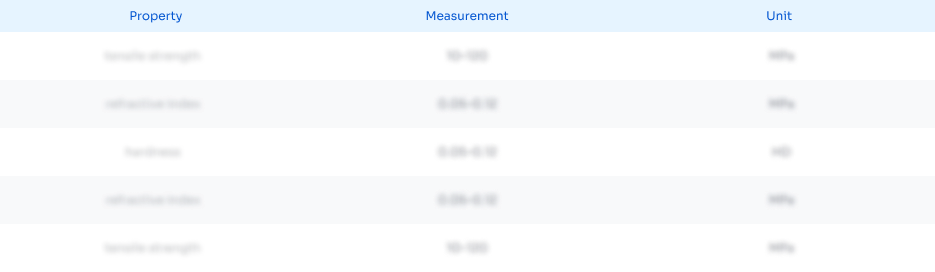
Abstract
Description
Claims
Application Information

- Generate Ideas
- Intellectual Property
- Life Sciences
- Materials
- Tech Scout
- Unparalleled Data Quality
- Higher Quality Content
- 60% Fewer Hallucinations
Browse by: Latest US Patents, China's latest patents, Technical Efficacy Thesaurus, Application Domain, Technology Topic, Popular Technical Reports.
© 2025 PatSnap. All rights reserved.Legal|Privacy policy|Modern Slavery Act Transparency Statement|Sitemap|About US| Contact US: help@patsnap.com